Серьезные задачи требуют серьезных материалов, и сегодня мы расскажем про некоторые из инженерных термопластов и композитов, используемых в экструзионной 3D-печати и доступных в нашем магазине.
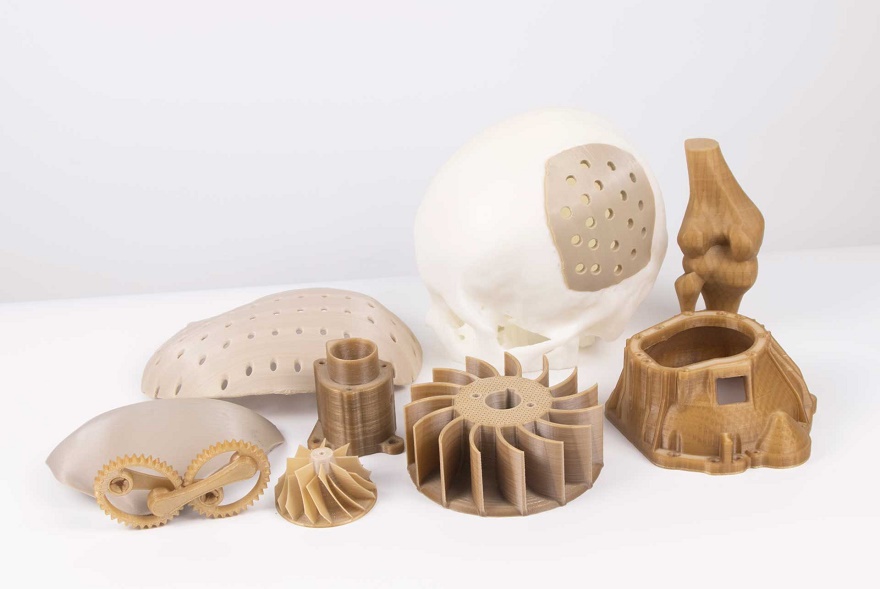
Определение инженерных пластиков довольно размыто, но обычно неофициально к этой категории причисляют полимеры, рассчитанные на активную эксплуатацию под механическими нагрузками и с теплостойкостью не менее 100°С. Химическая стойкость тоже нередко играет важную роль, например при контакте с горюче-смазочными материалами.
Если исходить из этого определения, полилактид (PLA) и полиэтилентерефталатгликоль (PETG) отметаем сразу, хотя в среде любительской 3D-печати это одни из самых популярных материалов. Оба очень просты в обращении, не требуя дорогих, хорошо оснащенных 3D-принтеров, но физико-механические характеристики далеки до «инженерного» уровня».
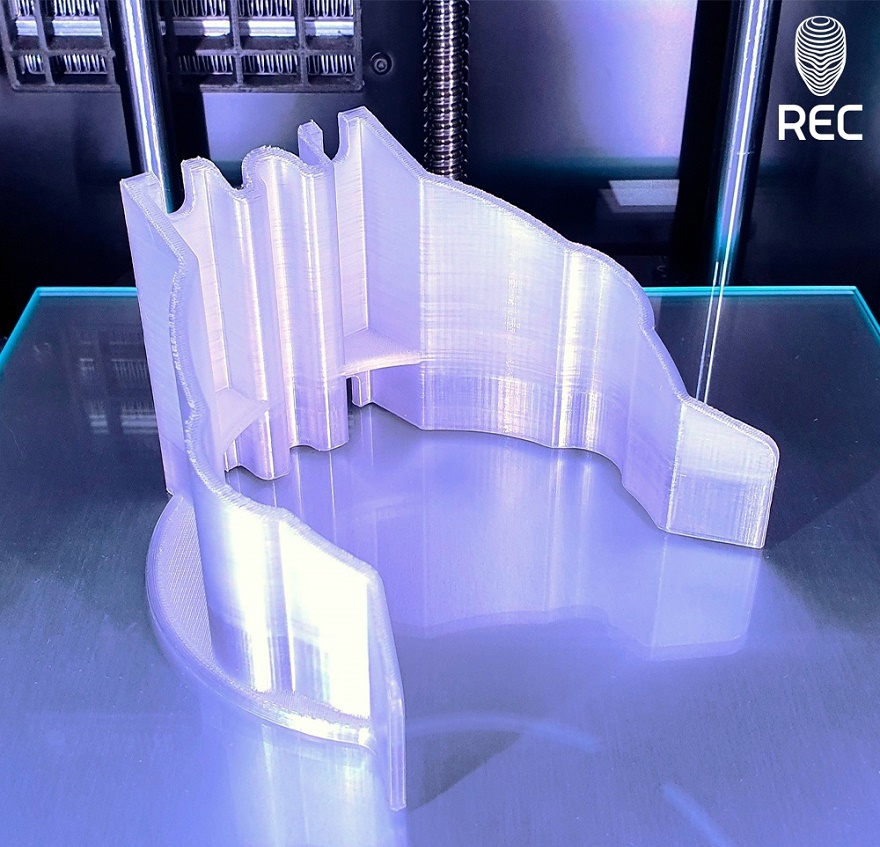
Аквариумное крепление из полиэтилентерефталатгликоля (REC Relax)
Особенно это касается полилактида как хрупкого и весьма легкоплавкого полимера с температурой размягчения где-то в районе 60°С, недостаточной даже для пребывания на солнце жарким летним днем. С PETG обстоят лучше: он гораздо прочнее, особенно при ударных нагрузках, и держит продолжительные эксплуатационные температуры до 70-80°С, но все же до инженерного пластика не дотягивает.
Это вовсе не означает, что такие материалы бесполезны. Ценовая доступность, простота 3D-печати и нетокcичность — уже важные факторы, да и с практическим применением все хорошо: из PLA и PETG делают всякую всячину, начиная с игрушек и заканчивая вполне себе механическими деталями, только не промышленного уровня. PLA к тому же отлично подходит для 3D-печати выжигаемых литейных мастер-моделей, а PETG в комбинации со стекловолоконным наполнителем дает недорогой и прочный композит, как наш REC rPETG.
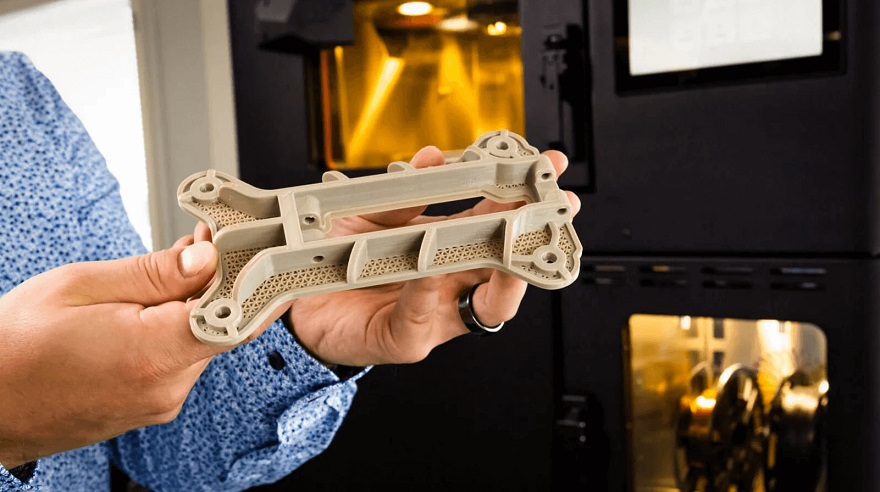
Деталь из тугоплавкого конструкционного термопласта полиэфирэфиркетона (PEEK)
На другом конце спектра материалы, именуемые тугоплавкими конструкционными термопластами. Название длинное и серьезное, но и полимеры нешуточные — как по цене, так и по характеристикам, что вполне взаимосвязано. Сюда можно отнести, например, полиэфирэфиркетон (PEEK), полиэфиримид (PEI 9085, Ultem), полисульфон (PSU), плюс более известные и привычные нейлоны и поликарбонаты. Что еще интереснее, практически любые полимеры, включая перечисленные тугоплавкие варианты, можно дополнительно армировать стеклянными, углеродными или даже арамидными волокнами, получая еще более интересные материалы, но уже композиционные.
1. Полиэфирэфиркетон (PEEK, ПЭЭК)
Нет, название этого термопласта — не результат заикания или залипающей клавиатуры. Полиэфирэфиркетон называется так потому, что содержит две эфирные и одну кетонную группу. Это подсказывает, что бывают и другие варианты. Так и есть: PEEK относится к семейству, называемому полиарилэфиркетонами или ароматическими полиэфиркетонами. Помимо PEEK сюда входят полиэфиркетонкетон (PEKK) и просто полиэфиркетон (PEK). Известный химический концерн BASF даже какое-то время выпускал полиэфиркетонэфиркетонкетон (PEKEKK). Мы этот материал не предлагаем, так как не можем выговорить название, но PEEK у нас есть.
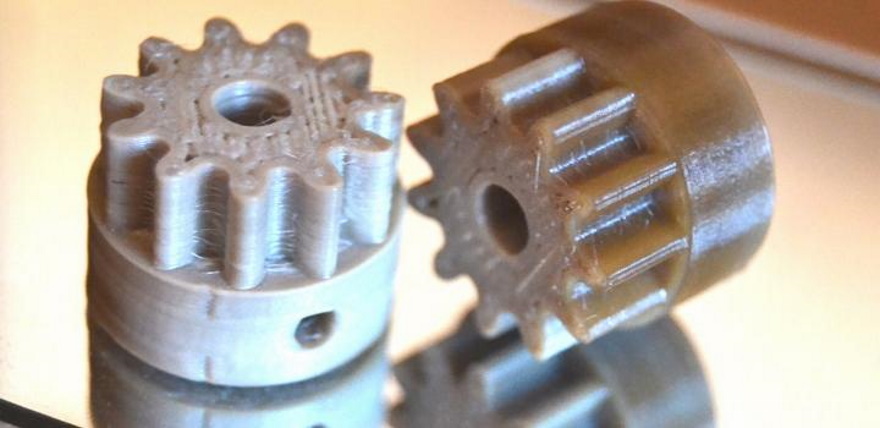
Все они достаточно близки по свойствам, но самый распространенный вариант — как раз PEEK. Этот полимер крайне термостоек, выдерживая продолжительную эксплуатацию при температурах до 275°С, да к тому же негорюч. Добавьте сюда стойкость к большинству растворителей, за исключением концентрированных серных и азотных кислот, плюс превосходные диэлектрические свойства, и получается весьма привлекательный инженерный материал.
Высокая прочность и ударная стойкость PEEK напрямую связаны с его полукристаллической структурой, но она же создает довольно серьезные сложности при 3D-печати. Дело в том, что одного лишь нагревания до 400°С для стабильной экструзии недостаточно, материал нужно еще и правильно, медленно охлаждать после построения детали, а иногда и отжигать (повторно нагревать), иначе в процессе рекристаллизации часть прочности может быть утеряна. Подробнее про 3D-печать полиэфирэфиркетоном и требуемое оборудование рассказывается в отдельной статье.
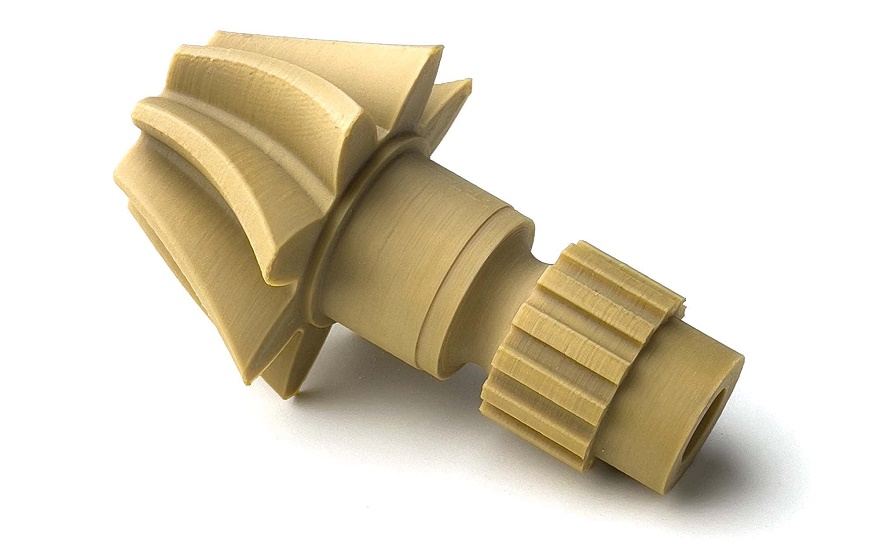
Благодаря отличному сочетанию физических и химических свойств PEEK используют в производстве самых разных нагруженных деталей, включая элементы несущих конструкций, подшипники, поршни, клапаны, и прочая. В целом этот материал рассматривается как полимерная альтернатива легким сплавам, особенно алюминиевым: при примерно той же массе зачастую можно получать изделия, более близкие по прочности к стальным.
Более того, в чистом виде PEEK еще и бисовместим, благодаря чему нашел применение в пищевой промышленности и даже в медицине в качестве материала для производства эндопротезов, например заплаток для краниопластики. Кстати, наш вариант PEEK тоже имеет сертификат допуска к контакту с пищевыми продуктами.
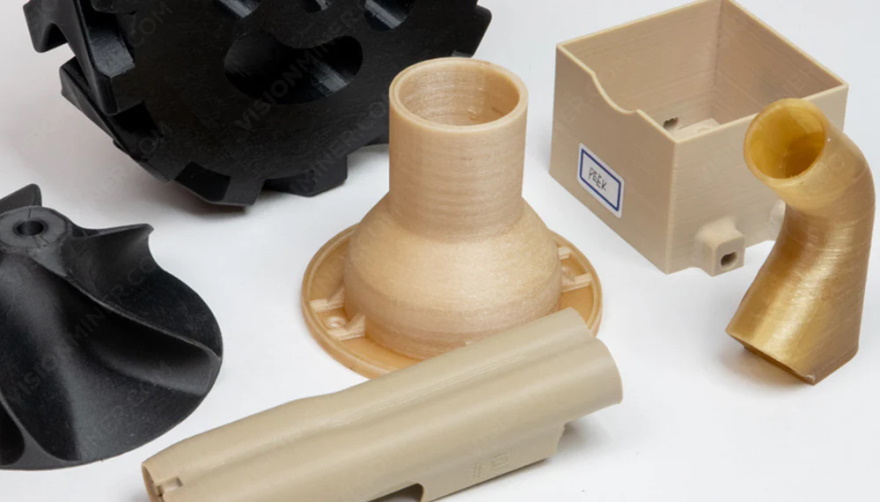
Полиэфиркетонкетон (PEKK) очень похож на PEEK и тоже применяется в промышленной 3D-печати в тех же целях. От более известного собрата этот вариант отличается несколько более высокой температурой стеклования и более медленной кристаллизацией, что с одной стороны требует более высоких трудо- и энергозатрат, а с другой помогает несколько точнее контролировать рабочие процессы. В остальном PEEK и PEKK аналогичны.
Чтобы написать отзыв нужно авторизоватся
Вход через социальные сети