Существует множество замечательных полимеров, но даже самые прочные из них можно сделать еще прочнее с помощью волоконных добавок. Рассказываем о стекло- и угленаполненных композитах.
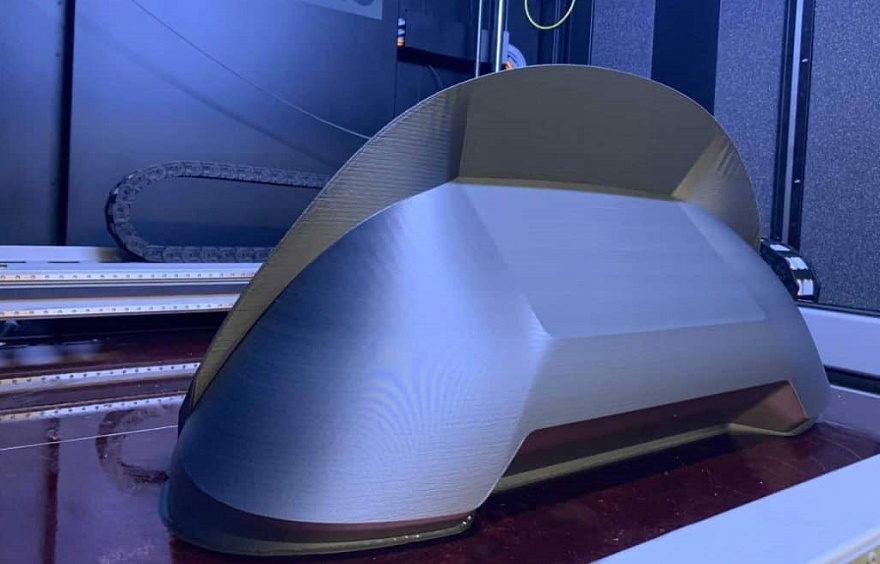
Содержание:
1. Что такое армированные композиты
Армированные композиты — это полимеры с волоконными добавками, повышающими физико-механические характеристики. Наиболее распространенные варианты наполнителей — стекло- и углеволокно, хотя бывают и более экзотичные варианты, например базальт или кевлар. Далеко не все композиционные филаменты создаются под промышленные нужды. Многие композиты предназначены для декоративных целей: филаменты с наполнителями из древесной муки, металлического или керамического порошка могут служить имитаторами древесины, металлов и фарфора.
Некоторые из порошковых наполнителей тоже обеспечивают дополнительную функциональность: металлические и углеродные наполнители могут придавать композиту электропроводность и антистатические свойства, композиты с высоким содержанием металлического порошка можно использовать для дальнейшего отжига и спекания в цельнометаллические изделия. Вариантов масса, но сегодня мы затронем конкретно композиты, армированные короткими волокнами.
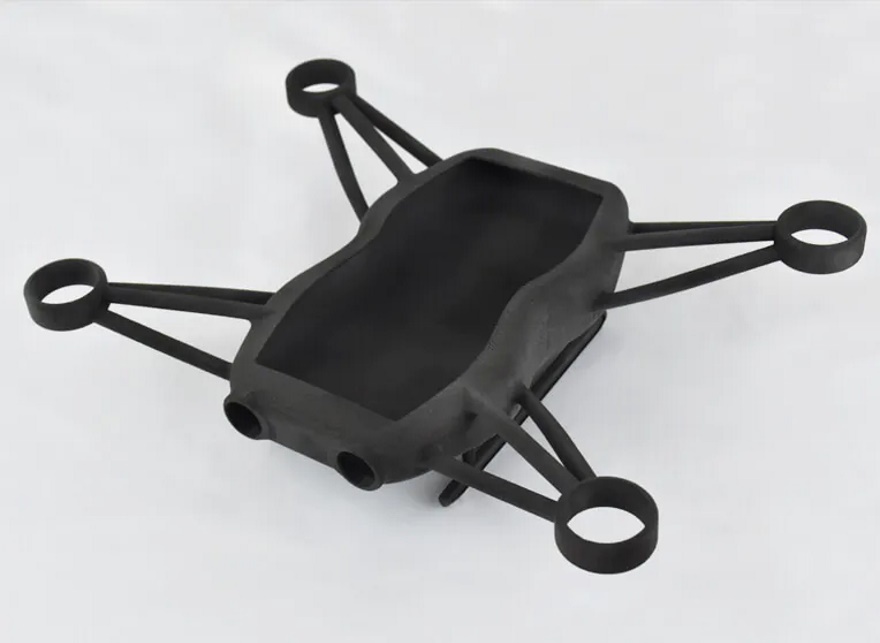
Здесь тоже необходимо сделать пояснение: есть две разновидности 3D-печати филаментами, использующие короткое, рубленое волокно и непрерывные волокна. Второй вариант занимает довольно узкую нишу и требует специализированного оборудования — 3D-принтеров с двумя головками, где одна наносит основной полимер, а вторая укладывает на каждый слой и обрезает углеродную нить, как правило тоже в полимерной оболочке — для лучшей адгезии. Самые известные производители таких систем — американская Markforged и российско-люксембургская Anisoprint.
Наибольшей же популярностью пользуются композиты с наполнителями из коротких волокон, так как для работы с ними специальное оборудование не требуется. Кое-какие требования все же есть: сопла обязательно должны быть из износостойкого материала, ибо обычные латунные очень быстро стачиваются. Самый распространенный и недорогой вариант — фильеры из закаленной стали, но на рынке есть альтернативные решения, более дорогие, но в то же время долговечные — с наконечниками или покрытиями из искусственного рубина, сапфира или алмаза, либо карбида вольфрама.

Помимо этого не помешает использовать фидеры (подающие механизмы) с шестернями из закаленной стали, так как они тоже подвержены износу, хоть и в меньшей степени. Наконец, в зависимости от полимерной матрицы, то есть основного материала, могут потребоваться высокотемпературные хотэнды и/или термокамеры.
Повышенная прочность — далеко не единственное преимущество угле- и стеклонаполненных пластиков. Волоконные наполнители еще и помогают стабилизировать геометрию 3D-печатных изделий. Все полимеры подвержены термоусадке, но в разной степени. Наиболее привередливые термопласты, такие как акрилонитрилбутадиенстирол (ABS) или нейлон, при охлаждении могут расслаиваться и деформироваться, вплоть до отлипания от столика во время 3D-печати. Эти недостатки можно победить прогревом столика, использованием термокамеры для стабилизации фоновой температуры и использованием клея для повышения адгезии, но размерная точность все равно может страдать, а в инженерной 3D-печати это зачастую неприемлемо — части не будут стыковаться, детали не будут вставать на посадочные места, дистанция между техническими отверстиями для крепежных элементов будет сбиваться, и так далее. Угле- и стекловолоконные наполнители, с другой стороны, заметно снижают усадку, как бы препятствуя сжатию материала изнутри.

Классический пример композита с пониженной усадкой — REC FormaX, где полимерной матрицей служит как раз ABS, а роль наполнителя играет углеродное волокно.
Таких материалов у нас много, и распределены они по нескольким линейкам.
2. Линейка X-line
Первая — X-line, разработанная нами в сотрудничестве с российским производителем 3D-принтеров PICASO 3D. Они предлагают наши композиты как стандартную опцию. Всего в этой линейке пять разновидностей.
REC FormaX
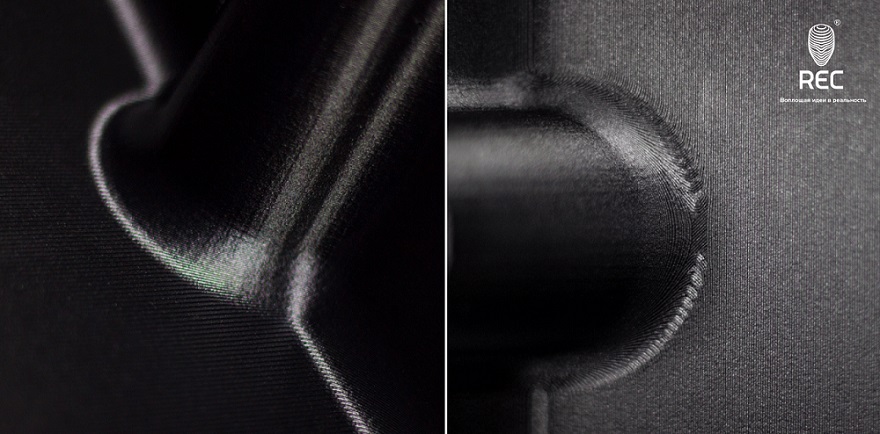
Упомянутый выше материал из акрилонитрилбутадиенстирола (ABS) с углеволоконным наполнителем, повышающим прочность на сжатие и растяжение, жесткость и размерную точность. FormaX обладает широким диапазоном эксплуатационных температур — от -60°С до +105°С. Что интересно, помимо технических приложений этот материал нашел применение и в декоративной 3D-печати. Дело в том, что после укладки композит образует приятные на ощупь шершавые поверхности, отлично скрывающие слоистость и тем самым позволяющие обходиться без сглаживания.
REC UltraX
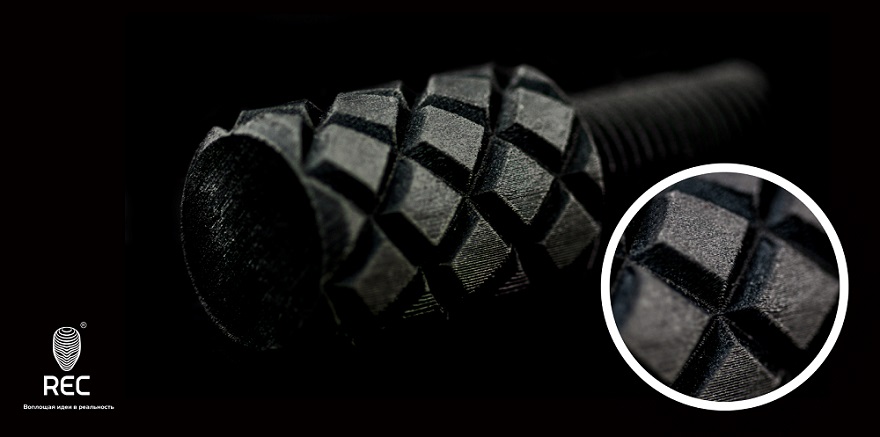
Тоже углеволоконный композит, но на этот раз на основе нейлона — полиамида-6. Нейлоны славятся высокой прочностью, а тридцатипроцентная доля углеродного волокна повышает как прочность, так и жесткость. REC UltraX отлично подходит для 3D-печати функциональных прототипов и нагруженных деталей с продолжительной эксплуатацией при температурах до 110°С. Только не забывайте просушивать филамент непосредственно перед 3D-печатью, так как полиамиды весьма гигроскопичны.
Printamid 1284
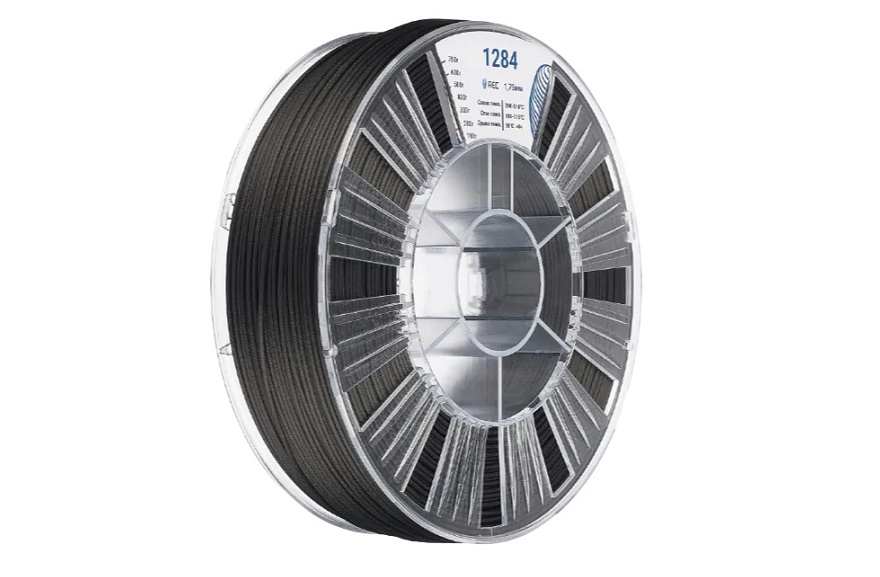
Еще один угленаполненный полиамид, созданный совместно с нашим партнерским предприятием 3D Solutions и предназначенный специально для крупноформатных промышленных 3D-принтеров. Printamid 1284 материал можно приобрести как на стандартных катушках массой 750 грамм нетто, так и больших двухкилограммовых для 3D-печати крупногабаритных изделий. Если у вас нет доступа к здоровенному 3D-принтеру, но очень нужно напечатать большой предмет, обращайтесь к нам, и мы задействуем 3D-принтер Colossus с областью построения 2,7х1,25х1,5 метра.
REC PPX
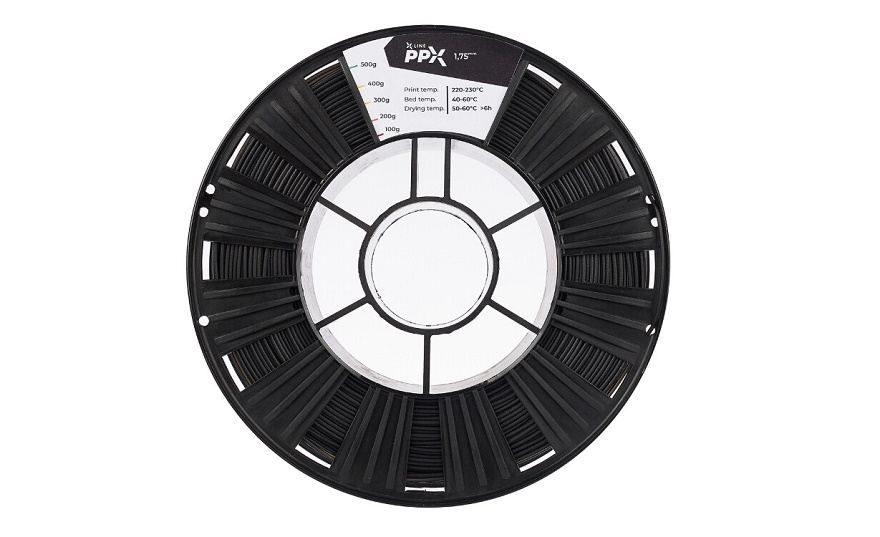
Полипропилен — крайне заманчивый полимер с полным букетом полезных свойств — высокой прочностью, ударной стойкостью, нетоксичностью, износостойкостью, сопротивлением пластическим деформациям, невосприимчивостью к большинству распространенных химикатов и ультрафиолетовому излучению. Одна беда: полипропилен сильно усаживается. Усложняется это проблема еще и тем, что полипропилен мало к чему липнет, если не считать самого полипропилена, так что адгезионные средства работают не особо эффективно. Оптимальный вариант — стабилизация размеров как за счет поддержания повышенной температуры в термокамере, так и добавления армирующих волокон. REC PPX — как раз такой угленаполненный полипропиленовый композит с пониженной усадкой и сохранением всех привлекательных свойств.
REC GF Max
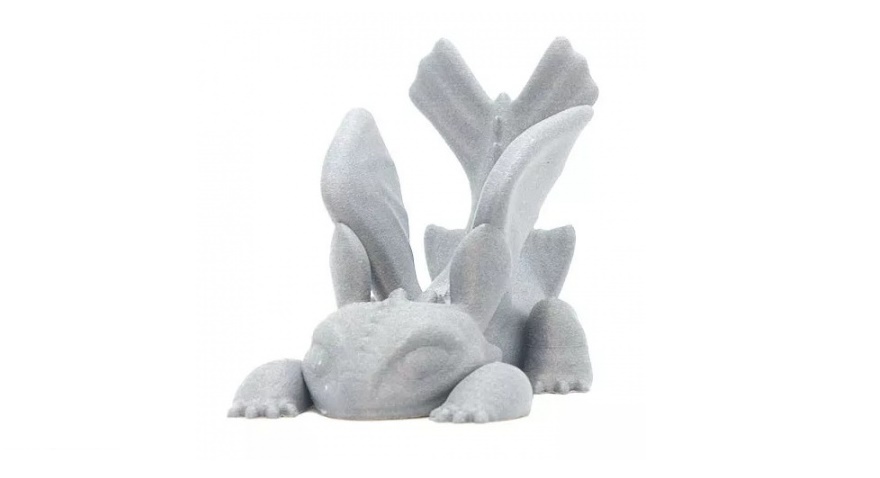
В составе этого композита используется уже стекловолоконный наполнитель в матрице из полиэтилентерефталатгликоля (ПЭТГ). ПЭТГ — один из самых популярных полимеров в экструзионной 3D-печати — как любительской, так и профессиональной. ПЭТГ относительно недорог, прочен, обладает отличной ударной стойкостью и выдерживает приличные температуры. Все мы хорошо знакомы с этим пластиком, так как из него изготавливают пищевую упаковку, в том числе пластиковые бутылки. Не менее важное преимущество ПЭТГ — простота 3D-печати. ПЭТГ не требует особо горячих хотэндов и не очень сильно усаживается, так что можно обойтись без термокамеры. Высокая стойкость к ударным нагрузкам объясняется вязкостью этого полимера, так что при укладке ПЭТГ может образовывать паутину, но это легко решается точной настройкой ретракта или просто удалением волосков вручную. Стекловолоконный наполнитель же дополнительно повышает прочность и жесткость и делает материал пригодным для изготовления нагруженных компонентов.
3. Линейка Clotho
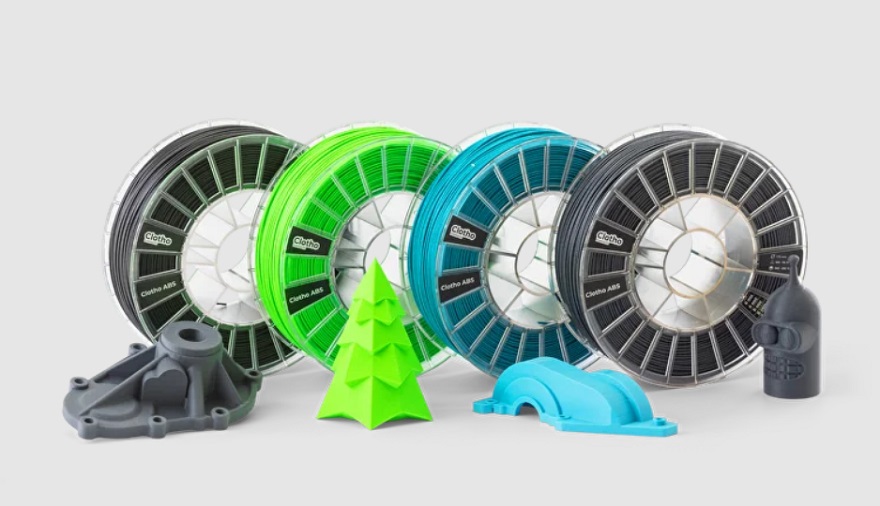
Линейка Clotho — результат еще одной коллаборации, на этот раз с красноярским производителем 3D-принтеров Imprinta. Собственно, композит здесь только один, зато доступный в четырех оттенках — «оригинальном» зеленом (Imprinta очень любит этот цвет), аквамариновом, черном и темно-сером. Сам же материал — стеклонаполненный АБС с тринадцатипроцентной долей армирующего волокна, отлично подходящий как для технических, так и художественных задач. Большие двухкилограммовые катушки для больших 3D-принтеров тоже доступны.
4. Разное, но важное
Еще три варианта не принадлежат к определенным линейкам, но сами по себе очень интересны.
REC Friction
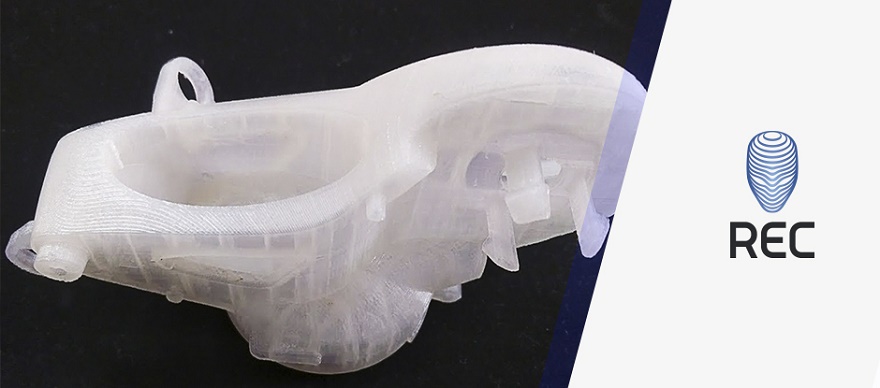
Этот материал — стеклонаполненная альтернатива угленаполненным нейлонам. Матрицей служит очень стойкий к истиранию полиамид-12. REC Friction выдерживает эксплуатацию при температурах от от -60°С до +90°С и отлично справляется с высокими нагрузками, в том числе циклическими.
PEEK CF и PEEK GF
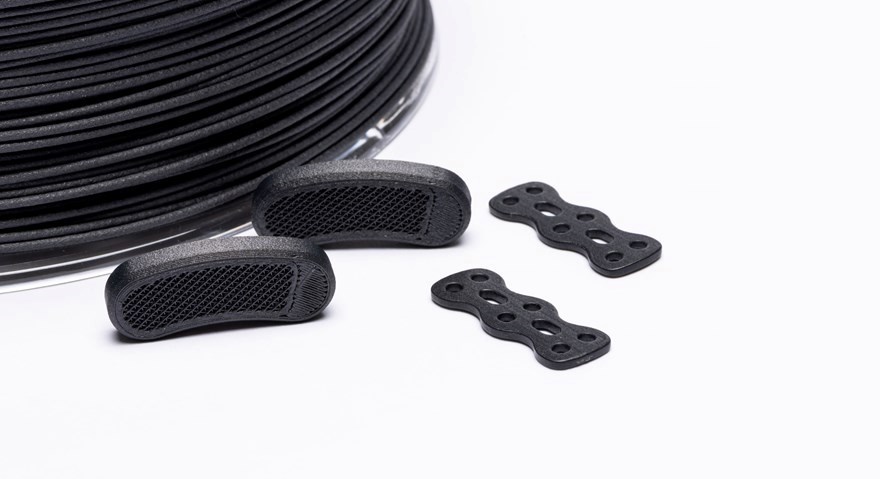
Композиты для очень серьезных задач, выполненные на основе полиэфирэфиркетона (PEEK). PEEK — тугоплавкий конструкционный термопласт, выдерживающий эксплуатационные температуры до 275°С, а по прочности сравнимый и даже превосходящий алюминиевые сплавы. PEEK обладает высокой химической инертностью, негорюч, в чистом виде нетоксичен. Конечно, для работы с настолько тугоплавкими полимерами требуются уже 3D-принтеры с высокотемпературными хотэндами, например системы линейки Designer X Series 2 от PICASO. Угле- и стекловолоконные наполнители в PEEK CF и PEEK GF дополнительно повышают прочностные характеристики, а заодно помогают бороться с деформациями из-за усадки, чтобы дорогой материал не уходил в отбраковку. Подробнее про работу с PEEK читайте в отдельной статье.
REC rPETG
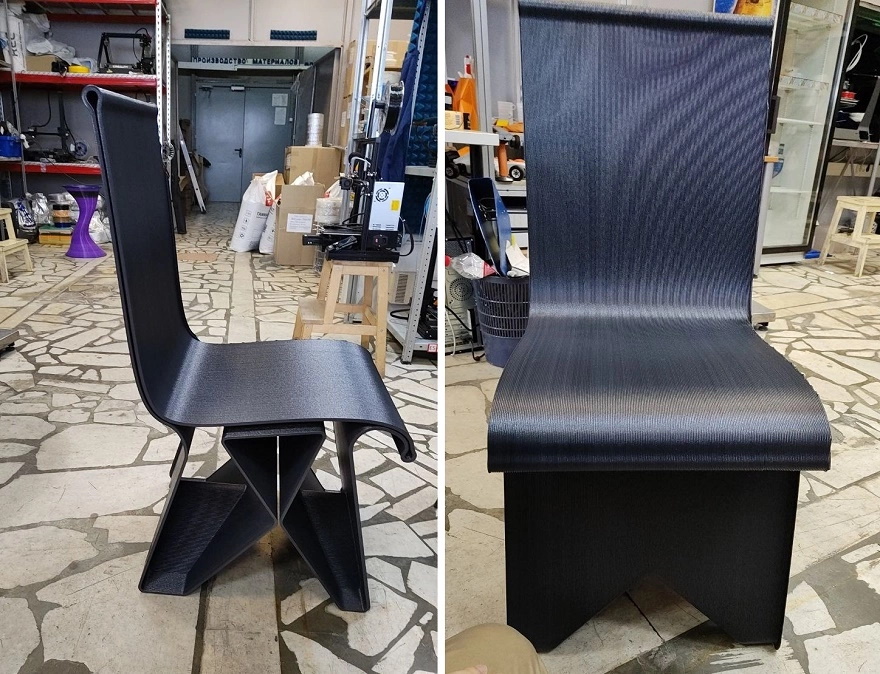
И наконец, композит, созданный для больших идей на малом бюджете. Это комбинация переработанного полиэтилентерефталатгликоля (PETG) и стекловолокна. ПЭТГ, как мы уже говорили — очень популярный материал, а стеклонаполненный композит на основе ПЭТГ добавлен в линейку X-line под наименованием GF MAX. rPETG — бюджетная альтернатива, выполненная из вторичного полимерного сырья. К серьезному снижению прочностных характеристик переработка не ведет, а добавление армирующих волокон с лихвой покрывает любые потери. Стульчик на иллюстрации выполнен как раз из этого композита на крупноформатном 3D-принтере пермской компании F2 Innovation, с которой мы регулярно участвуем в выставках.
5. Оборудование
Последний вопрос — на чем печатать. Для большинства композитов подойдут 3D-принтеры с температурой хотэндов в районе 300°С. Обязательное условие — износостойкие сопла. Термокамеры желательны и в некоторых случаях просто необходимы.
Bambu Lab X1 Carbon и X1E
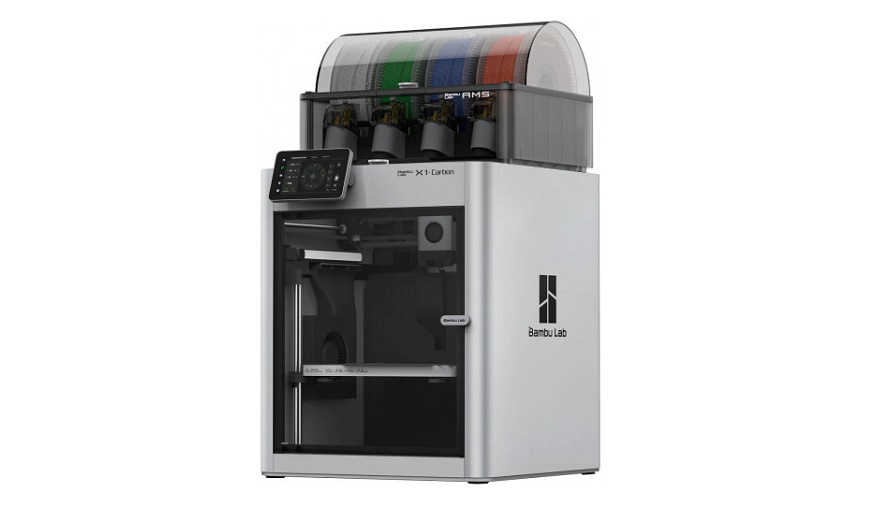
3D-принтеры от Bambu Lab пользуются огромным спросом благодаря высокой степени автоматизации и высокому качеству 3D-печати. По факту эти системы наиболее близки к реализации концепции «печати из коробки». В линейке Bambu Lab есть две системы, оптимизированные под 3D-печать композитами, хотя это далеко не промышленное оборудование. Скорее, это 3D-принтеры для хорошо обеспеченных любителей и студий 3D-печати, тем более что эти аппараты при наличии системы автоматической смены филамента умеют печатать разноцветные изделия.
X1 Carbon — вариант флагманской системы X1, но с износостойкими деталями, а X1E — дальнейшее развитие с упором на профессиональный сегмент, с повышенной температурой экструзии и другими усовершенствованиями. Главное ограничение — температурный режим. X1 Carbon переваривает пластики на температурах до 300°С, а X1E — до 320°С. Для большинства композиционных материалов этого достаточно, но для более тугоплавких полимеров вроде полиэфирэфиркетона или полисульфона потребуется что-то посолиднее.
PICASO Designer X Series 2
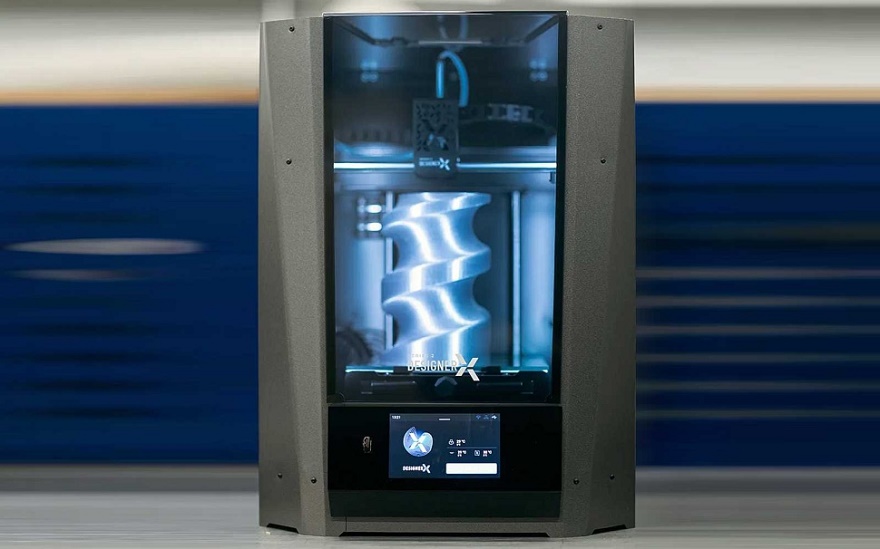
Посолиднее можно найти у PICASO 3D. Зеленоградская компания предлагает целую линейку 3D-принтеров второго поколения на технологической платформе Designer X, ориентированную как раз на 3D-печать тугоплавкими полимерами. Всего в линейке четыре системы в двух парах. В каждой паре есть одно- и двухэкструдерный вариант, последние помогают печатать с использованием специализированных опорных материалов, например водорастворимого поливинилового спирта. Второе отличие — полезный объем: 3D-принтеры стандартного размера имеют область построения до 201х201х210 мм, а варианты XL — до 360х360х610 мм.
Необходимость в повышенной мощности и соблюдении более строгих температурных режимов здесь учтена. Все четыре аппарата оснащены экструдерами с максимальной температурой хотэндов до 410°С, а вдобавок еще и термостатированными камерами с активной регулировкой фоновой температуры до 80°С. Теоретически этого хватает для работы с любыми полимерами и композитами, даже самыми термостойкими.
Imprinta Hercules
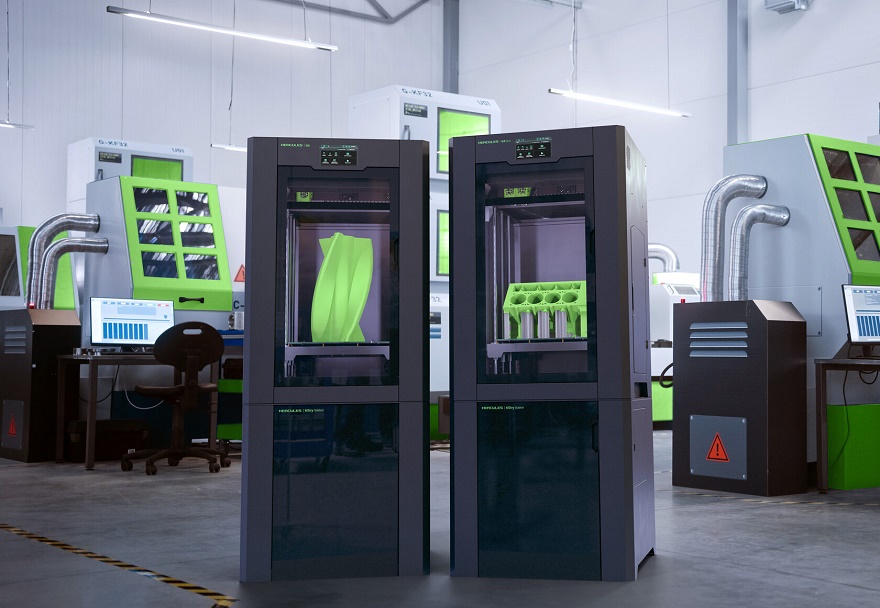
Нечто подобное 3D-принтерам от PICASO есть и у красноярской компании Imprinta. Предприятие предлагает системы Hercules G3 иHercules G4 с рабочими объемами 300х200х300 мм и 400х300х610 мм и максимальной температурой экструдеров 420°С. Двухэкструдерные варианты также доступны.
F2 Innovations
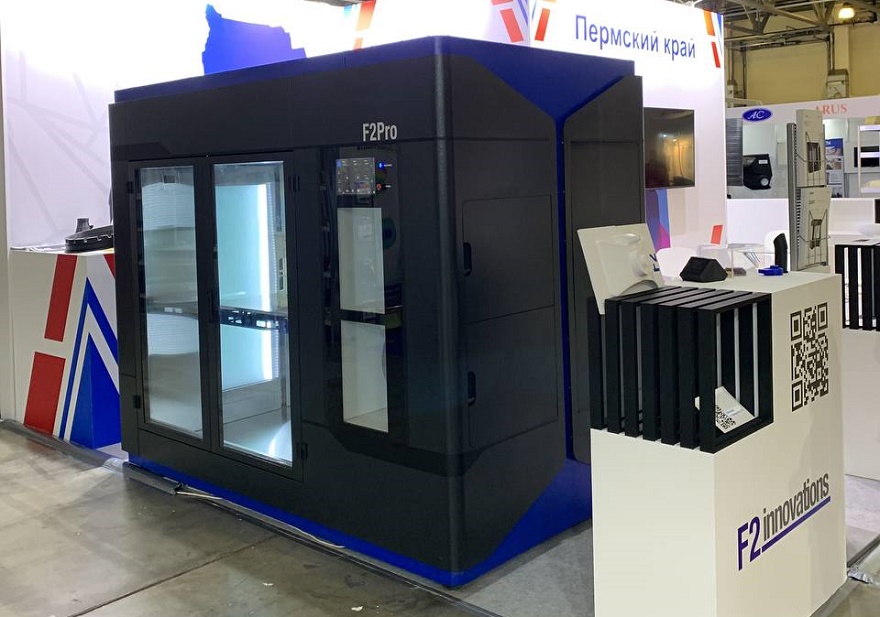
Пермская компания «Ф2 Инновации» ориентируется уже на промышленный сектор. Температуры хотэндов достигают 550°С, не только позволяя работать с любыми термопластами, но и повышая производительность. Термокамеры тоже оснащаются активным подогревом для борьбы с усадкой и прогреваются в плоть до внушительных 200°С, в зависимости от модели. Помимо этого некоторые модели оборудования от F2 Innovations способны работать не только с филаментами, но и гранулятами.
Остались вопросы? Свяжитесь с нами, и специалисты REC будут рады предоставить подробную консультацию по выбору оборудования и расходных материалов под конкретные задачи.
Чтобы написать отзыв нужно авторизоватся
Вход через социальные сети