Композиционные материалы с волоконными армирующими наполнителями подходят не только для 3D-печати конечных изделий. Есть и еще одно направление, быстро набирающее популярность в промышленности — аддитивное производство формовочной оснастки для изготовления угле- и стеклопластиковых деталей.
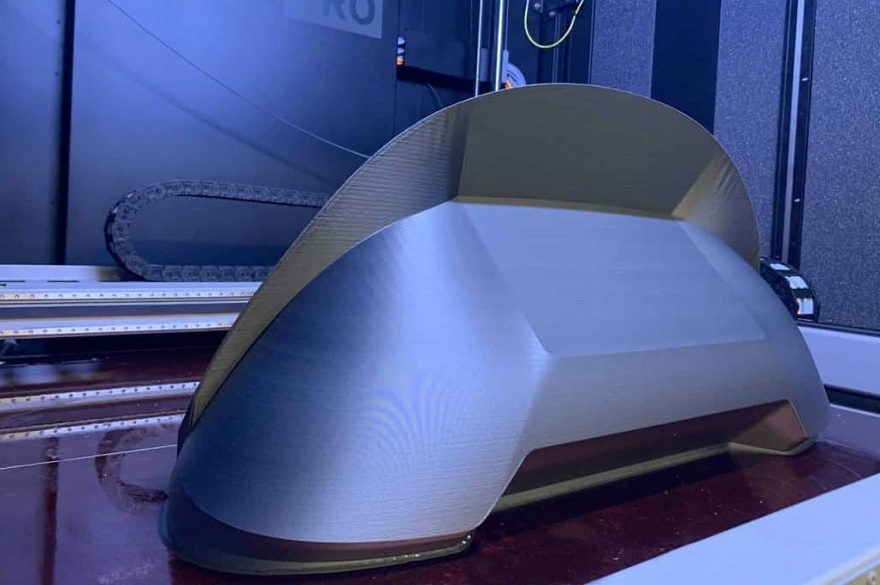
Одно из преимуществ цифрового производства — возможность изготовления форм без создания мастер-моделей, что уже устраняет один трудоемкий этап. Формы можно и фрезеровать, но зачастую это обходится дороже и занимает дольше, чем 3D-печать заготовок. Это не означает, что фрезерование теряет актуальность: при всех своих возможностях экструзионная 3D-печать композитами все же ограничена в плане качества поверхностей, а потому 3D-печатные заготовки требуют чистовой механической обработки. Тем не менее, такой комбинированный подход во многих случаях более быстр и экономичен, чем, например, фрезерование из алюминиевых болванок. К тому же, аддитивные технологии позволяют выращивать цельные детали с внутренними полостями, что невозможно реализовать традиционными методами без разделения деталей на части и последующей сборки, а это опять-таки ведет к росту финансовых и временных затрат.
Почему в аддитивном производстве такой оснастки используются композиционные материалы? Причины три — прочность и термостойкость, необходимые для автоклавирования, плюс пониженная в сравнении с чистыми полимерами усадка, что облегчает соблюдение размерной точности при 3D-печати.
Диапазон угленаполненных композитов крайне широк, так как в качестве основы можно использовать любой полимер — от акрилонитрилбутадиенстирола, как в случае с REC FormaX, до тугоплавких конструкционных термопластов вроде полиэфиримида или полиэфирэфиркетона, как в случае с REC PEEK CF. Вопрос лишь в требованиях формовочного процесса — температуре термической обработки и давлении, которое должна выдерживать форма.
Примеры применения аддитивных технологий в производстве формовочной оснастки из угленаполненных композитов
Форма для производства вертолетных лопастей
Изделие на иллюстрации ниже — семиметровая форма для производства лопастей по заказу вертолетостроительной компании Bell Textron. Форма напечатана на крупноформатном 3D-принтере по технологии экструзионной печати гранулятами (FGF, Fused Granulate Fabrication). Расходным материалом послужил акрилонитрилбутадиенстирол (АБС) с двадцатипроцентной долей рубленого углеволоконного наполнителя, в целом аналогичный нашему композиту FormaX, только в гранулированной форме ввиду больших габаритов изделия.
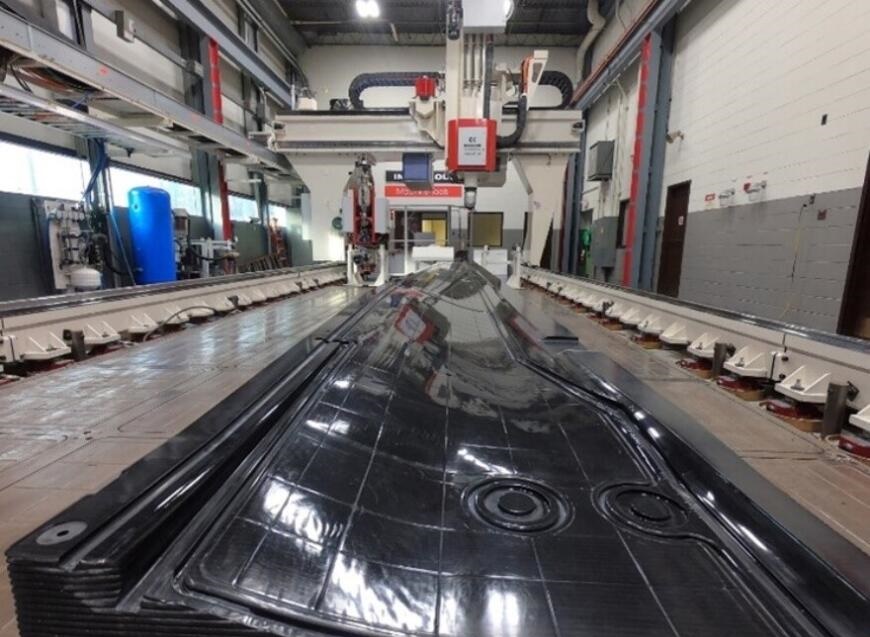
В общей сложности на 3D-печать израсходованы пятьсот двадцать килограмм композита. Заготовку вырастили целиком, одной деталью, а затем подвергли чистовой обработке на том же оборудовании, заменив экструдер на фрезерную головку. Так как это вакуумная форма, поверхности пропитали для удовлетворения требованиям по нулевой газопроницаемости.
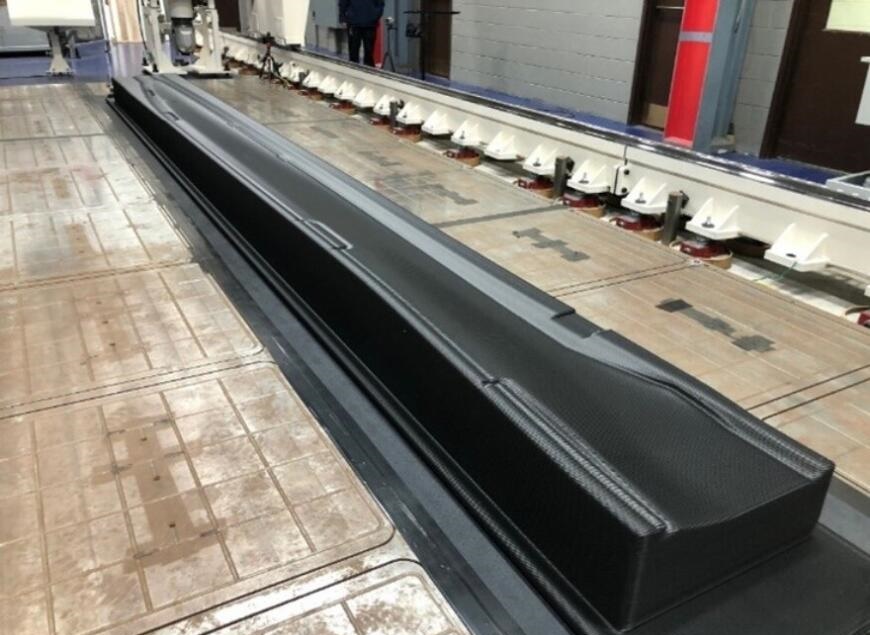
3D-печать заготовки заняла около трех суток, постобработка — еще неделю. Много это или мало? По словам авторов проекта, изготовление такой же формы, но традиционными методами и из алюминия заняло бы четыре-пять месяцев.
Автоклавная форма для Boeing
Этот пример — тоже из авиастроения, но уже с участием компании Boeing. Даже методом 3D-печати изготовление такой формы оказалось непростой задачей из-за геометрической сложности. Округлая порция детали требовала построения под углами наклона выше условного лимита в сорок пять градусов. Печатать по воздуху экструзионные 3D-принтеры не умеют, если не считать коротких «мостиков», поэтому в таких случаях есть два решения — либо выстраивать опорные структуры, либо менять пространственную ориентацию модели так, чтобы 3D-принтер мог вырастить деталь без 3D-печати поддержек. В этом случае авторы остановились на втором, менее трудоемком и расточительном варианте, развернув модель на тридцать пять градусов.
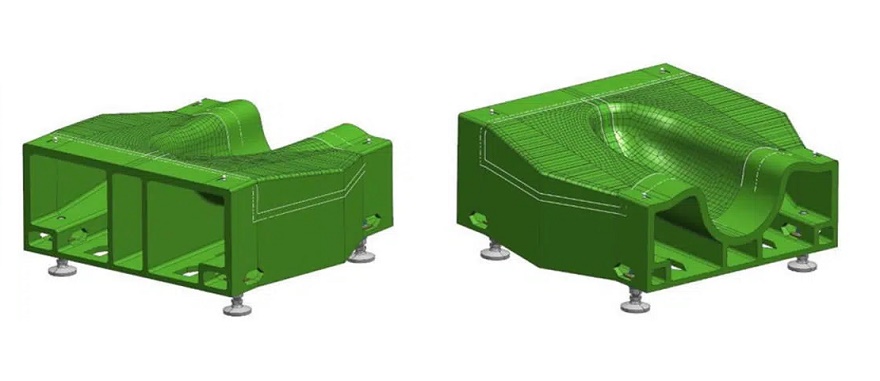
Помимо сложной геометрии были и другие требования: при автоклавировании форма должна была выдерживать температуры порядка 180°С под давлением чуть выше пяти с половиной атмосфер. В качестве расходного материала выбрали тугоплавкий конструкционный термопласт полисульфон, армированный короткими углеродным волокнами. Как и в предыдущем примере, форму напечатали на экструзионном 3D-принтере, используя композит в гранулированном виде.
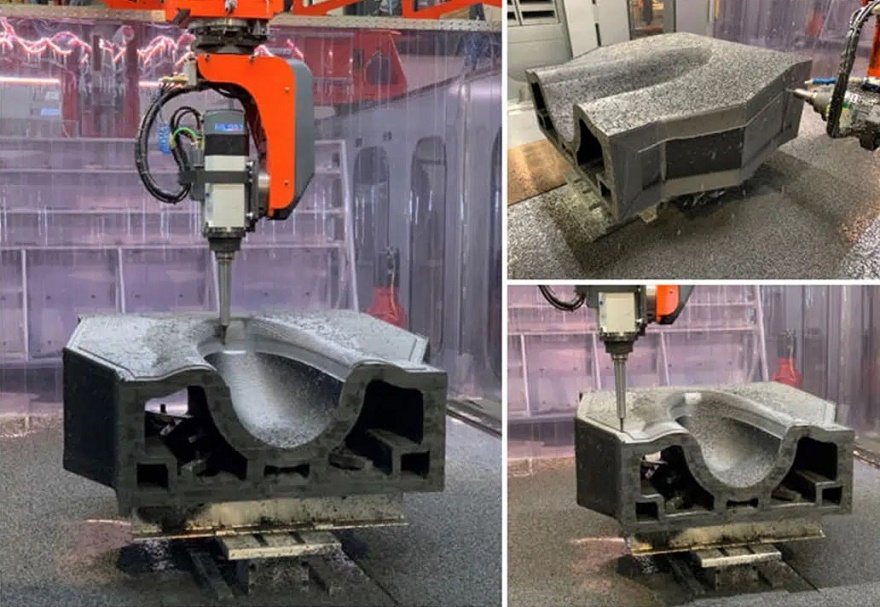
Гибридная аддитивно-субтрактивная система напечатала заготовку за семь с половиной часов, а после замены экструдера на фрезерную головку обработала заготовку до чистового вида еще за пятьдесят три часа.
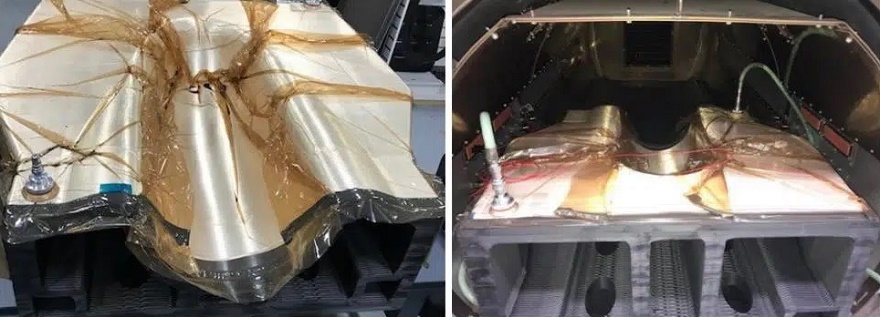
Экономия средств в этом случае оценена в пятьдесят процентов в сравнении с традиционными производственными методами, а экономия времени — в шестьдесят пять процентов. Форма успешно прошла испытания на термостойкость, прочность и газопроницаемость, а затем послужила основой для изготовления нескольких деталей из углепластика.
Формы для производства ветрогенераторных лопастей
Композитные лопасти используются не только в авиастроении, но и ветроэнергетике, и в этой отрасли предприятия тоже постоянно ищут более эффективные производственные решения. В прошлом году Министерство энергетики США выделило Университету Пердью и его промышленным партнерам грант в размере почти трех миллионов долларов на проект по оптимизации производства ветрогенераторных лопастей.
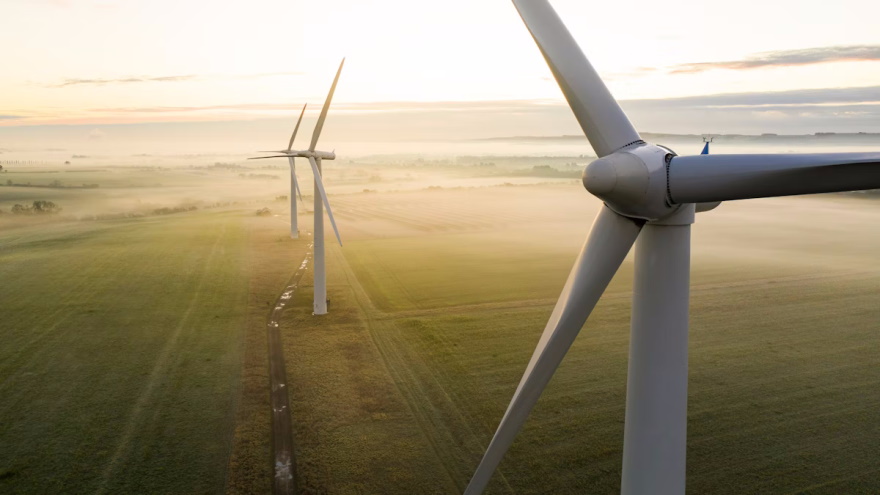
Перед участниками стоят амбициозные цели: сроки производства необходимо сократить минимум на сорок процентов, а стоимость — на тридцать пять процентов. В то же время массу оснастки необходимо снизить на четверть, а заодно повысить эффективность на пятнадцать процентов. Помимо этого, технология должна позволять изготавливать лопасти длиной не менее восьмидесяти метров.
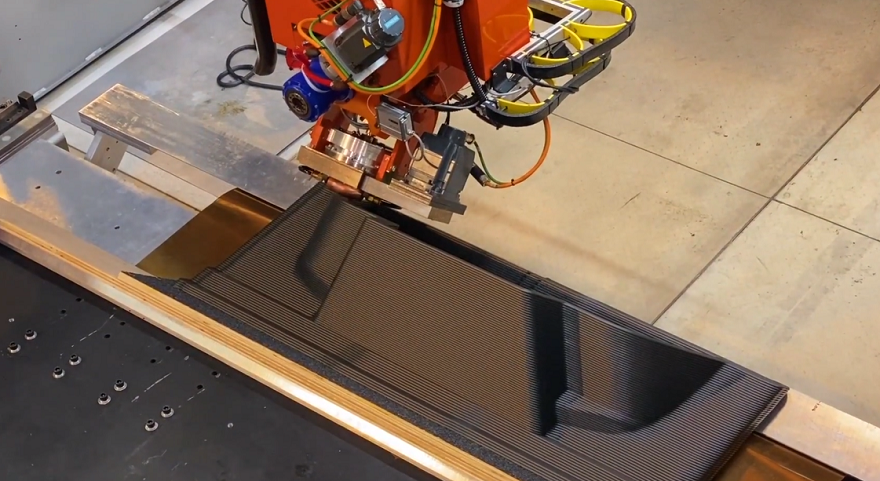
Участники проекта тоже решили положится на аддитивные технологии. Производство композитных лопастей таких размеров требует модульной оснастки сложной формы с прочными соединениями и интеграцией охлаждающих каналов. В проекте задействовано аддитивное оборудование компании Thermwood — крупноформатные гибридные системы LSAM, печатающие гранулированными угленаполненными композитами и выполняющие чистовую обработку с помощью пятиосевых фрезерных насадок. Такие системы способны выращивать заготовки длиной до двенадцати и шириной до четырех с половиной метров с возможностью дальнейшего масштабирования, если возникнет необходимость. Производительность экструзионных систем достигает двухсот двадцати пяти килограмм в час, при этом изделия можно выращивать как вертикально, так и горизонтально.
Оснастка для формования углепластиковых картерных крышек
Еще одна отрасль, где широко используются углепластики — автомобилестроение. Следующий пример реализован компанией Caracol. На иллюстрации ниже показана 3D-печатная оснастка для формования углепластиковой крышки картера гиперкара (слева) и готовая крышка (справа).
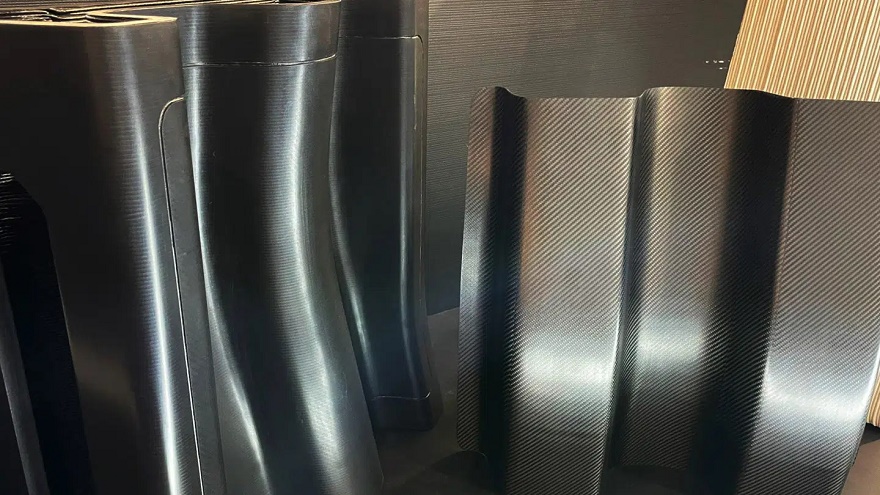
Формовочная оснастка напечатана угленаполненным композитом на основе поликарбоната. Как видно на иллюстрации ниже, непосредственно после выращивания заготовка имела характерные ребристые поверхности, потребовавшие чистовой обработки фрезером. Аддитивные системы от Caracol строятся на основе многоосевых роботов-манипуляторов, так что переход от 3D-печати к фрезерованию — вопрос замены рабочей насадки.
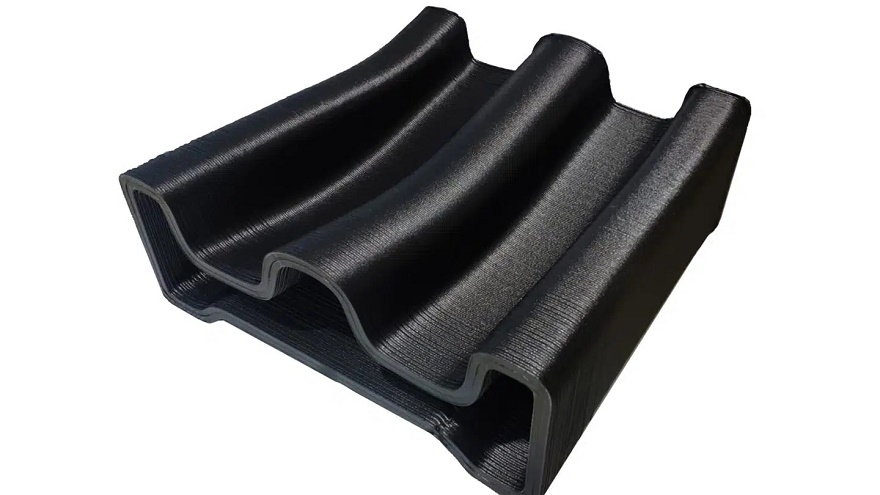
Полученная форма выдерживает температуры до 180°С под давлением до шести атмосфер, то есть соответствует требованиям автоклавирования. Масса заготовки длиной и высотой в полметра с шириной около двухсот миллиметров составила двадцать один килограмм. При изготовлении формы традиционными, субтрактивными методами масса заготовки и объем отходов оцениваются на шестьдесят и семьдесят процентов выше соответственно. Экономия времени достигла семидесяти пяти процентов с сокращением сроков с восьми до двух недель, а стоимость удалось снизить вдвое.
3D-печать форм и производство углепластиковых деталей в мастерских
Если речь не идет про производство крупногабаритных изделий, процесс 3D-печати форм и получения готовых углепластиковых деталей вполне реализуем в небольших мастерских.
Для выполнения подобных проектов само собой потребуются препрег и эпоксидная смола, а форму можно напечатать на настольном 3D-принтере, оборудованном износостойким соплом и, крайне желательно, закрытой камерой для стабилизации фоновой температуры, например системе линейки Picaso Designer X Series 2. В качестве расходных материалов можно использовать угленаполненный акрилонитрилбутадиенстирол REC FormaX или стеклонаполненный полиэтилентерефталатгликоль rPETG GF. Без вакуумной обработки можно обойтись даже чистыми полимерами — REC ABS или REC Relax.
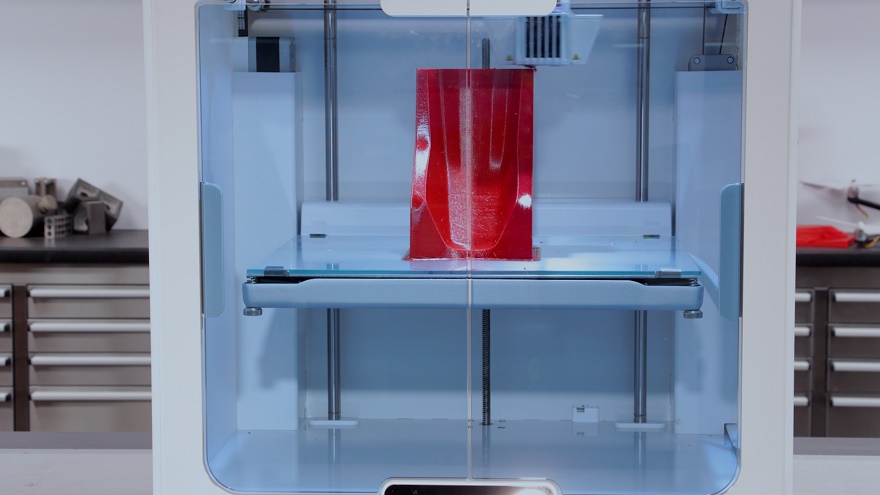
На первом этапе проектируется и печатается форма из выбранного материала. Перед укладкой препрега на форму необходимо нанести разделительный слой, иначе после отвержения эпоксидной смолы деталь будет практически невозможно отделить от формы. В качестве разделительного слоя можно использовать раствор поливинилового спирта. Это водорастворимый полимер, родственный поливинилацетату в клее «ПВА» и часто используемый для построения опорных структур при 3D-печати сложных деталей.
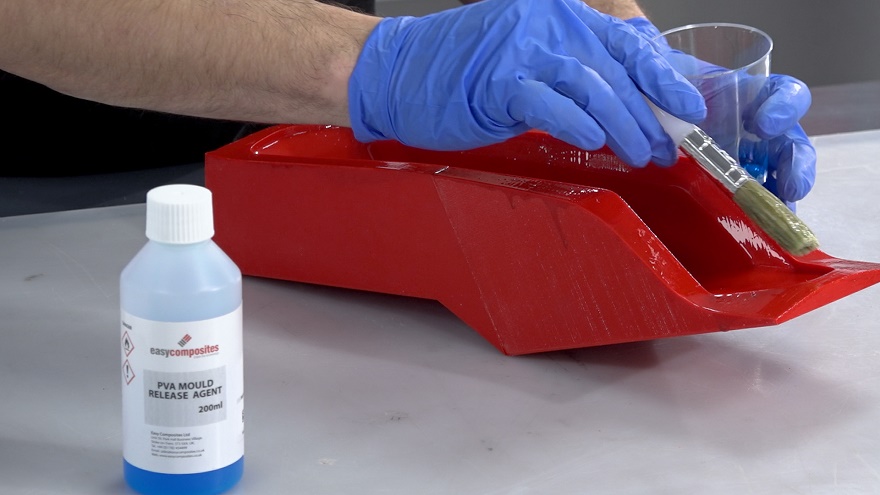
Просушивание разделительного слоя при комнатной температуре займет около получаса, после этого можно приступать к укладке препрега. Углепластики — это ламинаты, то есть изделия, состоящие из слоев углеродной ткани (карбона), обильно смазанных связующим — в нашем случае эпоксидной смолой. Первым делом на форму с нанесенным и высушенным разделительным слоем наносится слой эпоксидной смолы, затем поверх нее укладывается лоскут углеткани, затем наносится следующий слой смолы. Пропорции смолы и ткани по весу должны быть примерно равными.
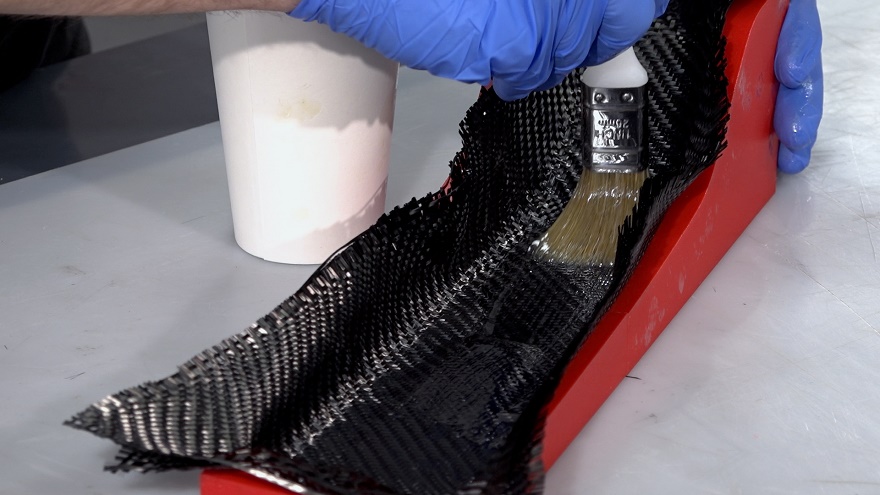
Если речь идет про изготовление тонкостенных изделий толщиной не более трех миллиметров, весь процесс можно выполнить за один прием. Если толщина превышает три миллиметра, необходимо брать во вниманию усадку: в таких случаях ламинировать лучше поэтапно, позволяя смоле схватываться и усаживать перед нанесением следующей партии слоев. Это поможет избежать сильных остаточных напряжений и деформаций.
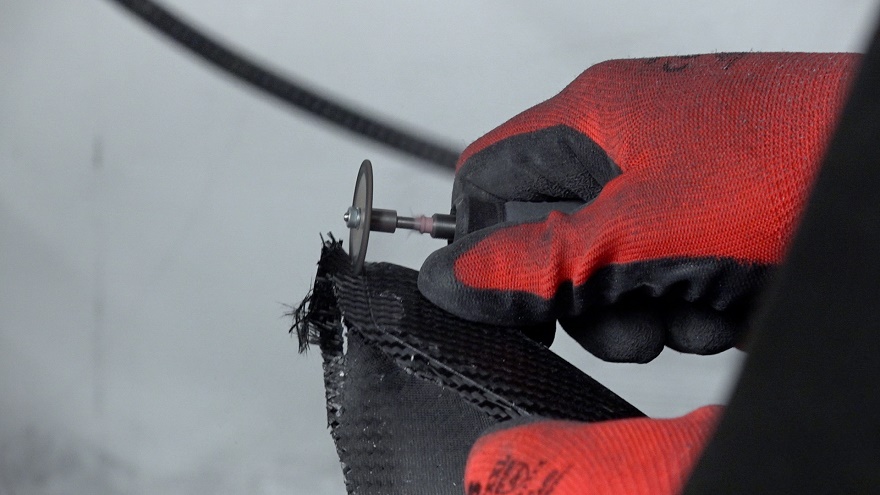
Время полного отверждения деталей будет варьироваться в зависимости от процентной доли отвердителя в смоле и окружающей температуры, но обычно процесс занимает от двенадцати часов до двух суток. После отверждения смолы и отделения заготовки от формы лишний материал по краям обрезается, как правило с помощью электроинструмента. Чистовую обработку можно выполнить наждачной бумагой.
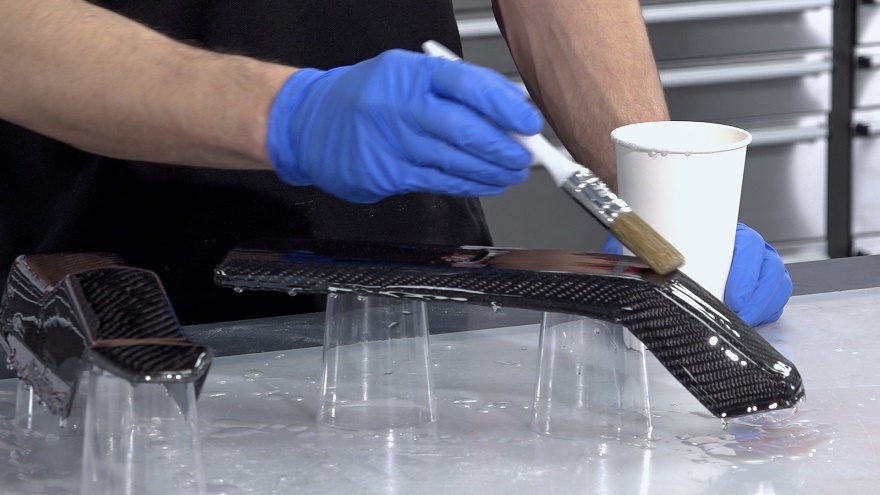
После механической обработки на деталь можно нанести слой прозрачной смолы для повышения эстетики: дополнительный слой не только даст приятную глянцевую поверхность, но и позволит скрыть мелкие дефекты. В таких случаях поверхность заготовки необходимо предварительно обработать крупнозернистой наждачной бумагой для повышения адгезии. Расход смолы на каждый слой составит примерно триста грамм на квадратный метр, отвердитель и основу перед нанесением кистью необходимо смешать в пропорции 10:3,5. В большинстве случаев хватает одного слоя, но при необходимости можно нанести второй, как только первый слегка схватится.
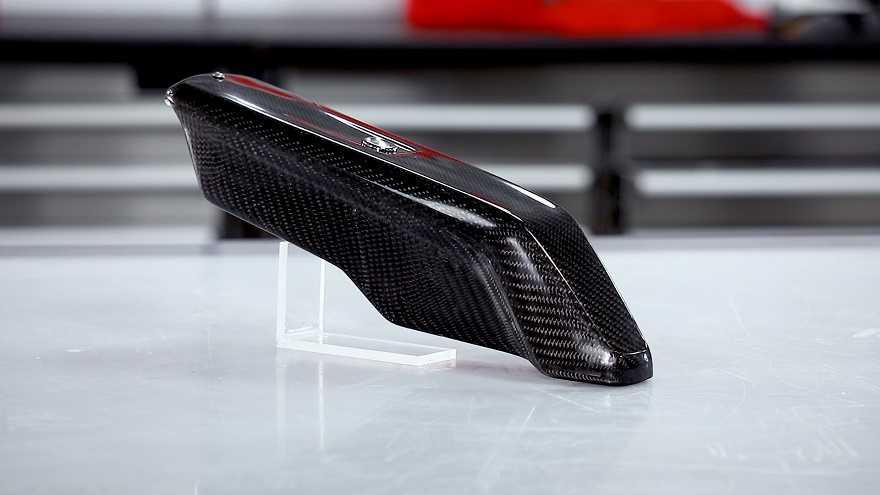
Заключительный этап — повторная обработка наждачной бумагой с постепенным переходом от крупной зернистости к мелкой. Шлифовать лучше сначала смоченной в воде бумагой, а затем сухой той же зернистости. После шлифования деталь следует отполировать, используя специальный лак.
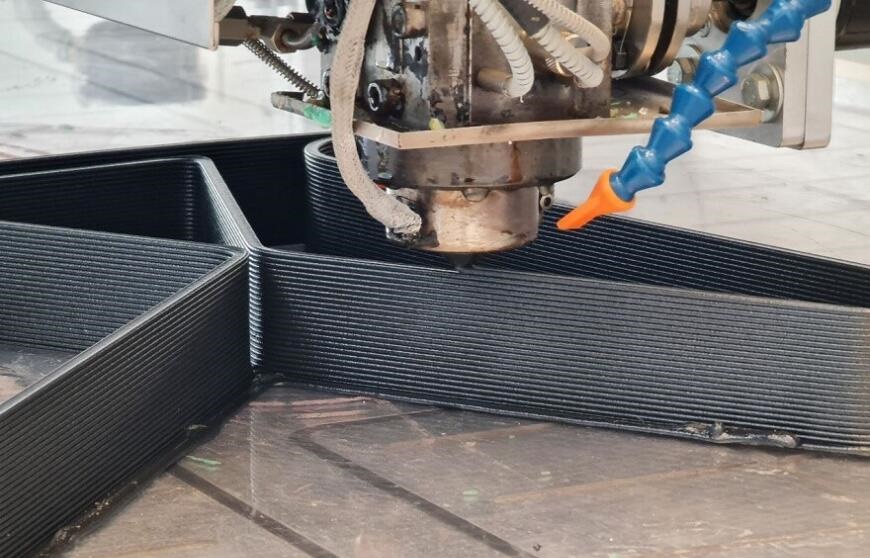
Различные композиционные материалы со стекло- и углеволоконными наполнителями представлены в наших линейках X-line, Clotho и Technika. В нашем распоряжении также крупноформатный 3D-принтер Colossus, способный выращивать изделия длиной более двух с половиной метров.
Если у вас остались вопросы, свяжитесь с нами и получите подробную консультацию.
Чтобы написать отзыв нужно авторизоватся
Вход через социальные сети