Полиамиды, зачастую называемые нейлонами — одни из самых распространенных инженерных термопластов, и на то есть ряд объективных причин: они прочны, долговечны, выдерживают довольно высокие эксплуатационные температуры. Некоторые разновидности полиамидов используются в 3D-печати. О них и поговорим в этой статье.
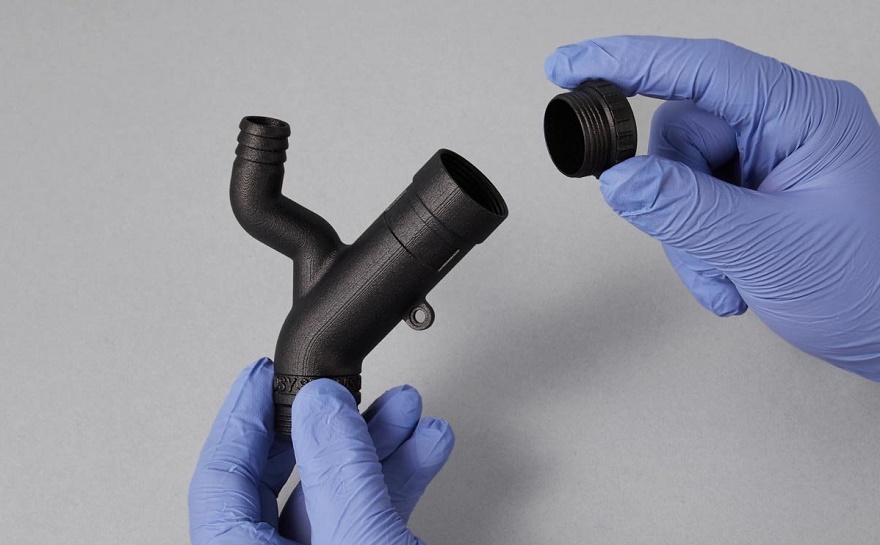
Для начала давайте разберемся с «полиамидами» и «нейлонами». Все нейлоны — полиамиды, но не все полиамиды — нейлоны. Название «нейлон» — изначально торговая марка американской компании DuPont, относившаяся конкретно к нейлону-6,6, он же нейлон-66, он же полиамид-6,6 или полиамид-66. В аддитивных технологиях нейлон-66 используется довольно редко, да и то в основном в виде сополимера полиамида-6 и полиамида-66, но слово «нейлон» вошло в обиход и стало нарицательным для разных видов полиамидов.
Что означают цифры? Это количество атомов углерода в так называемых «блоках». Например, каждый блок полиамида-6 содержит один мономер с шестью атомами углерода, а блок полиамида-6,6 содержит два мономера — гексаметилендиамин и адипиновую кислоту — с шестью атомами углерода в каждом.

В 3D-печати наиболее часто используются три вида полиамидов — полиамид-6, полиамид-11 и полиамид-12. Помимо этого популярность набирают композиционные материалы на основе полиамидов, армированные стекло- или углеволокном, а иногда усиливаемые базальтовыми или параарамидными (кевларовыми) волокнами. Кевлар, кстати — тоже торговая марка компании DuPont и тоже обиходное, хоть и не всегда корректное название.
Полиамиды в целом славятся высокой прочностью, широким диапазоном эксплуатационных температур, низким коэффициентом трения, хорошей химической стойкостью, и в то же время страдают от одинаковых недостатков — высокого влагопоглощения (гигроскопичности) и уязвимости к ультрафиолету. Фактически, разные виды полиамидов затачиваются под разные задачи — где-то уделяется больше внимания повышению прочности или размерной стабильности, где-то — снижению гигроскопичности или стоимости.
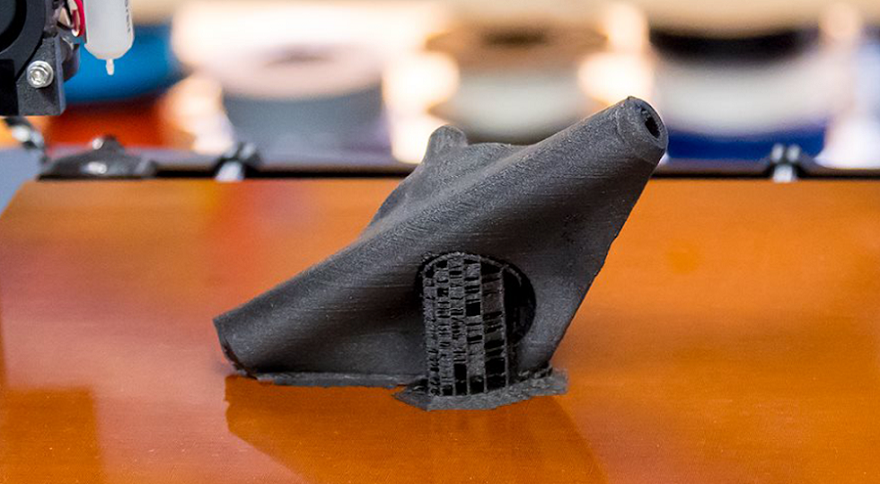
Полиамид-6 и полиамид-6,6
Полиамид-6 — самый недорогой вариант, но при этом обладающей наиболее высокими прочностными характеристиками наряду с хорошей термостойкостью и ударной вязкостью. Главный недостаток этой разновидности — высокая гигроскопичность, то есть склонность к впитыванию влаги. По этому показателю полиамид-6 — рекордсмен в нашем списке, причем в плохом смысле.
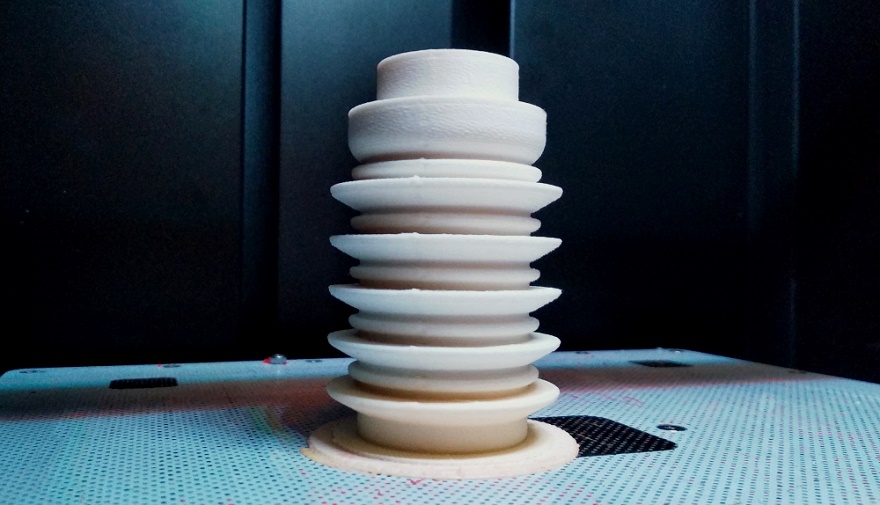
Полиамиды в целом весьма гигроскопичны, а набор влаги снижает размерную стабильность деталей, изменяет механические и электрические свойства, да к тому же может приводить к разнообразным дефектам непосредственно во время 3D-печати, поэтому любые полиамидные филаменты, а не только полиамид-6, необходимо просушивать непосредственно перед загрузкой в 3D-принтер. Подробно о хранении и просушивании филаментов из разных материалов рассказывается в отдельных статьях — здесь и здесь.
Полиамид-6,6 близок по характеристикам к полиамиду-6, но при этом обладает более низкой ударной прочностью, особенно во влажной среде, и стойкостью к ультрафиолетовой деструкции. С другой стороны, у него прекрасная износостойкость и сопротивление горюче-смазочным материалам, так что именно эта разновидность нашла самое широкое применение в промышленности, в немалой степени за счет высокого спроса в автомобилестроении. В 3D-печати полиамид-6,6 не так популярен, как полиамид-6, но все же встречается, обычно в виде комбинации полиамида-6,6 и полиамида-6.
Полиамид-11
Полиамид-11 — самый эластичный вариант. Если полиамид-6 и полиамид-6,6 используются в основном в экструзионной (FDM) 3D-печати, то полиамид-11 наиболее популярен в аддитивном производстве по технологии селективного лазерного спекания (SLS). Здесь расходными материалами служат мелкодисперсные порошки, послойно спекаемые лазерными излучателями. Ввиду высокой пластичности, ударной вязкости и сопротивления механической усталости полиамид-11 отлично подходит для изготовления гибких деталей — соединений, защелок, прокладок и тому подобного.
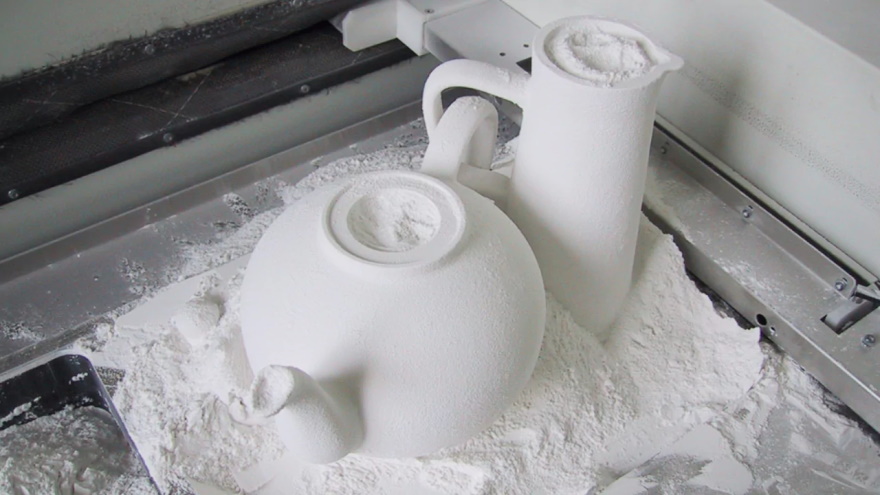
Полиамид-11 демонстрирует хорошую химическую стойкость, а также низкую плотность, что может быть выгодно при изготовлении деталей с пониженной массой, например авиационных. Помимо этого у полиамида-11 относительно низкая гигроскопичность, что тоже играет на руку, особенно при работе с порошками и при эксплуатации на открытом воздухе.
Интересная особенность полиамида-11 — происхождение: в отличие от полиамида-6 и полиамида-12 эта разновидность изготавливается из биосырья, обычно из касторового масла.
В нашем магазине этого материала нет, по крайней мере пока: REC все-таки расшифровывается как «Русская экструзионная компания», так что здесь мы предлагаем филаменты, но порошки из полиамида-11 можно приобрести у нашего партнерского предприятия 3D Solutions.
Полиамид-12
Полиамид-12 обладает самой высокой химической стойкостью, более высокой твердостью и хрупкостью, чем полиамид-6, плюс повышенной термостойкостью и самыми низкими показателями гигроскопичности — примерно на уровне полиамида-11 или даже чуть лучше. Этот вариант также выделяется наиболее высокой размерной стабильностью, что важно при изготовлении механических компонентов, в том числе стыкующихся деталей.
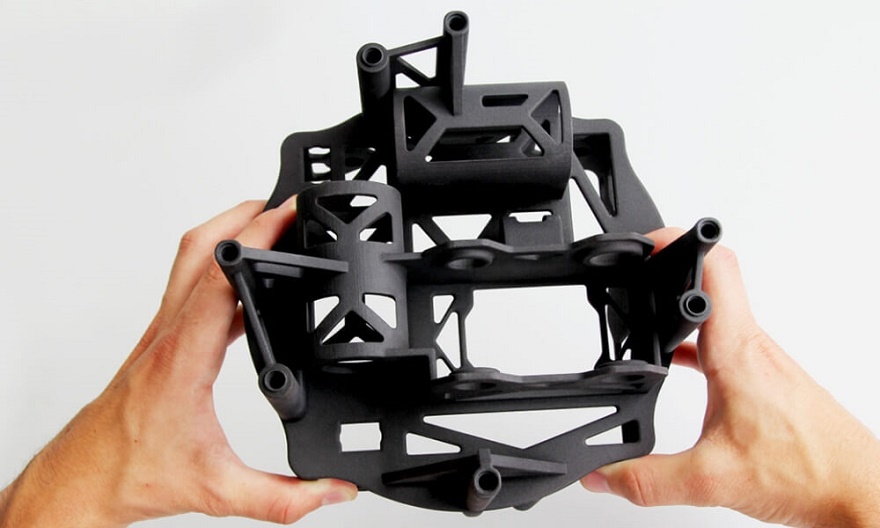
В целом, полиамид-12 — самый сбалансированный вариант, более дружелюбный в производственном плане и применяемый как в экструзионной (FDM), так и лазерной порошковой 3D-печати (SLS), но при этом один из самых дорогих — примерно в два раза дороже полиамида-6.
Для более наглядного и простого сравнения взгляните на табличку ниже.

Полиамиды и композиты под брендом REC
Мы предлагаем два варианта полиамидов и три композиционных материала на основе нейлонов, при этом мы всегда открыты к пожеланиям пользователей и даже выпускаем специфические материалы на заказ.
REC PA6
Классический инженерный полимер, также называемый капролоном, по-крайней мере в советской и российской номенклатуре. Обладает низким коэффициентом трения, высокой прочностью и сопротивлением пластическим (необратимым) деформациям, стойкостью к углеводородам, маслам, спиртам и разбавленным кислотам.
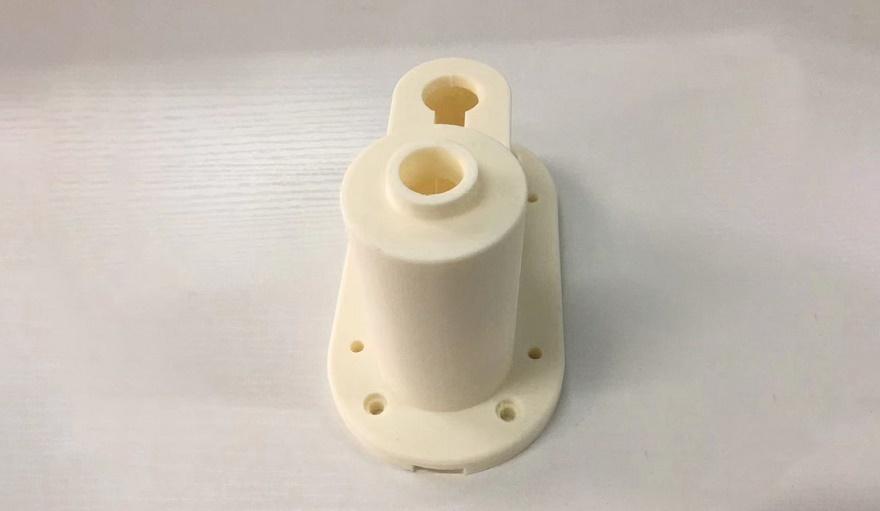
REC PA6 очень гигроскопичен и уязвим к ультрафиолетовому излучению, но хорошо подходит для изготовления теплостойких, нагруженных механических деталей и компонентов медицинского оборудования, требующих горячей стерилизации. Диапазон эксплуатационных температур — примерно -40-80°C с возможностью кратковременного нагрева до 150°C.
При 3D-печати рекомендуется прогрев хотэнда до 250-270°C, прогрев столика до 100-110°C, плюс адгезионное средство, например клей Adhesivix.
REC PA6 предлагается в виде филамента диаметром 1,75 на катушках массой 500 грамм нетто и доступен в двух оттенках — натуральном и черном.
REC PA12
Вариант с повышенной химической стойкостью к горюче-смазочным материалам, гидравлическим жидкостям, различным растворителям. По прочностным характеристикам несколько уступает полиамиду-6, но благодаря низкому коэффициенту трения, высокой теплостойкости, износостойкости и размерной стабильности все равно хорошо подходит для 3D-печати функциональных деталей — креплений, направляющих, защитных корпусов, роликов и шестерней, и тому подобного. Диапазон продолжительных эксплуатационных температур — примерно -40-80°C.
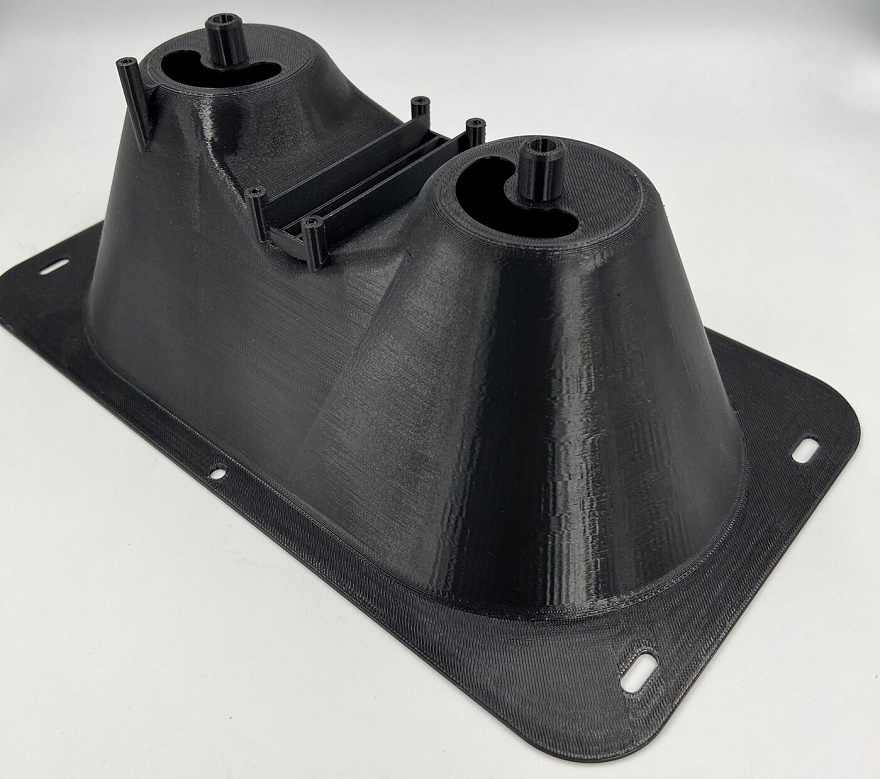
При 3D-печати рекомендуется прогрев хотэнда до 275-290°C, прогрев столика до 100-110°C, плюс адгезионное средство.
REC PA12 предлагается в виде филамента диаметром 1,75 на катушках массой 500 г или 2 кг нетто и доступен в двух оттенках — натуральном и черном.
REC Friction
Отличную износостойкость и прочность полиамидов можно дополнительно улучшить добавками. REC Friction — один их таких композиционных, стеклонаполненных материалов на основе полиамида-12, отлично подходящих для 3D-печати защитных кожухов, нагруженных механических деталей и других функциональных изделий.
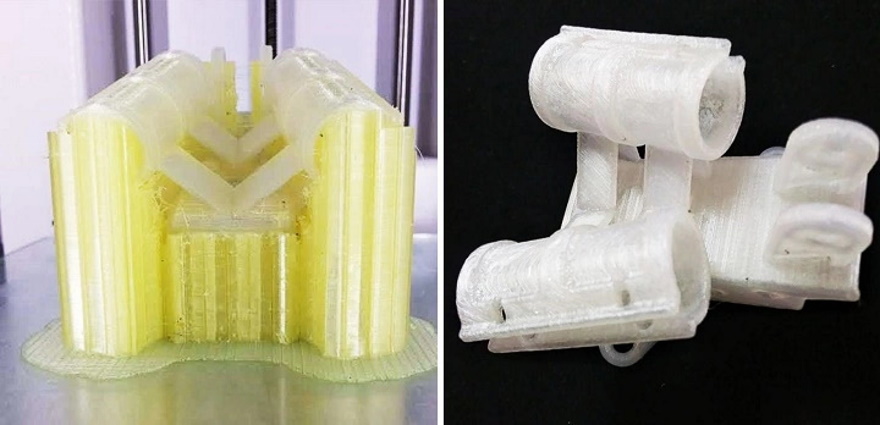
Композит сохраняет прекрасные химические свойства чистого полимера: REC Friction устойчив к воздействию минеральных масел и бензина, спиртов и щелочей, но растворяется в серной кислоте, феноле, крезоле, хлорале и трифторэтаноле. Этот материал подходит для эксплуатации при температурах от -60°С до +90°С.
Вместе с достоинствами полиамида-12 REC Friction унаследовал и слабости, а именно гигроскопичность, хоть и менее высокую, чем у полиамида-6, а также уязвимость к ультрафиолетовому излучению. REC Friction наиболее хорошо подходит для 3D-печати компонентов внутренних механизмов, скрытых от прямого солнечного света.
При 3D-печати хотэнд рекомендуется прогревать до 250-270°C, а столик — до 90-110°С. Крайне рекомендуется использовать дополнительные адгезионные средства. Еще один важный момент — повышенная абразивность, требующая использования износостойких сопел, например из закаленной стали.
REC Friction предлагается в виде филаментов диаметром 1,75 на катушках массой 500 грамм нетто и доступен в натуральном оттенке, без красителей.
Printamid 1284
Еще один композит на основе полиамида-12, но на этот раз с углеволоконным наполнителем, дополнительно повышающим жесткость и снижающим риск коробления из-за усадки, что особенно сподручно при 3D-печати крупногабаритных изделий. Собственно, этот материал изначально и разрабатывался с оглядкой на крупноформатные 3D-принтеры промышленного класса. Химическая стойкость тоже остается на высоте.
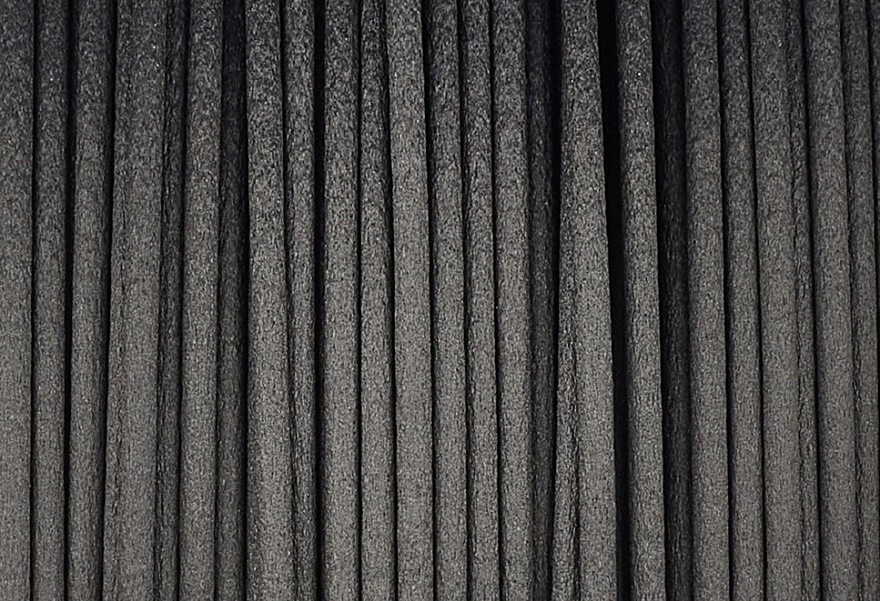
Композит Printamid 1284 отлично подходит для 3D-печати нагруженных деталей — шестерней, формовочной оснастки, элементов несущей конструкции беспилотных летательных аппаратов, и так далее.
Углеволоконные добавки повышают не только жесткость, но и термостойкость материала, а потому для 3D-печати потребуются достаточно мощные хотэнды с температурой порядка 310°С. Те же добавки снижают усадку, но во избежание отлипания моделей столики необходимо прогревать до 100-115°С и покрывать рабочие поверхности клеями. Также не стоит забывать об абразивности углеволокна: при 3D-печати армированными композитами необходимо использовать износостойкие сопла.
Композит Printamid 1284 предлагается в виде черного филамента диаметром 1,75 на катушках массой 750 грамм нетто.
REC UltraX
И наконец, композит на основе полиамида-6, тоже усиленный углеродными волокнами. Этот материал — один из самых прочных в нашем ассортименте и предназначен в первую очередь для 3D-печати нагруженных деталей. Доля углеволокна достигает тридцати процентов, обеспечивая как высокую прочность, так и жесткость, а также повышенную тугоплавкость. Диапазон эксплуатационных температур композита UltraX очень широк — от -60°C до 150°C с возможностью кратковременного нагревания до 200°C.
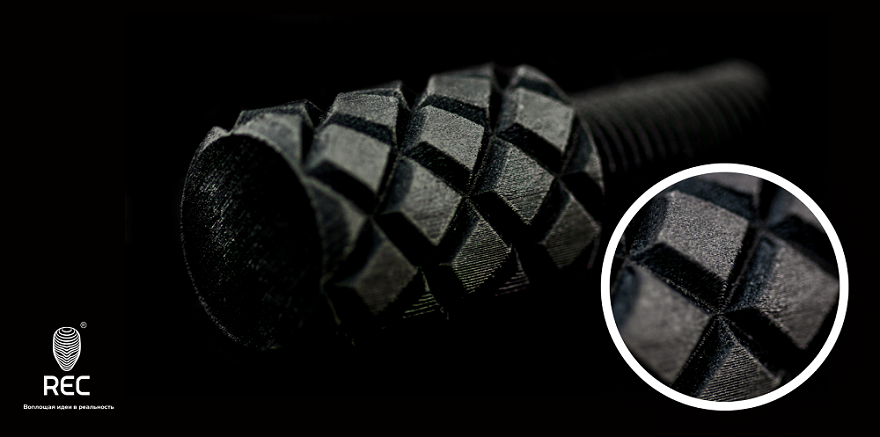
Для оптимальных результатов при 3D-печати требуется нагрев хотэнда до 300-310°C, столика — до 120-135°C и покрытие столика адгезионным средством. Также настоятельно рекомендуется использовать 3D-принтеры с термостатированными камерами, прогреваемыми до 60-90°С, например аддитивные системы линейки Designer X Series 2 производства компании PICASO 3D. Это поможет добиться высокой размерной точности изделий. Конечно, для работы с этим композитом тоже требуются износостойкие сопла из закаленной стали.
Угленаполненный полиамид-6 REC UltraX предлагается в виде филамента диаметром 1,75 мм на стандартных катушках массой 750 грамм нетто и больших катушках массой 2 кг для крупноформатной 3D-печати.
Остались вопросы? Свяжитесь с нами, и специалисты REC будут рады предоставить подробную консультацию по выбору расходных материалов под конкретные производственные задачи.
Чтобы написать отзыв нужно авторизоватся
Вход через социальные сети