Композиционные материалы используются в FDM 3D-печати достаточно давно, а последние годы пользуются особенной популярностью ввиду быстро растущего ассортимента и функциональности. Рассказываем об основах и ключевых моментах 3D-печати композитами.
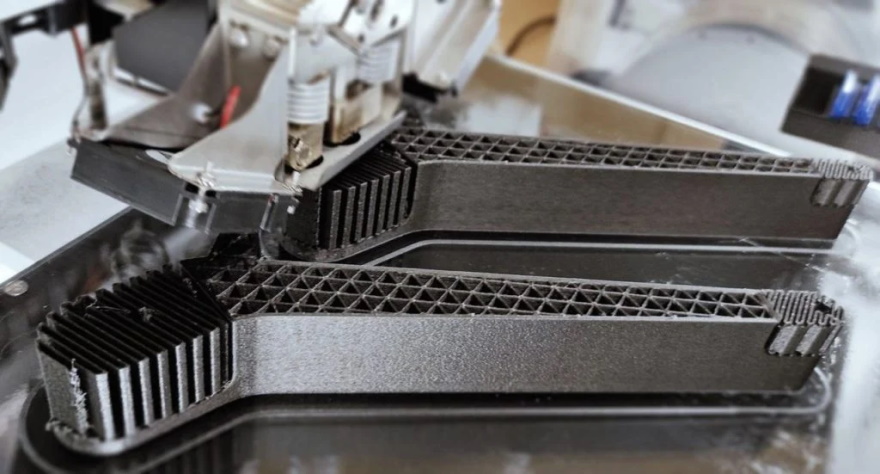
Содержание:
- Армированные композиты
- Материалы с улучшенной эстетикой
- Функционально-модифицированные материалы
- Выбор диаметра сопла
- Выбор материала сопла
- Скорость и температура печати
- Адгезия со столиками
- Хрупкость филаментов
Композиционные филаменты состоят из полимерной матрицы (основы) и наполнителей в виде порошков или волокон. Назначение наполнителей может быть разным — от повышения физико-механических характеристик до улучшения внешнего вида 3D-печатных изделий или даже добавления новых свойств, например электропроводности.
Такие образом, композиционные филаменты можно разделить на три категории — армированные композиты, материалы с улучшенной эстетикой и функционально-модифицированные материалы.
1. Армированные композиты
Армирование обычно производится за счет добавления волокон, повышающих механические и физические свойства композита. Полимерная основа может быть практически любой, а наполнителем обычно служит стекловолокно, углеродное волокно или параарамидные волокна.
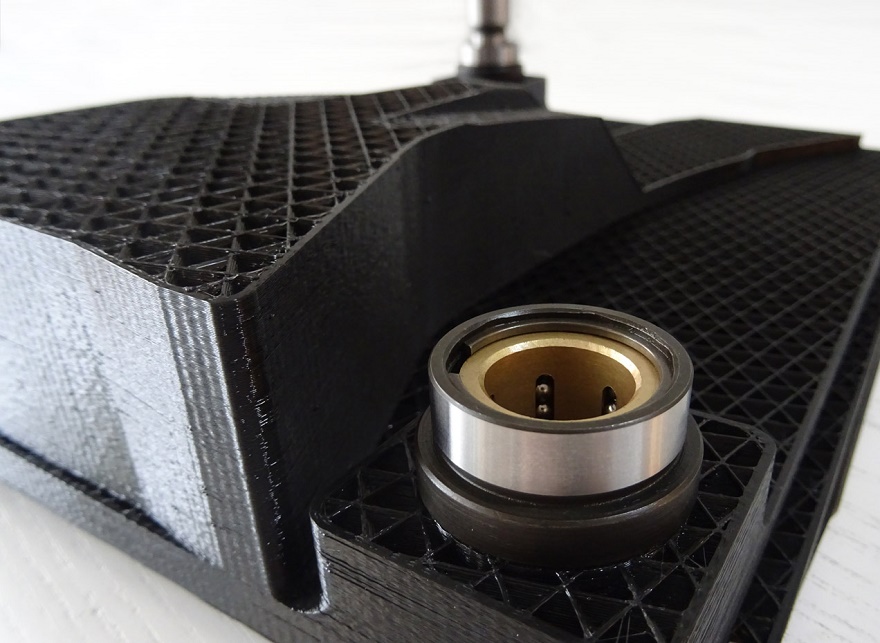
Стекловолокно повышает прочность материала на растяжение и изгиб, а заодно несколько повышает максимальные эксплуатационные температуры и, таким образом, деформационную теплостойкость.
Углеродное волокно аналогичным образом повышает теплостойкость и прочность на растяжение и изгиб, но к тому же увеличивает жесткость материала.
Арамидное волокно отличается прежде всего высокой прочностью, ударной стойкостью и сопротивлением механической усталости. Арамиды (ароматические полиамиды) в целом широко используются в производстве нагруженных функциональных компонентов. Самый известный пример арамида — кевлар.
Полимерной основой наиболее часто служат полиамиды (нейлоны), например угленаполненный REC UltraX или стеклонаполненный REC Friction, хотя бывают и другие варианты — на основе акрилонитрилбутадиенстирола (угленаполненный REC FormaX или Clotho ABS), полиэтилентерефталатгликоля (стеклонаполненные REC GF Max и REC rPETG GF), полипропилена (REC PPX с наполнителем из углеродных трубок) и даже тугоплавкого конструкционного термопласта полиэфирэфиркетона (угленаполненный REC PEEK CF).
В большинстве случаев процентное содержание армирующих волокон в филаментах колеблется в пределах 5-20%. Более высокие доли возможны, но чреваты проблемами с экструзией при использовании сопел относительно малого диаметра.
2. Материалы с улучшенной эстетикой
В этих композитах волоконные или порошковые добавки служат повышению привлекательности и зачастую имитации других материалов, например древесины, керамики или металлов. Наполнители в основном делятся на пять категорий — древесные, минеральные, металлические, растительные и люминофорные.
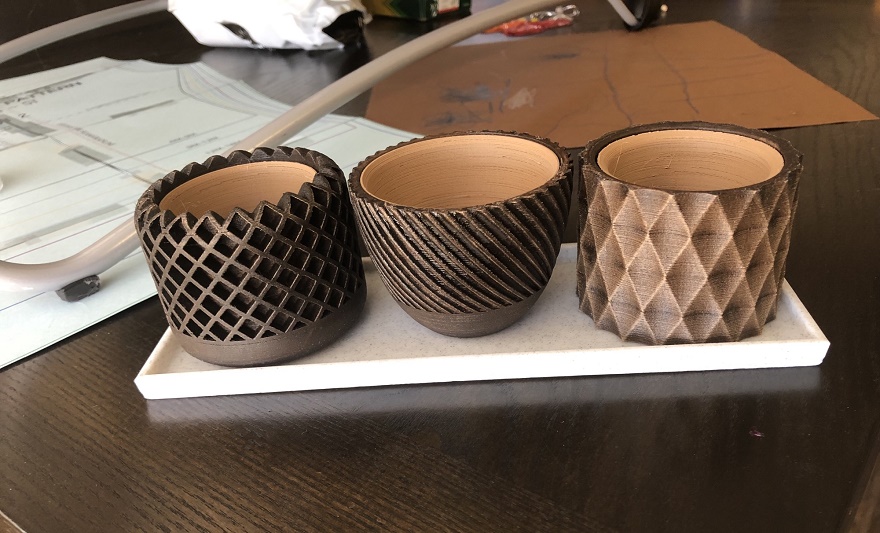
Древесные волокна позволяют имитировать разные сорта древесины.
Минеральные наполнители в виде порошков делают итоговый композит схожим с керамикой, различными горными породами или глиной. Наиболее часто в этой роли используется гипс с разными красителями.
Металлическое наполнители могут как придавать композиту схожесть с металлами, так и превращать полимерный композит в сырье для производства цельнометаллических изделий. Такие процессы подразумевают 3D-печать полимер-металлических заготовок с последующим отжигом связующего полимера и спеканием в цельнометаллические детали. Доля наполнителя в последнем случае может превышать 80%, в филаментах для 3D-печати декоративных изделий процентное содержание металлического наполнителя значительно ниже.
Растительные волокна обычно используются в связке с полилактидом (PLA), помогая получать матовые поверхности.
Люминофорные добавки обеспечивают свечение композитов в темноте. Наиболее часто в этом качестве используется порошок алюмината стронция с характерным зеленым свечением.
В большинстве случаев подобные декоративные композиты изготавливаются на основе полилактида: этот полимер не обладает высокими физико-механическими характеристиками, зато неприхотлив в работе и к тому же дает низкую остаточную зольность, когда речь идет о 3D-печати полимер-металлических заготовок.
Что интересно, материалы из категории армированных композитов все чаще используются в роли декоративных, так как волоконные наполнители дают приятные на ощупь, немного шершавые поверхности и отлично маскируют слои, позволяя обходиться без механической постобработки. В любом случае, повышенная прочность таких материалов не вредит даже при 3D-печати сувениров или декора.
3. Функционально-модифицированные материалы
В некоторых случаях добавки придают конечному композиту свойства, нехарактерные для исходной полимерной основы.
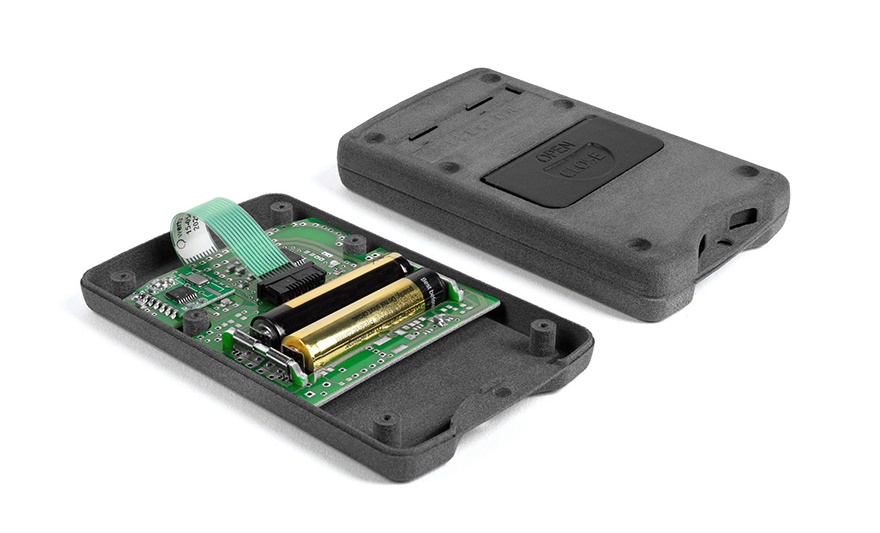
Например, за счет графеновых, борон-карбидных или ферромагнитных добавок можно получать материалы с повышенной электрической проводимостью, антистатическими и магнитными свойствами. Такие материалы относительно редки ввиду высокой стоимости и узкой специализации.
4. Выбор диаметра сопла
Диаметр сопла — один из важнейших параметров, так как слишком малый диаметр с высокой долей вероятности приведет к забиванию филеры армирующими волокнами или порошковыми наполнителями. В целом, настоятельно рекомендуется использовать сопла диаметром как минимум 0,4 мм. В любом случае, перед началом 3D-печати крайне желательно сверяться с рекомендациями производителя.
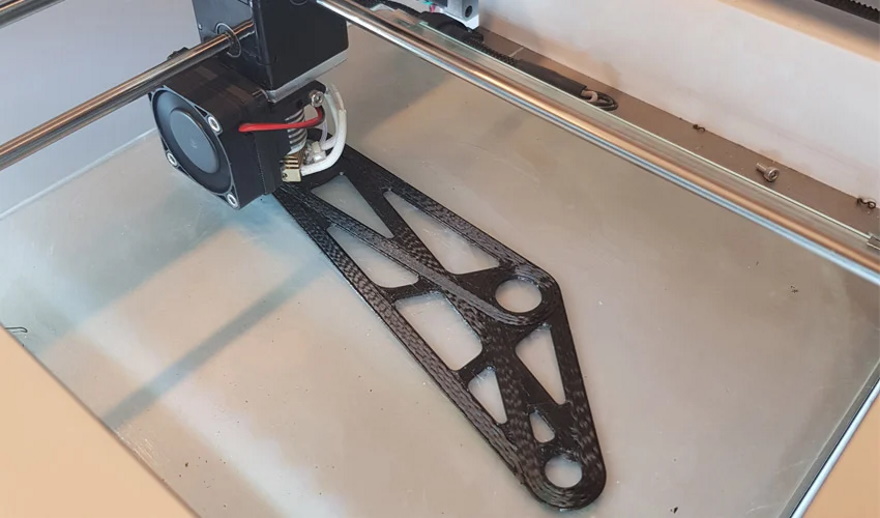
При работе со стекловолоконными композитами желательно использовать сопла диаметром как минимум 0,6 мм из-за относительно высокой длины и толщины волокон.
В случае с угленаполненными композитами минимальный диаметр зависит от типа волокон. Если производитель указывает в составе короткое рубленое волокно, возможно хватит сопла диаметром 0,4 мм. В противном случае необходимо использовать сопла диаметром не менее 0,6 мм.
Арамидные волокна также могут сильно отличаться по длине, так что во избежание пробок рекомендуется использовать сопла диаметром от 0,6 мм.
Для 3D-печати полимерами с древесными наполнителями минимальный размер — 0,6 мм, во многих случаях может потребоваться и увеличение до 0,8 мм.
При печати материалами с минеральными добавками все зависит от процентного содержания наполнителя: если доля относительно невелика, можно попробовать сопло диаметром 0,4 мм.
При 3D-печати материалами с растительными волокнами желательно отталкиваться от 0,6 мм, увеличивая или понижая диаметр опытным путем.
Люминофорные добавки не оказывают сильного влияния на плотность и текучесть, так что должно хватить сопла диаметром 0,4 мм.
Композиты с металлическими и керамическими наполнителями обычно требуют диаметра не менее 0,6 мм, особенно если речь идет про материалы с высокой долей порошка для печати полимер-металлических или полимер-керамических заготовок.
В целом, мы рекомендуем перед началом ответственных проектов печатать тестовые модели, например калибровочные кубики. Это поможет не только определить качество экструзии и адгезии, а заодно и проверить размерную точность.
5. Выбор материала сопла
Большинство композиционных филаментов отличаются повышенной абразивностью и могут «съесть» новенькое латунное сопло за считанные часы. По этой причине необходимо использовать сопла из износостойких материалов. Наиболее распространенный ввиду хорошей ценовой доступности вариант — насадки из закаленной стали. Существуют и более износостойкие, но в то же время значительно более дорогие варианты, например сопла из карбида вольфрама и даже с насадками или покрытиями из синтетических рубинов, сапфиров и алмазов.
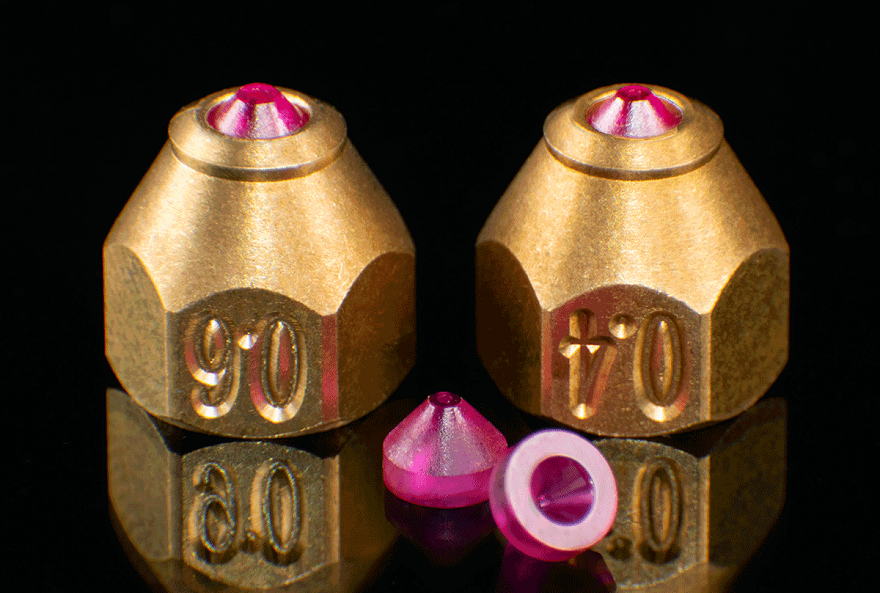
Дополнительно рекомендуем использовать специализированные экструдеры, так как при длительной 3D-печати абразивными композитами повышенному износу могут быть подвержены не только сопла, но и шестерни подающих механизмов, тефлоновые трубки, термобарьеры и другие детали в прямом контакте с расходными материалами.
6. Скорость и температура печати
Материалы с наполнителями в целом обладают более высокой вязкостью и теплостойкостью, чем чистые полимеры, поэтому при работе с композитами желательно несколько понижать скорость печати и в тоже время слегка повышать температуру экструзии.
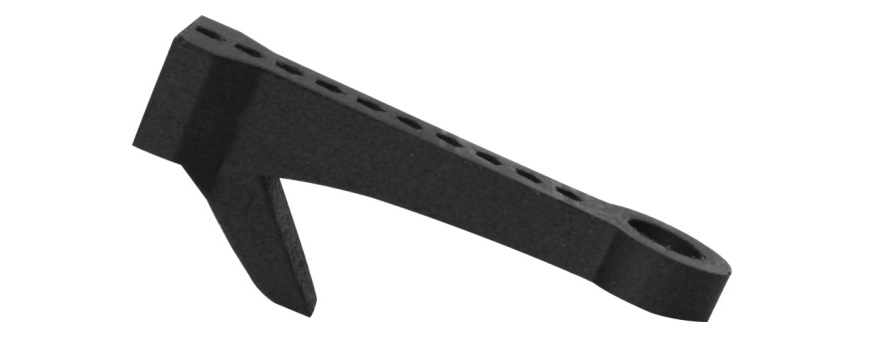
Ориентируйтесь на рекомендации производителя и старайтесь не превышать максимальные допустимые температуры, так как это может привести к повреждению материалов.
7. Адгезия со столиками
Филаменты с наполнителями обычно менее подвержены усадке при охлаждении, что делает их менее склонными к короблению. Чем выше доля волокон или частиц, тем ниже усадка, а это несомненный плюс.
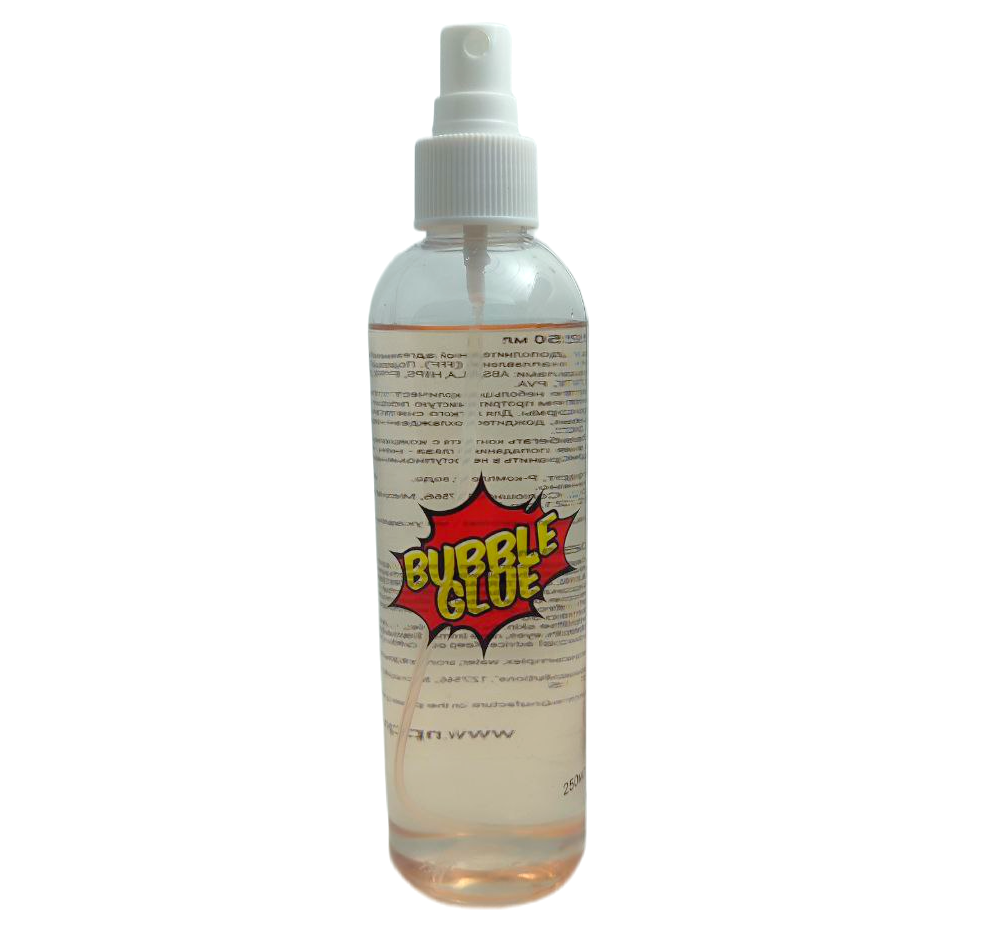
С другой стороны, наполнители нередко влияют на адгезию материала со столиками 3D-принтеров, несколько снижая схватывание. При использовании таких филаментов, особенно с высоким содержанием наполнителей, рекомендуется использовать дополнительные адгезионные средства — клеи или лаки.
8. Хрупкость филаментов
Характерная особенность большинства филаментов с наполнителями — повышенная хрупкость, особенно при высокой доле наполнителя и/или при использовании изначально хрупких полимеров в качестве основы, например того же полилактида (PLA). По этой причине важную роль играет правильное расположение катушки: путь филамента к хотэнду должен быть как можно более коротким и прямым, без сильных изгибов.
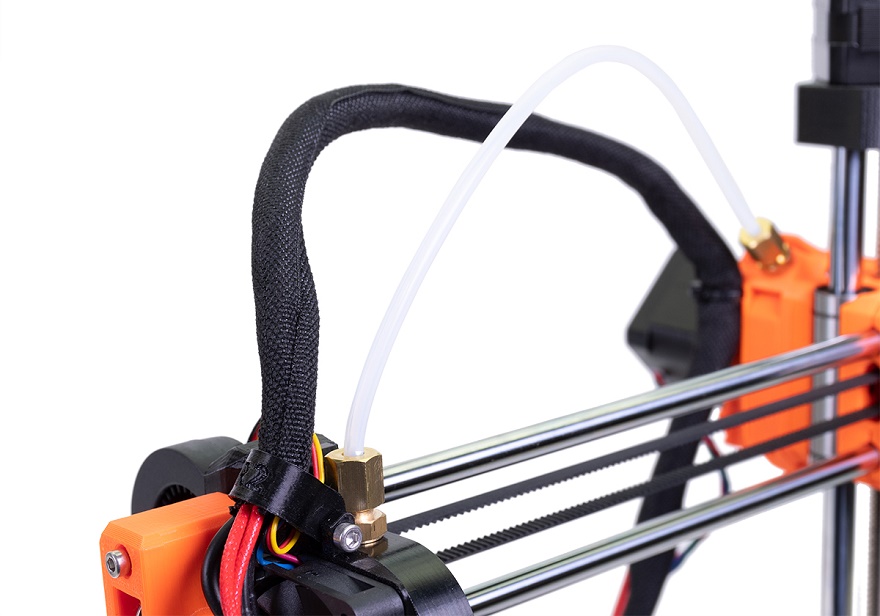
Также желательно использовать экструдеры с директ-подачей филамента (где механизм подачи и хотэнд объединены в единый узел на каретке), хотя некоторыми композитами можно печатать и на 3D-принтерах с боуденовской подачей (где механизм крепится на шасси 3D-принтера и соединяется с хотэндом длинной тефлоновой трубкой — трубкой Боудена). В последнем случае целесообразно располагать трубку Боудена таким образом, чтобы она имела максимальный возможный радиус изгиба.
Адаптированный перевод статьи 3D printing with composite materials. What to have in mind, опубликованной на сайте filament2print.
Чтобы написать отзыв нужно авторизоватся
Вход через социальные сети