Сегодня взглянем на весьма успешное направление в развитии экструзионной 3D-печати — построение изделий с комбинированием разных материалов для достижения градиентных свойств, улучшения эстетичности и упрощения постобработки.
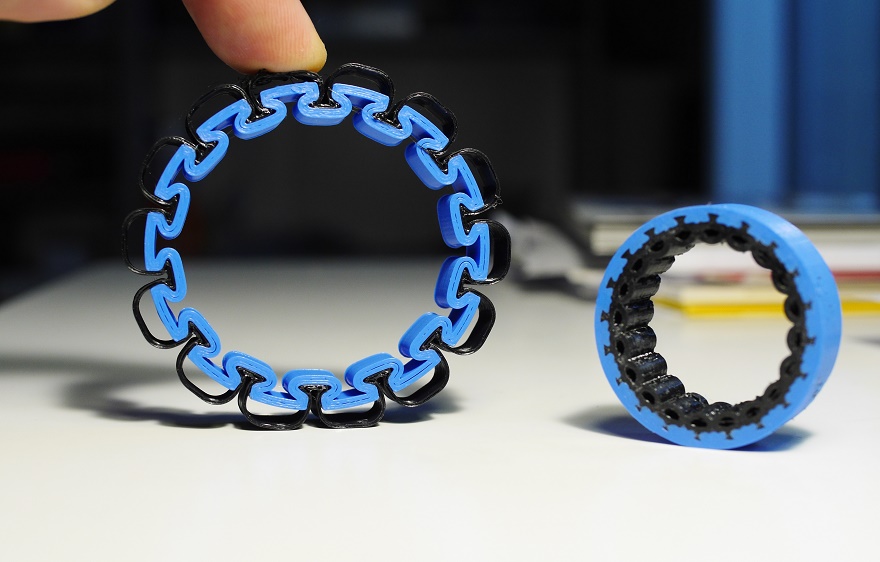
Как подсказывает название, мультиматериальная 3D-печать — это печать несколькими материалами в пределах одного рабочего цикла. Сюда может входить как печать разными цветами, так и материалами с разным химическим составом, или даже построение разными цветами и составами одновременно. Соответственно, мультиматериальная 3D-печать может быть направлена либо на создание многоцветных изделий, либо получение разных физико-механических и/или химических свойств на разных участках моделей, например электропроводности, сочетания эластичности и жесткости, выборочной прозрачности, и так далее.
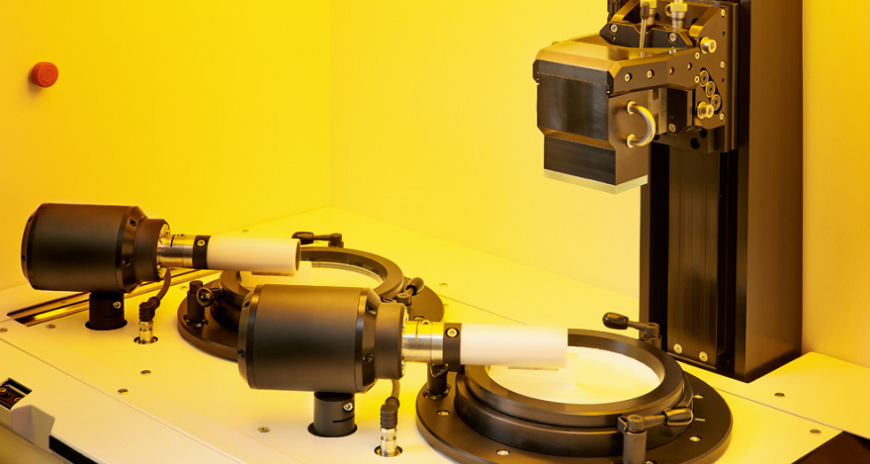
Двухматериальная стереолитографическая система CeraFab Multi 2M30 компании Lithoz
Концепция мультиматериальной 3D-печати реализована с той или иной степенью успеха в разных аддитивных технологиях, а также с разной доступностью. Например, при работе с фотополимерами приходится полагаться либо на стереолитографию, либо на струйную печать. В первом случае можно печатать разными материалами, используя две или несколько емкостей с разными жидкими смолами и перемещением модели туда и обратно в процессе построения. Такое решение придумала австрийская компания Lithoz, выпускающая оборудование для 3D-печати высоковязкими фотополимерными смолами.
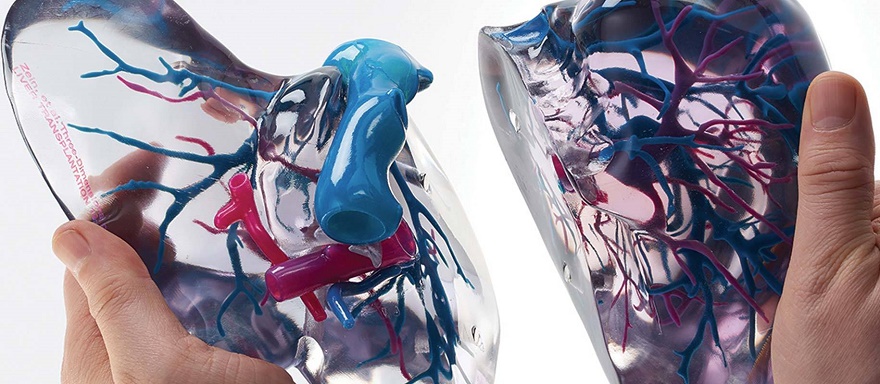
Примеры 3D-печати на струйном фотополимерном 3D-принтере Stratasys J750
Струйные аддитивные системы используют пьезоэлектрические головки для выборочного напыления смол с последующей засветкой и отверждением. Подобное оборудование выпускают, например, американская корпорация Stratasys и японская компания Mimaki. Этот вариант позволяет добиваться огромного разнообразия оттенков, а заодно дает возможность работы с несколькими материалами одновременно, но стоит такое оборудование очень дорого. Мы же расскажем подробнее про варианты с использованием экструзионной 3D-печати филаментами (FDM/FFF), доступной любителям и малому бизнесу.
Экструзионная 3D-печать дает богатый выбор опций ввиду развитости рынка расходных материалов. Один из самых распространенных примеров одновременного применения нескольких материалов — 3D-печать моделей сложной формы с растворимыми поддержками. Например, изделие можно вырастить из полилактида (PLA) с опорами из водорастворимого поливинилового спирта (PVA), либо из акрилонитрилбутадиенстирола (ABS) с опорами из растворимого в D-лимонене ударопрочного полистирола (HIPS).
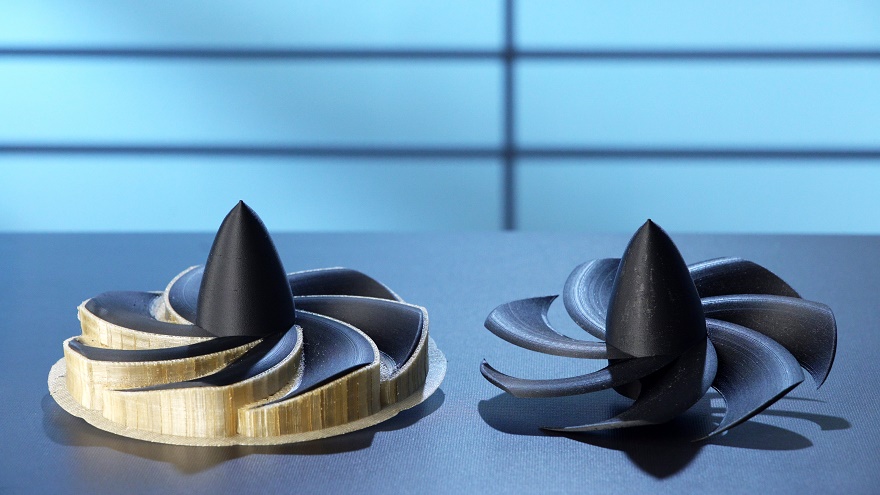
3D-печатная модель до и после удаления водорастворимых опорных структур
Это значительно снижает трудозатраты на постобработку, а заодно помогает повышать качество поверхностей. В некоторых случаях, когда приходится иметь дело с деталями особо сложной формы, без растворимых поддержек можно обойтись только делением 3D-моделей на более простые части, что в итоге требует сборки и может снижать прочность конечных изделий. Аналогичным образом мультиматериальная 3D-печать позволяет обходиться без склеивания изделий из нескольких материалов, снижая затраты и, опять-таки, повышая прочность.
Любая 3D-печать начинается с дизайна. Большинство современных систем автоматизированного проектирования (CAD) позволяют маркировать детали, добавляя информацию о материалах или приписывая конкретные материалы к конкретным участкам моделей, что помогает с настройкой параметров 3D-печати. Непосредственно в процессе построения необходимо помнить о том, что разные материалы требуют разных настроек, например температуры экструзии. Соответствующие инструкции должны присутствовать в машинном коде (G-коде), что осуществляется либо посредством подходящего слайсера, либо вручную. Немаловажен и выбор оборудования, так как процесс будет отличаться при использовании одноэкструдерных и многоэкструдерных 3D-принтеров, а также систем автоматической смены филамента.
Мультиматериальная 3D-печать на одноэкструдерных системах
3D-печать несколькими материалами вполне можно реализовать даже на самых простых и дешевых 3D-принтерах, оснащенных одним экструдером. Самый простой вариант — ручная замена филамента в процессе 3D-печати. На самом деле это частично автоматизированный процесс, так как в машинный код необходимо заранее внести команды на приостановку 3D-печати в требуемые моменты: когда подходит время, 3D-принтер встает на паузу, затем оператор меняет филамент и отдает команду на продолжение построения. Процесс довольно трудозатратный, так как в зависимости от размера и сложности модели могут потребоваться десятки или даже сотни операций по смене филамента.
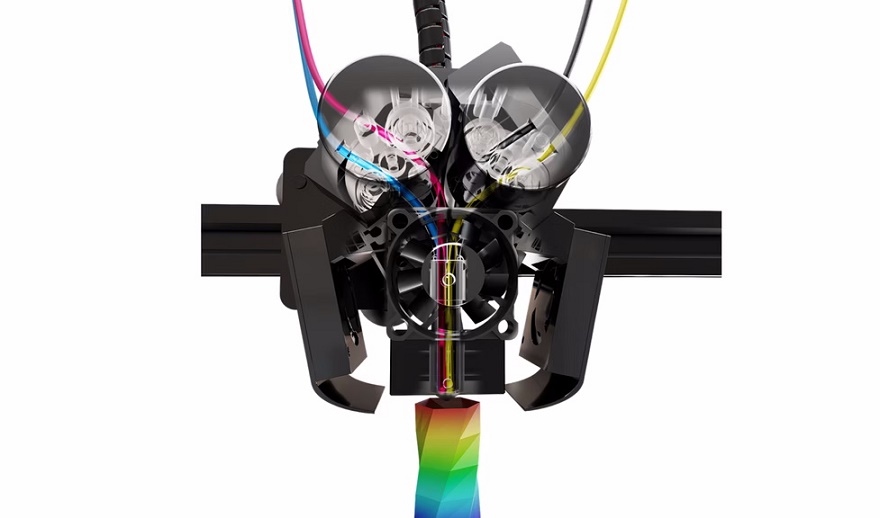
Некоторые экструзионные аддитивные системы изначально предназначены для мультиматериальной 3D-печати, например 3D-принтеры со смешивающими экструдерами. В головку одновременно заражаются два или несколько филаментов, а 3D-принтер реализует либо последовательную подачу, либо смешивание материалов в разных пропорциях. Ключевой фактор здесь — температура: так как все материалы разогреваются одним и тем же хотэндом, температуры экструзии должны быть примерно одинаковыми, иначе могут возникнуть проблемы с подачей расплава. Как результат, такой вариант используется в основном для печати разноцветными филаментами из одного и того же полимера.
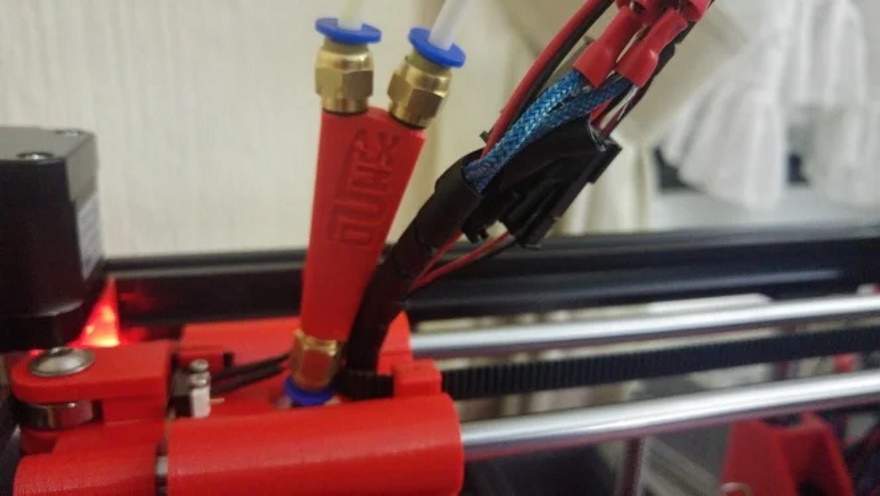
Самодельный Y-образный переходник
Еще один простой вариант — использование Y-образных разветвителей. Суть примерно та же: каждый из двух филаментов подается в отдельную трубку, трубки сходятся в одной точке, после чего материалы попеременно попадают в хотэнд. Ввиду конструкции таких переходников этот вариант применим только на системах с боуденовской подачей филамента, то есть размещением подающих механизмов на раме 3D-принтера, отдельно от головки. Здесь тоже необходимо помнить о температурах экструзии разных материалов, но в принципе в машинный код можно внести команды для приостановки укладки в процессе замены и ожидания прогрева или охлаждения хотэнда до требуемой новому полимеру температуры. Это, в свою очередь, позволяет печатать модели двумя материалами с существенной разницей в температуре плавления.
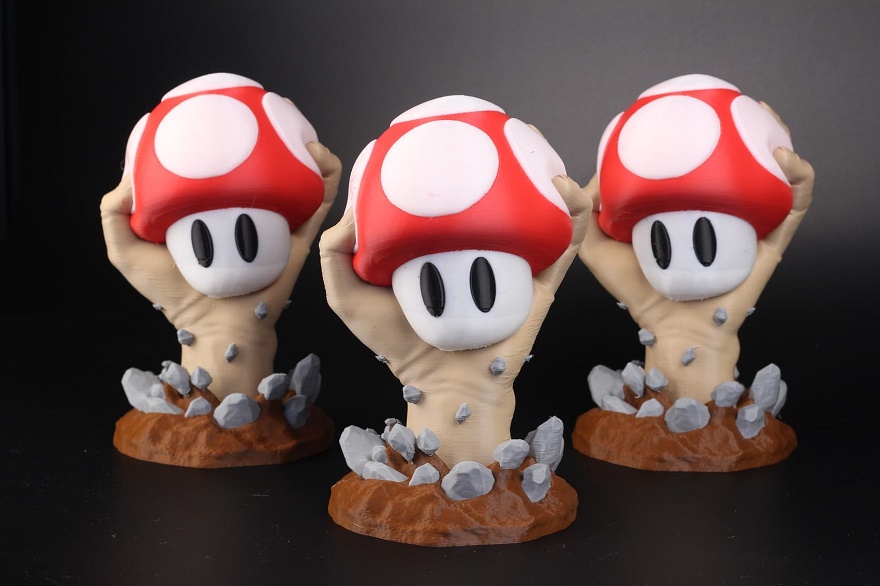
Результат 3D-печати на 3D-принтере от Bambu Lab с системой автоматической смены филамента
Самый прогрессивный вариант — оснащение одноэкструдерных 3D-принтеров системами автоматической смены филамента или сплайсерами.
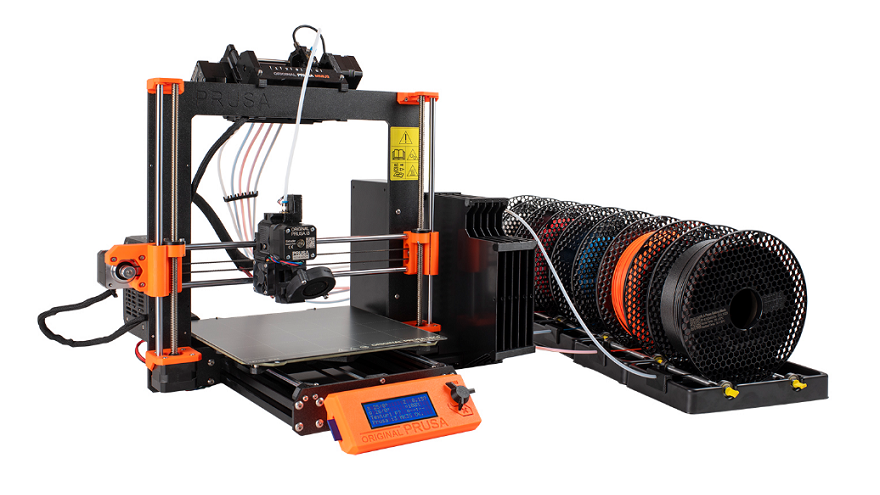
Система автоматической смены филамента MMU3 на 3D-принтере от Prusa Research
Например, чешская компания Prusa и китайская Bambu Lab предлагают опциональные автоматизированные системы, меняющие филамент по заранее заданному алгоритму без участия оператора. Количество одновременно используемых филаментов зависит от оборудования и конфигурации: системы MMU (Multi Material Upgrade) от Prusa Research принимают до пяти материалов, а системы AMS (Automatic Material System) от Bambu Lab построены по модульной схеме, где каждый модуль принимает до четырех материалов с возможностью параллельного подключения до четырех модулей и, таким образом, до шестнадцати филаментов.
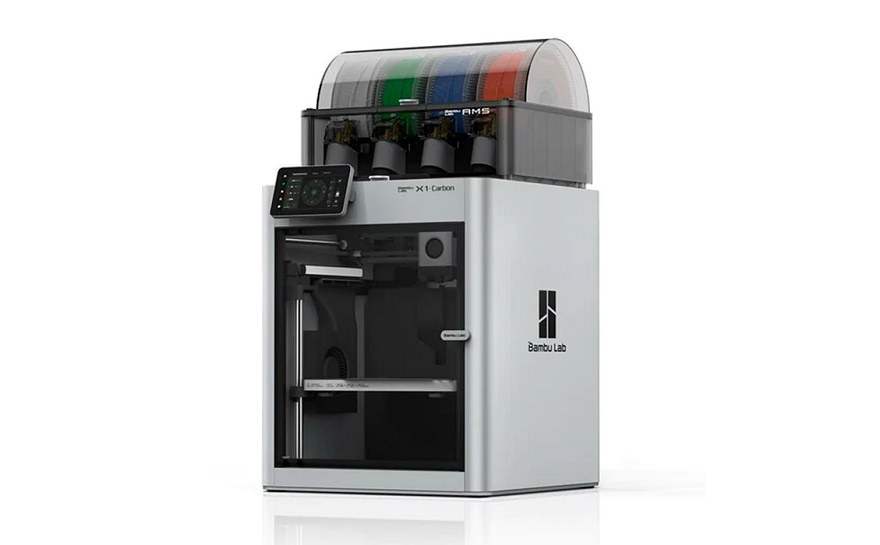
Система автоматической смены филамента AMS на 3D-принтере Bambu LabX1 Carbon
Самый известный производитель сплайсеров — канадская компания Mosaic Manufacturing. Сплайсеры Mosaic Palette работают по немного другому принципу: здесь вместо последовательной загрузки материалов разные филаменты автоматически отмеряются, обрезаются и спаиваются в непрерывную нить прямо в процессе 3D-печати.
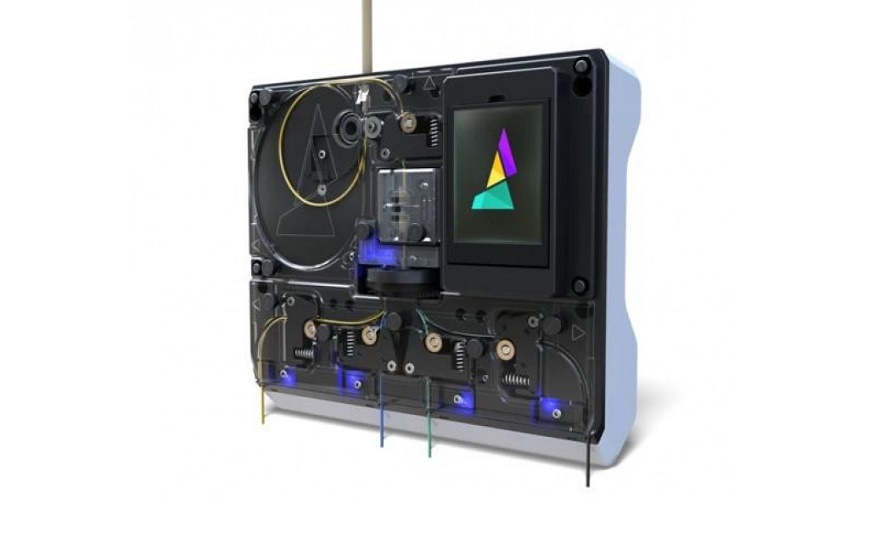
Сплайсер Mosaic Palette 2
Системы автоматической смены филамента и сплайсеры очень удобны, но c одним существенным недостатком — высоким перерасходом пластика. Для реализации четких переходов с одного оттенка на другой при смене материала приходится прогонять пластик для прочистки хотэнда от остатков предыдущего полимера. Объемы при каждой замене незначительны, но при частых сменах быстро накапливаются и в итоге дают массу отходов, тем самым повышая себестоимость и время 3D-печати.
Мультиматериальная 3D-печать на многоэкструдерных системах
Многие FDM 3D-принтеры оснащаются двумя или даже несколькими экструдерами. Наиболее распространены именно двухэкструдерные системы по упомянутой выше причине: двухэкструдерная конфигурация позволяет печатать основными и опорными материалами одновременно. Само собой, оснащение дополнительным экструдером влечет повышение стоимости оборудования, но есть и плюсы: такая схема позволяет осуществлять быстрый переход с одного материала на другой, даже если это материалы с сильно отличающимися температурами экструзии, да к тому же без образования лишних отходов, так как постоянная выгрузка материалов, загрузка новых и прочистка хотэндов не требуются — за каждый материал отвечает отдельный экструдер.
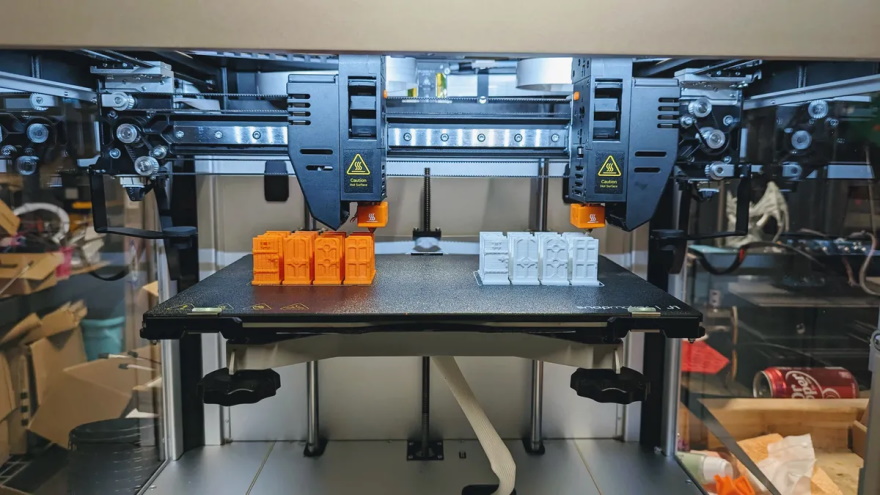
Построение в режиме копирования на IDEX 3D-принтере Snapmaker J1s
Один особенно интересный вариант двухэкструдерных 3D-принтеров — системы на кинематике IDEX (Independent Dual Extrusion). Такие 3D-принтеры оснащаются не просто двумя экструдерами, а двумя отдельными головками с независимым позиционированием по оси X. Преимущества обычной двухэкструдерной 3D-печати сохраняются, но когда мультиматериальная 3D-печать не требуется, можно значительно повышать производительность, параллельно печатая сразу две модели. Единственное ограничение — форма: так как головки независимы только по оси X, одновременно выращиваемые модели должны быть либо идентичной геометрии, либо зеркальными отражениями друг друга.
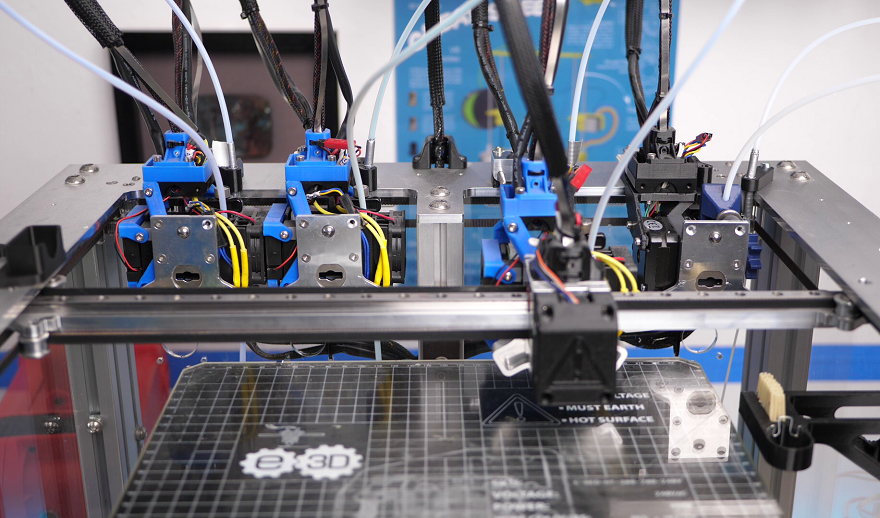
3D-принтер с системой автоматической смены инструмента компании E3D
Самый же продвинутый вариант многоэкструдерных 3D-принтеров — тулченджеры, то есть системы автоматической смены инструмента. Здесь вместо смены филамента в одной головке осуществляется смена самих головок и других насадок, например фрезерных шпинделей или лазерных граверов. Помимо очевидного преимущества в виде возможности проведения механической или лазерной обработки наряду с 3D-печатью, такая схема позволяет работать с достаточно большим количеством материалов, так как припаркованные головки не нагружают кинематику и не мешают работе активного инструмента. С другой стороны, такие системы весьма сложны конструктивно, а следовательно дороги.
Применение и нюансы мультиматериальной 3D-печати
Главная задача мультиматериальной 3D-печати — изготовление изделий с градиентными свойствами, будь то оттенки, физико-механические или химические свойства на разных участках. Печатая разными материалами можно менять матовость и глянец, эластичность и жесткость, температуру тепловой деформации и другие характеристики, а также создавать композиты с оболочками из одних материалов и наполнителями из других, либо просто использовать специализированные опорные материалы.
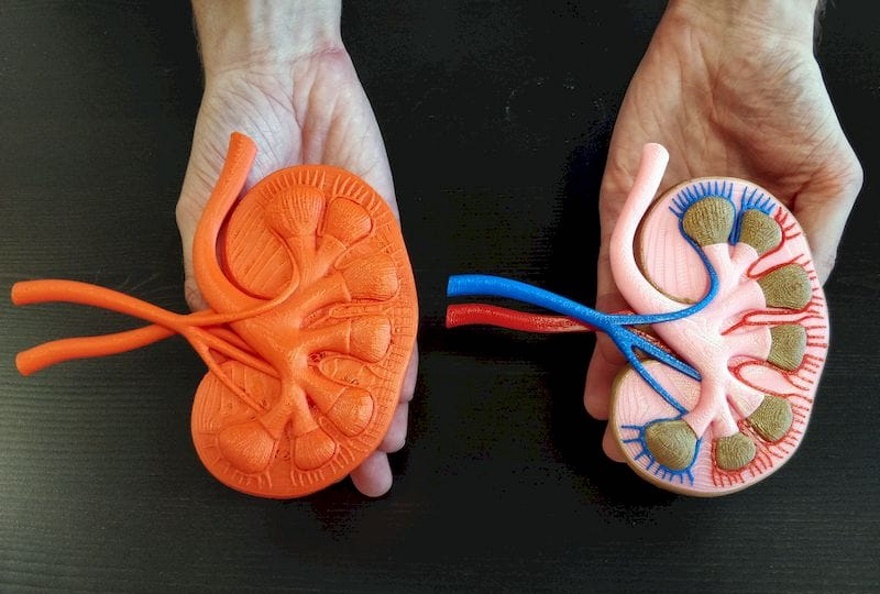
Широко распространенные примеры применения мультиматериальной 3D-печати включают изготовление протезов, микрожидкостных лабораторных систем, твердых робототехнических хватов с мягкими поверхностями для улучшения сцепления с манипулируемыми предметами, композитных деталей с наполнителями из армирующих волокон, не говоря уже об игрушках и сувенирной продукции.
При работе с разными материалами необходимо учитывать индивидуальные характеристики и совместимость разных полимеров в плане адгезии: не все термопласты хорошо схватываются друг с другом, а потому при параллельной 3D-печати несовместимыми полимерами может пострадать прочность конечных изделий. Например, чистые полиамиды (нейлоны) при всех своих великолепных механических и химических свойствах c трудом схватываются с другими полимерами, а следовательно плохо подходят для мультиматериальной 3D-печати.
По поводу совместимости разных материалов рекомендуем ознакомиться с постом по этой ссылке.
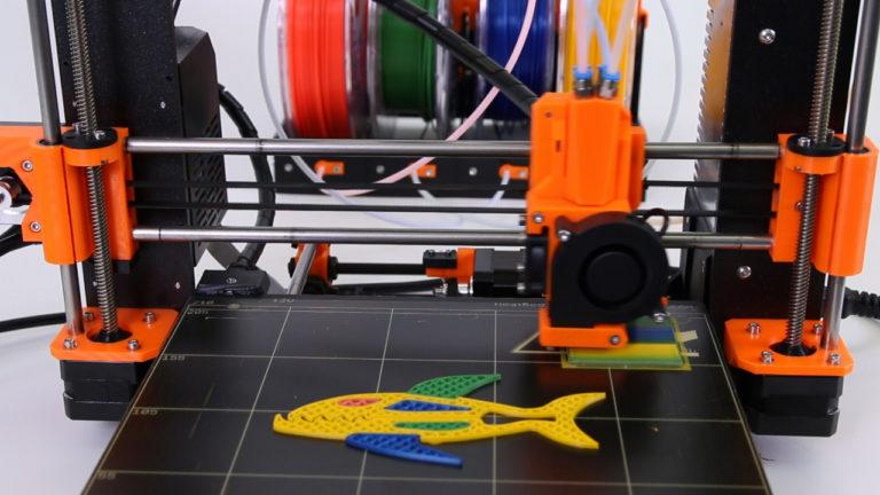
Помимо совместимости необходимо учитывать и индивидуальные параметры 3D-печати, включая температуру экструзии, скорость подачи и ретракта, температуру столика и другие факторы, зачастую сильно разнящиеся от полимера к полимеру. При смене материала в одном хотэнде необходимо не только перенастраивать температуру экструзии, но и прогонять остатки предыдущего полимера, иначе при переходе на пластик с более низкой температурой плавления может образоваться пробка. При работе с двумя или несколькими экструдерами необходимо точно настраивать ретракт, а по возможности, например при эксплуатации 3D-принтеров с кинематикой IDEX, вообще парковать неактивные головки во избежание загрязнения печатаемых изделий капающим расплавом.
Если у вас возникли вопросы, свяжитесь с нами, и специалисты REC будут рады помочь с подбором расходных материалов и аддитивного оборудования.
Чтобы написать отзыв нужно авторизоватся
Вход через социальные сети