В этой статье расскажем о том, какие бывают полимеры, об основных факторах, влияющих на качество и производительность FDM 3D-печати, и о взаимосвязи свойств термопластов и параметров экструзии.
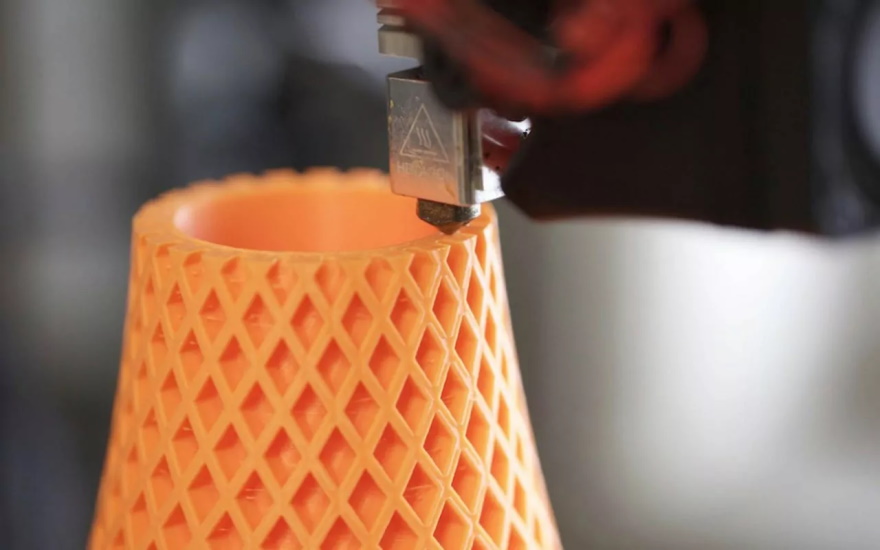
Содержание:
- Виды полимеров
- Виды термопластов
- Гигроскопичность
- Текучесть, усадка и пробки
- Когезия и прочность
- Производительность, диаметр сопла и обдув
1. Виды полимеров
Все полимеры можно разделить на две группы — реактопласты и термопласты.
В первых при полимеризации (сшивании макромолекул) происходят в основном необратимые химические изменения, так что они не подлежат переработке во вторичное сырье. К реактопластам относятся эпоксидные, полиэфирные, карбамидные и другие смолы. В число реактопластов входят и фотополимеры, используемых в стереолитографической 3D-печати, хотя некоторые фотополимерные смолы могут быть деполимеризованы.
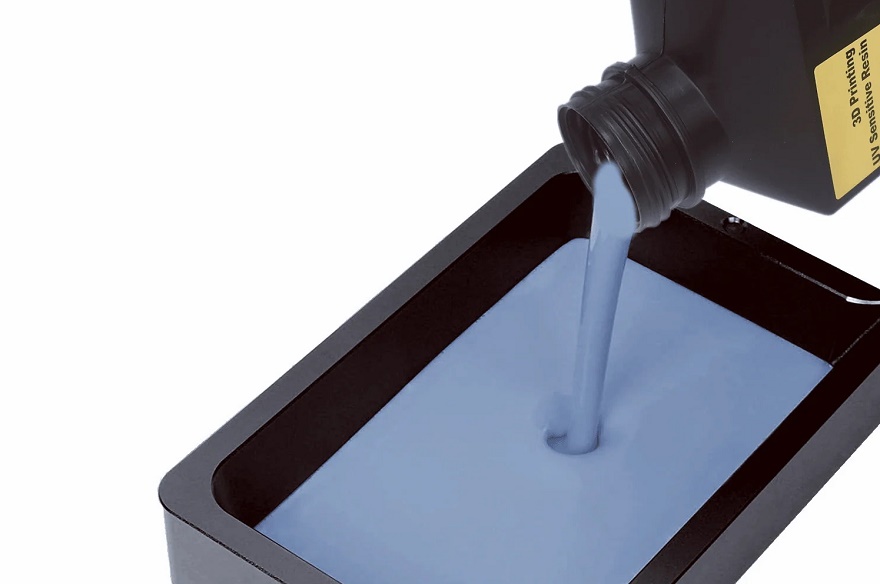
Фотополимер в исходной, жидкой форме
В термопластах соседствующие макромолекулы связываются силами Ван-дер-Ваальса, а процессы затвердевания и размягчения обратимы. Способность размягчаться и плавиться при нагревании, а затем набирать прочность при охлаждении и позволяет использовать термопласты в экструзионных (FDM/FFF) 3D-принтерах. Так как статья посвящена FDM 3D-печати, далее речь пойдет исключительно о термопластичных полимерах.
Каждая макромолекула полимера состоит из звеньев — мономеров. Степень полимеризации определяется молекулярной массой: чем больше в макромолекуле звеньев, тем выше масса. Молекулярная масса влияет на физико-механические характеристики, к чему мы еще вернемся во главе про текучесть, усадку и пробки.
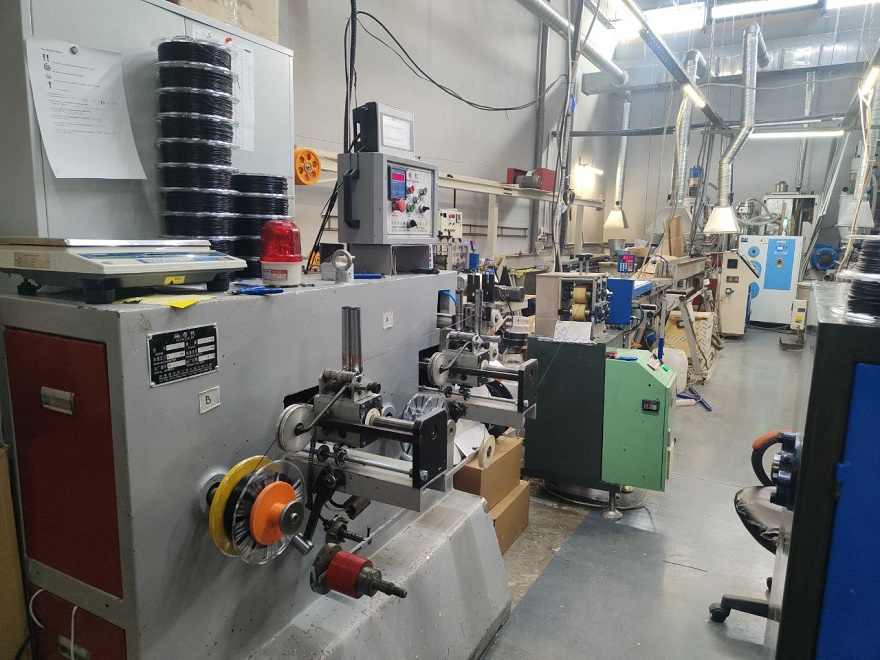
Производство филаментов на мощностях REC
Термопласты не просто пригодны к переработке, но и проходят переработку как минимум дважды перед тем, как превращаются в привычные расходные материалы для FDM 3D-принтеров: первый раз — в гранулы, второй — в филаменты. Непосредственно 3D-печать — это уже третья переработка, как и изготовление филаментов из вторичного сырья.
Использование вторичного сырья в производстве расходных материалов возможно, хоть и проблематично из-за неоднородности по массе, усложняющей контроль давления в промышленных экструдерах и, как результат, контроль диаметра филамента.
Термопласты тоже можно разделить на две группы — гомополимеры и сополимеры. Гомополимеры состоят из одинаковых по составу повторяющихся мономерных звеньев, а сополимеры — из двух или более различных структурных звеньев. К гомополимерам, например, можно отнести полистирол и полипропилен, к сополимерам акрилонитрилбутадиенстирол (ABS, АБС).
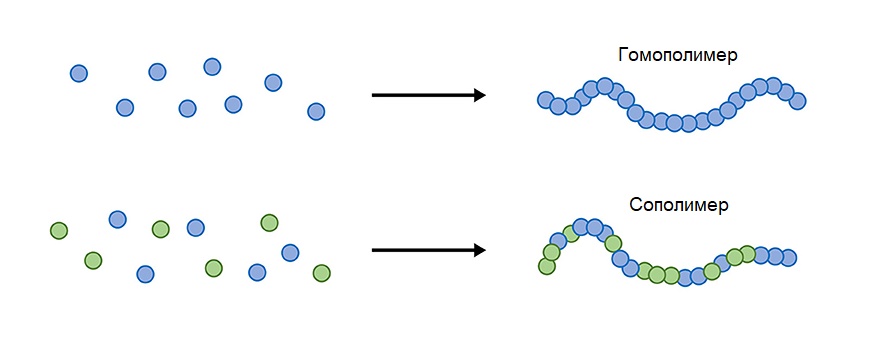
Важная разновидность сополимеров — блок-сополимеры, макромолекулы которых состоят из регулярно или статистически чередующихся гомополимерных блоков, различающихся по составу или строению. Иными словами, блоки твердых термопластов (полистирола, полиэтилена, полипропилена) чередуются с блоками эластомеров (полибутадиена, полиизопрена, статистических сополимеров бутадиена со стиролом или этилена с пропиленом). В группу блок-сополимеров входят синтетические каучуки и термоэластопласты.
2. Виды термопластов
Термопласты также можно разделить еще на две, но уже условные группы — аморфные и кристаллические. Условные, потому что в реальности чисто аморфные или чисто кристаллические полимеры практически не встречаются, а некоторые вообще классифицируются как полукристаллические. Разница в структуре.
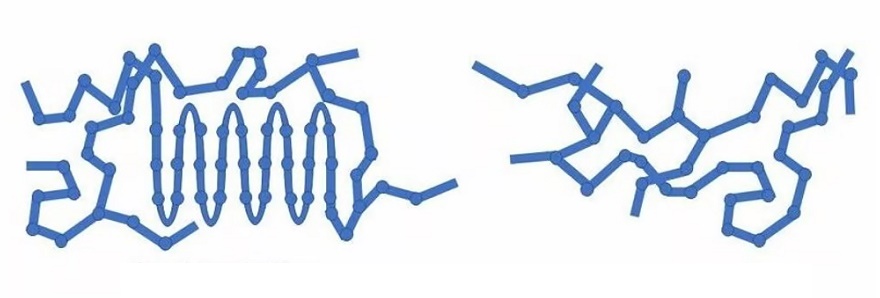
Условная структура полукристаллического (слева) и аморфного полимера (справа)
Структура аморфных полимеров никак или почти никак не упорядочена, то есть хаотична и напоминает этакую вермишель. Такие материалы обычно обладают повышенной вязкостью и, как следствие, высокой ударной прочностью, но не всегда: например, полистирол аморфен, но при этом довольно хрупок.
Структура кристаллических полимеров наоборот заметно упорядочена, но в разной степени — отсюда нередкая необходимость в опять-таки условном разделении на кристаллические и полукристаллические. Чем выше степень кристаллизации, тем выше жесткость, но зачастую ценой хрупкости. Степень кристаллизации может зависеть от добавок и режимов термообработки.
В группу кристаллических и полукристаллических полимеров входят полипропилен, полиэтилен, полиамиды (нейлоны), полифениленсульфид (PPS, ПФС), полиэтилен разной плотности, поликарбонаты, полиэфирэфиркетон (PEEK, ПЭЭК). Примеры аморфных полимеров включают акрилонитрилбутадиенстирол (ABS, AБС) и акрилонитрилстиролакрилат (ASA, АСА), полистирол, поликарбонат, полисульфон (PSU, ПСФ), полиметилметакрилат (оргстекло).
Некоторые полимеры могут в зависимости от варианта быть как аморфными, так и полукристаллическими, например полиэтилентерефталат (PET, ПЭТ) и полиэтилентерефталатгликоль (PETG, ПЭТГ). ПЭТ полукристаллический полимер, а ПЭТГ аморфный с вытекающей разницей в свойствах. Тут необходимо пояснить, что названия могут ввести в заблуждение, так как оба варианта содержат гликоли, только разные и в разных пропорциях: ПЭТ содержит этиленгликоль, а в ПЭТГ часть этиленгликоля замещается еще одним гликолем — циклогександиметанолом.
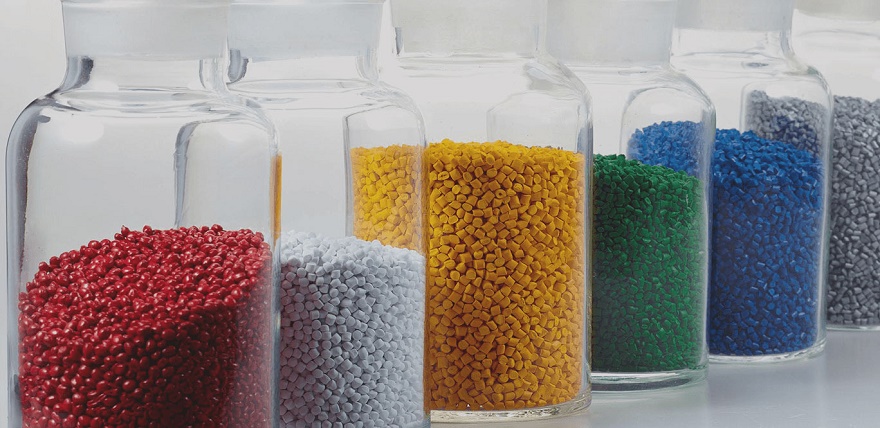
Из общих правил заметно выбивается полилактид (PLA, ПЛА). Это биополимер, получаемый поликонденсацией молочной кислоты. К молоку материал никакого отношения не имеет: молочная кислота добывается из растительных источников, как правило кукурузы, реже сахарного тростника. К репутации полилактида как абсолютно безопасного полимера натурального происхождения тоже следует относиться с осторожностью, так как конечный химический состав зависит исключительно от производителя. Например, в качестве стабилизатора обычно используется 2-этилгексаноат олова, а при слишком высокой концентрации в процессе производства остаточный химикат может вызывать раздражение слизистых оболочек и дыхательных путей.
Полилактид демонстрирует стереоизомерию, то есть способность молекул при одних и тех же связях формировать зеркальные структуры. От конфигурации зависят конечные свойства полимера. Например, L-лактид — это кристаллизующийся полимер с ярко выраженным порогом стеклования и высокой хрупкостью, а смесь L-лактида и D-лактида дает уже аморфный полимер — менее хрупкий, но без четкой температуры плавления.
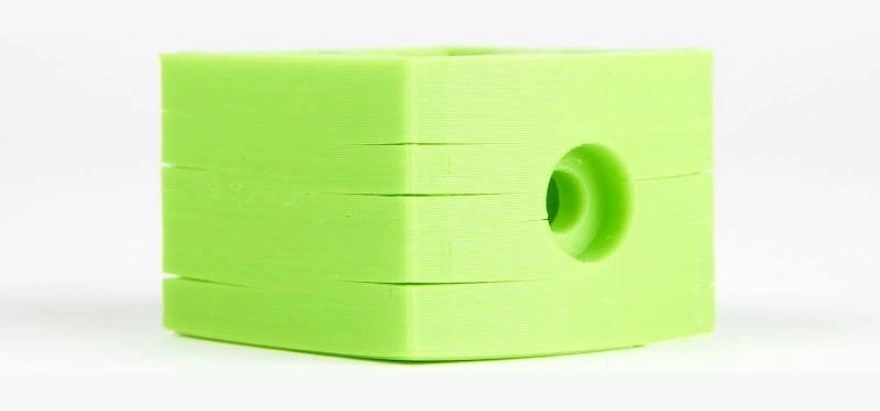
Одна из важнейших характеристик пластиков для 3D-печати — усадка. Как правило, кристаллические полимеры обладают повышенной усадкой, а следовательно более предрасположены к короблению и растрескиванию. Например, усадка полиамидов (нейлонов) может составлять 1,5-2,5%, полипропилена 1,8-2,5%, а полиэтилена 2-5%. Акрилонитрилбутадиенстирол (ABS, АБС) хоть и относится к аморфным, может быть частично кристаллизованным, а потому усадка в зависимости от марки может колебаться в диапазоне 0,4-2%. Усадка аморфного полистирола — 0,4-0,8%.
3. Гигроскопичность
Все полимеры впитывают влагу, но в разной степени. Тем не менее, даже конденсат на поверхности филамента может приводить к очень неприятным последствиям. При попадании в хотэнд влага вскипает, а это может приводить к неравномерной подаче расплава. Отсюда следует, что филаменты необходимо хранить в сухом месте, а непосредственно перед 3D-печатью крайне желательно просушивать, особенно при эксплуатации 3D-принтера во влажном климате.
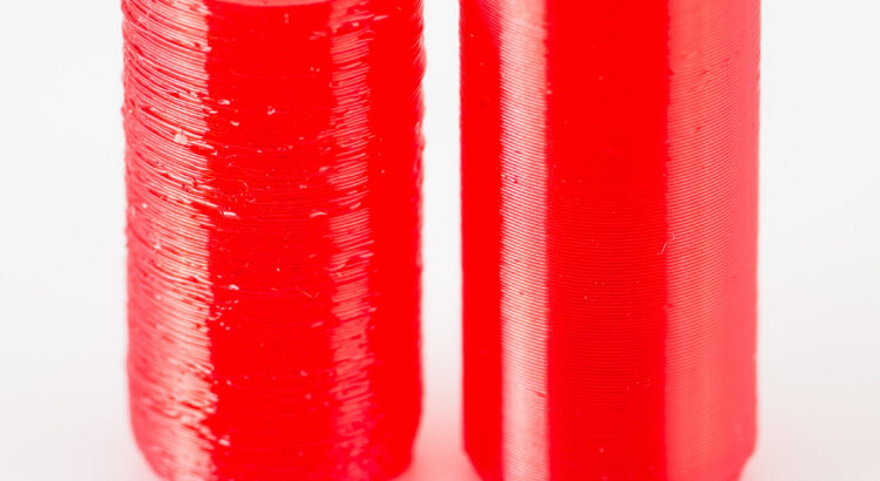
Примеры 3D-печати влажным (слева) и сухим филаментом (справа)
Ответственные производители расходных материалов делают то же самое: еще перед протягиванием филамента исходный гранулят просушивается в течение нескольких часов, чтобы диаметр нити был максимально стабильным. Если пропустить этот этап, можно получить не только плавающий диаметр, но и пузырьки в филаментах, а это чревато проблемами с подачей в хотэнд и все той же нестабильностью экструзии. Просушиванием в домашних условиях пузырьки удалить вряд ли получится, так что такие товары следует считать браком и возвращать продавцу.
Подробно про хранение и просушивание филаментов рассказывается в отдельных статьях (тут и тут), а пока приведем несколько примеров.
Рекордсмен в плане гигроскопичности — вышеупомянутый полилактид (PLA, ПЛА), способный впитывать до 4% от собственной массы. Второе место занимают полиамиды: например, нейлон-66 впитывает до 0,4% значительно меньше полилактида, но все равно очень существенно. На третьем месте акрилонитрилбутадиенстирол (ABS, АБС) со средним показателем 0,2%.
4. Текучесть, усадка и пробки
Текучесть выражается показателем текучести расплава, сокращенно ПТР. Эта цифра показывает, какой объем материала вытечет через техническую дырку (например, фильеру) под заданным давлением и при заданной температуре в течение заданного времени. Чем эта цифра ниже, тем ниже текучесть, то есть выше «густота» полимера.
Низкие показатели косвенно говорят о высокой молекулярной массе, а высокая молекулярная масса, как правило, свидетельствует о повышенных механических свойствах, в частности прочности и ударной стойкости. По этой причине высокопрочные, инженерные термопласты нередко требуют высокой температуры экструзии — для повышения текучести до приемлемого уровня. Если хотэнд едва справляется с задачей, темп подачи может быть довольно низким из-за высокой нагрузки «густого» расплава на подающий механизм (фидер). Отчасти это компенсируется повышением текучести с повышением скорости потока, так как полимерные расплавы — не ньютоновские жидкости.
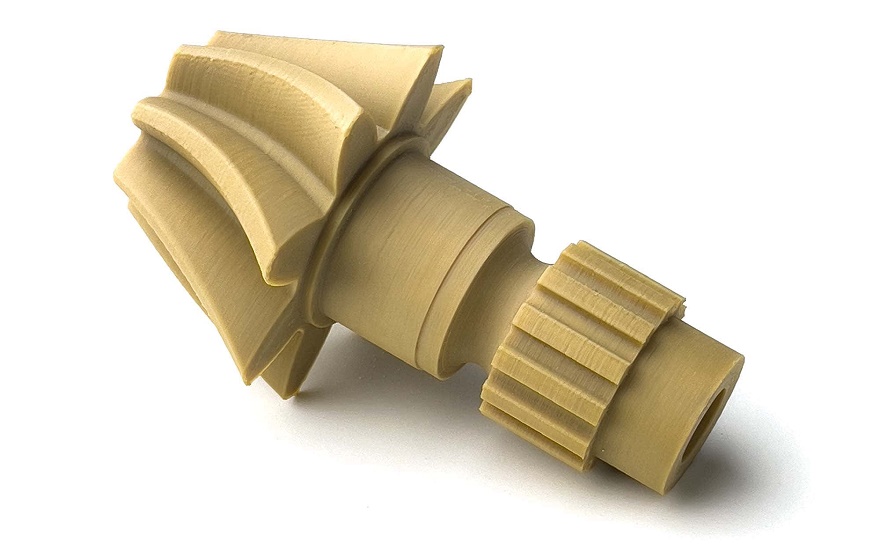
Пример 3D-печати тугоплавким конструкционным термопластом полиэфирэфиркетоном (PEEK, ПЭЭК)
Текучесть (и производительность) можно улучшить дополнительным повышением температуры экструзии, но тут кроются сразу два подвоха.
Во-первых, чем выше температура расплава, тем выше тепловое расширение, а следовательно выше и последующая усадка. При определенной температуре когезия (схватывание слоев между собой) окажется недостаточной. Другими словами, чрезмерный нагрев материала во время экструзии повышает риски деформаций и растрескивания по мере остывания уложенных слоев.
Во-вторых, при перегреве можно получить термическую деструкцию полимеров. Для акрилонитрилбутадиенстирола (ABS, АБС) этот порог находится в районе 260°С, а для полилактида (PLA, ПЛА) в районе 220-230°С. Это означает не только потерю прочности, но и тепловое расширение, в свою очередь способное забить хотэнд: чем больше расплав будет увеличиваться в объеме при нагревании, тем выше будет давление, а чем выше давление, тем сильнее трение о стенки хотэнда. Если давление и трение будут слишком высокими, фидер просто перестанет справляться с подачей расплава, и образуется пробка.
Отсюда следует, что не стоит пренебрегать настройками температуры хотэнда, рекомендуемыми производителями, ибо выше — не всегда лучше. В то же время возникает еще один вопрос: почему производители указывают допустимый диапазон температур, а не какое-то конкретное, оптимальное значение?
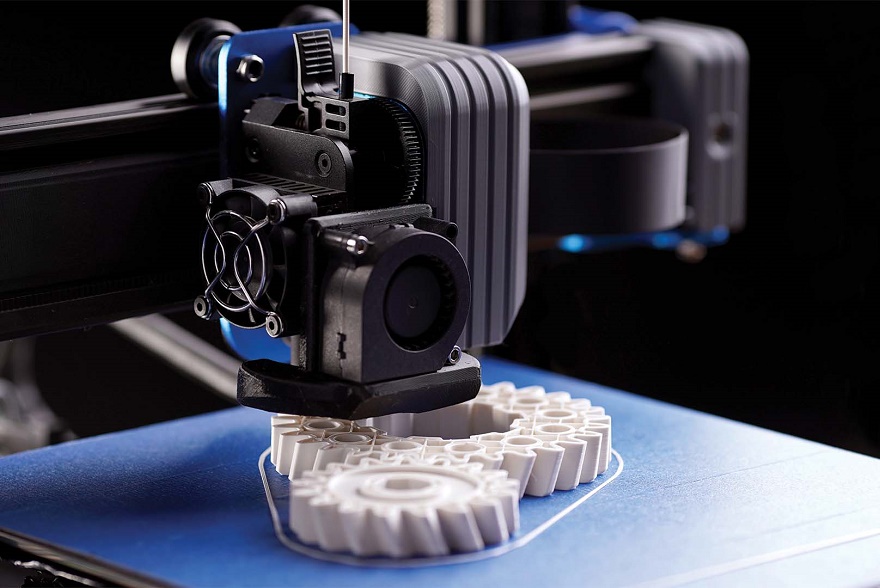
Ответ кроется в необходимости баланса между скоростью, прочностью и детализацией. Если не выходить за рекомендуемый диапазон, максимальные значения температуры экструзии дадут оптимальную прочность, так как слои будут хорошо схватываться друг с другом, но без чрезмерной усадки, способной привести к образованию трещин по тем же слоям.
С другой стороны, при минимальных значениях расплав будет охлаждаться быстрее и демонстрировать наименьшую усадку, к тому же темпа подачи хватит для печати соплом (фильерой) малого диаметра. Это плюсы к детализации, но в то же время минусы к когезии и, соответственно, прочности. К соплам мы вернемся в следующих главах.
Температуру следует подбирать в зависимости от поставленной задачи: для нагруженных деталей может потребоваться температура повыше, а для декоративных изделий может быть предпочтительна относительно низкая температура.
5. Когезия и прочность
Прочность 3D-печатных изделий на разрыв в немалой степени определяется когезией (межслойной адгезией), а когезия зависит от температуры, но как мы уже установили, для каждого полимера есть свой температурный порог. Можно ли как-то дополнительно повысить прочность схватывания? Можно, но для этого придется поиграть с толщиной слоев, шириной линий и диаметром сопла.
Начнем с того, что FDM 3D-принтеры укладывают линии разной степени овальности. Сами нити расплава — круглые в сечении, но по мере укладки расплющиваются в той или иной степени. Контакт и схватывание при этом происходят не только с линиями в предыдущем слое, но и соседними линиями в том же слое. Чем выше площадь контакта соседствующих линий, тем выше когезия и, соответственно, прочность.
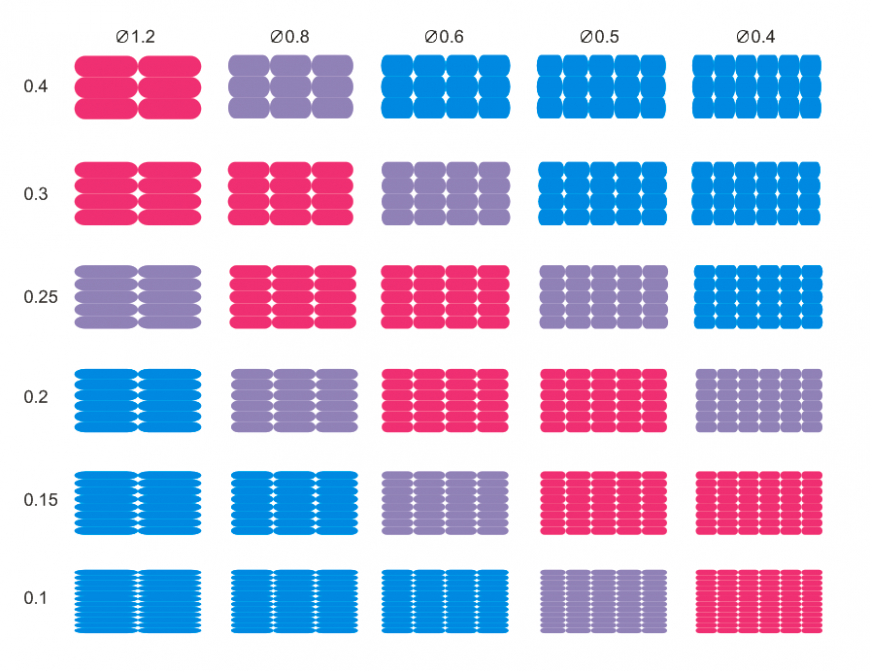
Так как у линий в поперечном разрезе нет ярко выраженных углов, вместо углов будут оставаться полости. Это означает, что 3D-печать относительно толстыми слоями дает более высокую прочность — чем меньше линий, тем меньше полостей, следовательно структура выходит плотнее, ближе к монолитной. Но все не так просто, ведь площадь контакта будет зависеть не только от толщины, но и от овальности: сильно сплющенные линии будут давать хороший контакт с предыдущими слоями, но меньший с соседствующими линиями в том же слое. Соответственно, необходимо искать золотую середину, подбирая оптимальную толщину и ширину линий под диаметр сопла.
Интересный момент заключается в разнице между фактическим и программным диаметром сопла (той самой шириной линий). Многие слайсеры позволяют выставлять разную ширину линий для разных участков моделей, например периметров и заполнения. Для пущей прочности ширину при печати заполнения можно выставить выше, чем фактический диаметр сопла. Это повысит выход расплава и поможет вдавливать пластик в те самые полости между линиями, способствуя повышению когезии. При укладке периметров, формирующих стенки и внешние поверхности, ширину линий можно наоборот снизить, что будет способствовать повышению детализации.
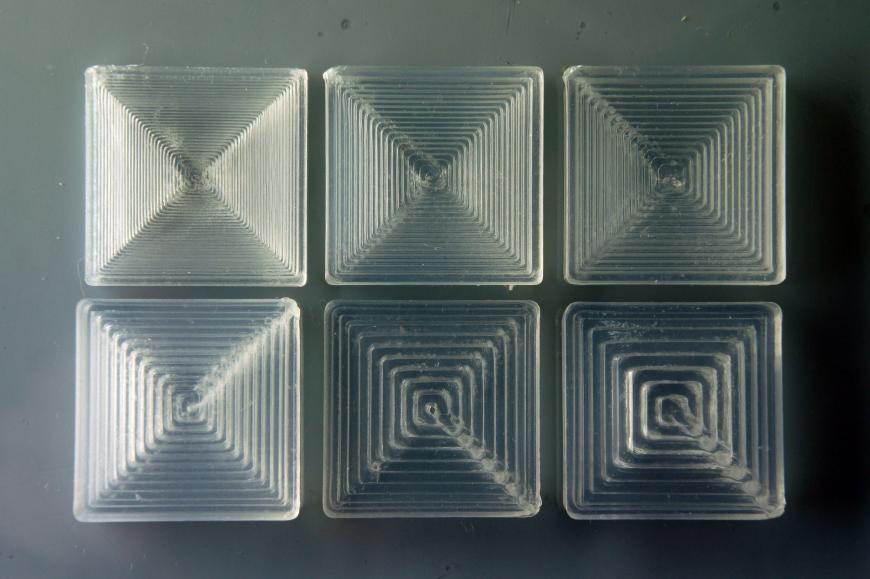
Здесь тоже нужно быть осторожными: хотэнд должен справляться с заданным темпом подачи, к тому же избыточная подача может привести к образованию наплывов на стенках. Слишком низкая ширина линий наоборот может привести к пропускам, так что чрезмерно отклоняться в ту или иную сторону не следует.
6. Производительность, диаметр сопла и обдув
Максимальная скорость печати, а точнее производительность, напрямую зависит от максимального темпа подачи расплава, а темп, в свою очередь, зависит от мощности хотэнда. Есть и другие ограничители, например диаметр сопла, где немаловажную роль играет разобранная выше текучесть, зависящая от материала и опять-таки от температуры. Само собой, скорость позиционирования головки тоже играет роль и может быть ограничителем, если кинематика не позволяет в полной мере использовать возможности экструдера.
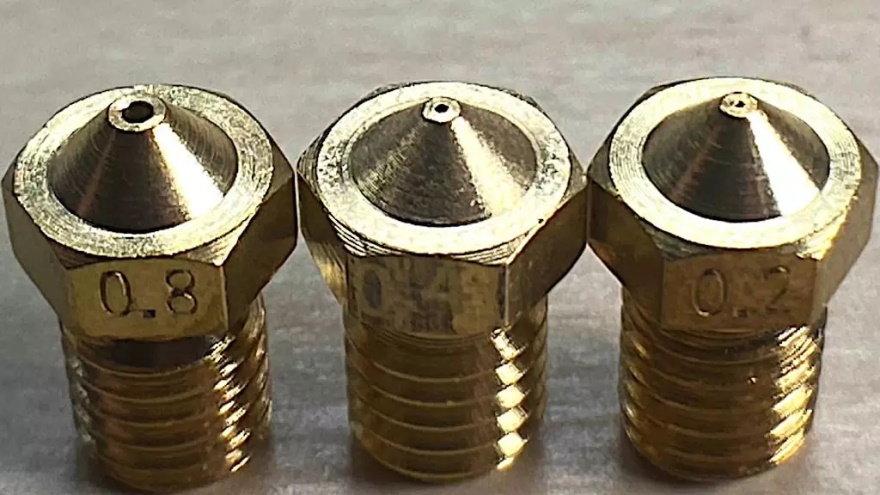
В повседневной эксплуатации максимальная мощность хотэнда и возможности кинематики остаются постоянными, а вот сопла можно менять в зависимости от требуемого диаметра и материала сопла: в основном используются латунные, но при 3D-печати абразивными материалами, например угле- или стеклонаполненными композитами, желательно использовать более износостойкие варианты из закаленной стали, с покрытиями из карбида вольфрама или даже вставками из синтетических камней — рубинов, сапфиров или алмазов.
Для повышения производительности в большинстве случаев необходимо повышать температуру экструзии, но не выходя за допустимый диапазон, а также увеличивать диаметр сопла: для повышения объема подачи расплава в два в раза диаметр необходимо увеличить примерно в полтора. Старайтесь иметь под рукой набор фильер под разные задачи — диаметром от 0,2 мм для максимальной детализации до 1,2 мм или выше для высокой производительности.
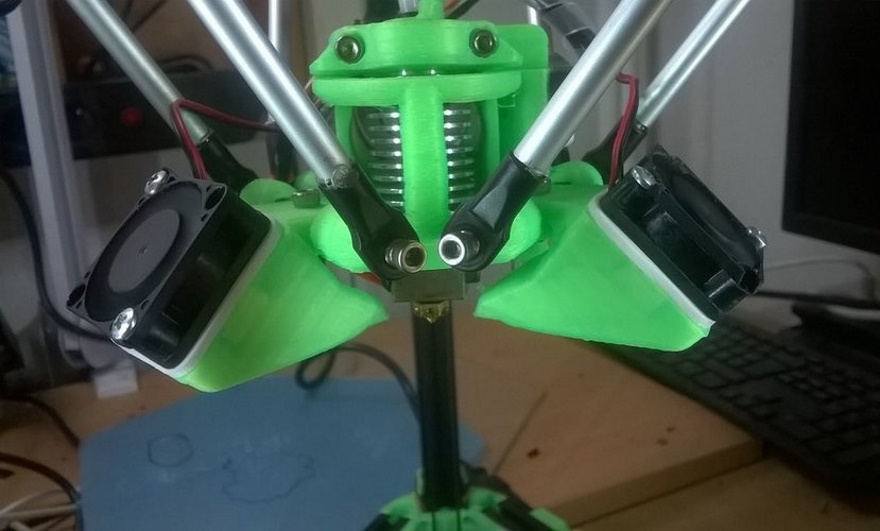
Вентиляторы обдува на головке дельта-принтера
При всем этом не стоит забывать и про охлаждение расплава после укладки, иначе наклонные стенки будут сползать, мостики — провисать, а основания — сплющиваться под массой нагромождаемого полимера. Охлаждение происходит естественным путем, но зачастую требуется и принудительное с помощью вентиляторов обдува. Особенно важную роль обдув играет при работе с полимерами с низкой температурой стеклования, например полилактидом (PLA, ПЛА) и большинством эластомеров вроде термопластичного полиуретана или синтетического каучука. С другой стороны, некоторым полимерам обдув противопоказан, так что не забывайте сверяться с рекомендациями производителей.
Требуемая мощность обдува пропорциональна скорости укладки — чем выше скорость укладки, тем мощнее должен быть обдув.
Статья основана на цикле «Тонкости 3D-печати» компании Filamentarno!, опубликованном на портале 3Dtoday
Чтобы написать отзыв нужно авторизоватся
Вход через социальные сети