В этой статье мы поделимся примером применения стеклонаполненного композиционного филамента PEEK GF-30 на основе конструкционного термопласта полиэфирэфиркетона в аддитивном производстве деталей для химической промышленности.
Этой историей с нами поделилась волгоградская компания-производитель 3D-принтеров Volgobot. Как и многие предприятия в сфере производства аддитивного оборудования и расходных материалов, включая нас, Volgobot предлагает услуги по 3D-печати на заказ. В этом случае использовались фирменный высокотемпературный 3D-принтер Volgobot A4 PRO и филамент нашего производства — REC PEEK GF-30.
Задача
Описанная ниже работа выполнена в интересах предприятия, занимающегося разработками в сфере органической химии. Парк предприятия включает оборудование, подключаемое с помощью шлангов к цистернам с химикатами, например концентратами кислот, щелочей и спиртов. Шланги соединяются штуцерами и тройниками из POM-C или полиамида-6. Срок эксплуатации таких штуцеров составляет всего около одного месяца. Оборудование импортное, так что запчасти стоят дорого и поставляются со значительными задержками.
Задача Volgobot состояла в поиске подходящего материала и изготовлении штуцера с повышенным эксплуатационным сроком. Более того, переход на 3D-печатные варианты должен быть экономически обоснованным. Так как оборудование многофункциональное, то есть работает с разными видами химических веществ, использование разных полимеров для разных соединений не представлялось возможным, но нашелся один универсальный материал, способный выдерживать контакт с любыми из используемых химикатов — конструкционный термопласт полиэфирэфиркетон (PEEK).
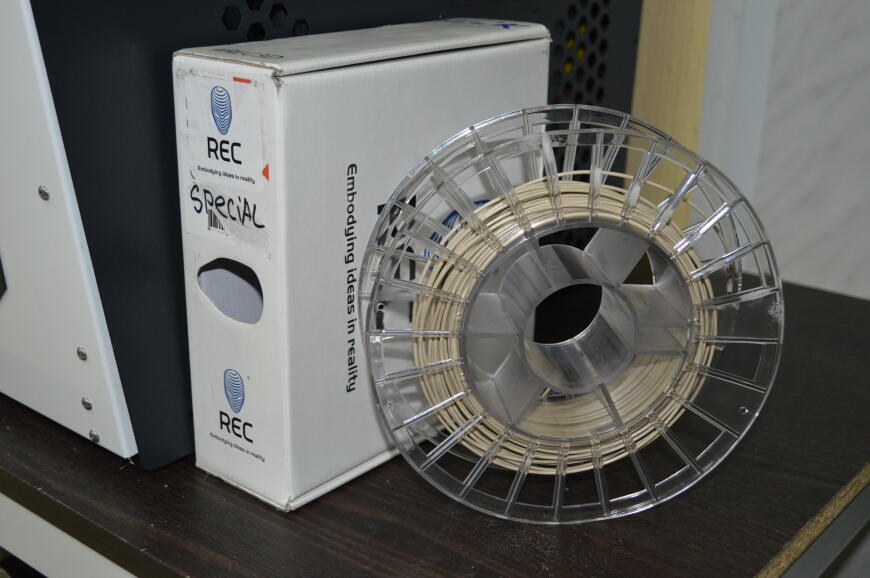
Свойства материала
Одно из главных преимуществ полиэфирэфиркетона и композитов на его основе — высокая термическая стойкость, превышающая 300°С. Само собой, это требует использования специализированного аддитивного оборудования, способного работать с тугоплавкими полимерами, например того же 3D-принтера Volgobot A4 PRO.
Помимо этого PEEK демонстрирует высокие механические и диэлектрические свойства, триботехнические характеристики, огнестойкость (V-0 по UL94), низкий уровень токсичности выделяемого при горении дыма, стойкость к радиационному излучению и, что особенно важно в этом проекте, исключительную химическую стойкостью.
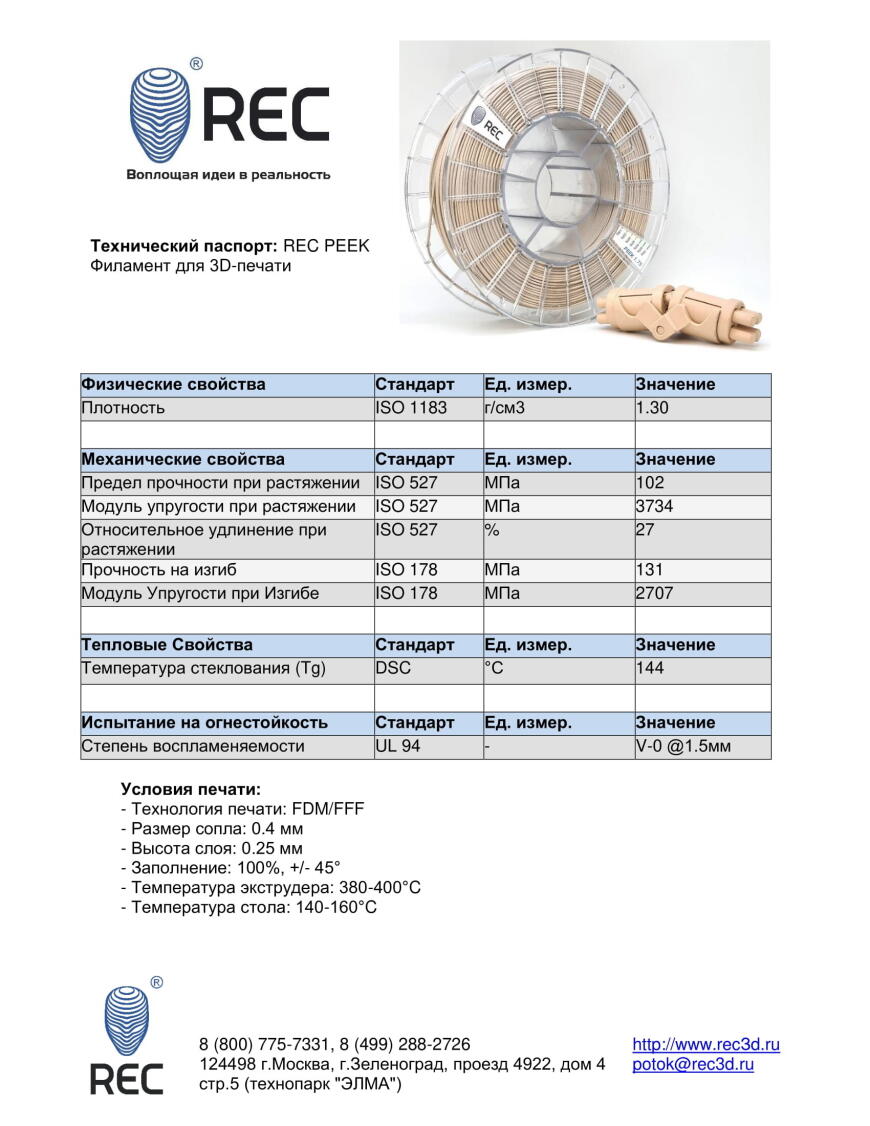
Главный недостаток PEEK — высокая стоимость. Один килограмм гранулята стоит от 25 000 рублей, цена филаментов выходит еще выше, а это отражается на себестоимости конечных изделий. Тем не менее, это вовсе не означает, что 3D-печатные детали из PEEK не могут окупать себя.
Второй недостаток — плохая межслойная адгезия. Эта проблема эффективно решается дополнительной термической обработкой, о чем мы расскажем ниже.
Подготовка к 3D-печати
Полиэфирэфиркетон, как и многие другие полимерные материалы, гигроскопичен, поэтому перед 3D-печатью филамент необходимо просушить. Сделать это можно разными методами, описанными в статье по этой ссылке, но в данном случае никакие ухищрения не потребовались, так как 3D-принтеры Volgobot A4 PRO оснащаются закрытыми камерами с активной регулировкой температуры. Термостатированную камеру прогрели до 100°С, а затем поместили внутрь катушку с филаментом на четыре часа.
Первый этап подготовки самого 3D-принтера — очистка рабочего столика и нанесение свежего адгезионного покрытия. Столик очищается от остатков материала после предыдущей работы, поверхность промывается бытовой химией. После высыхания поверхность необходимо протереть салфеткой с ацетоном или другим подходящим растворителем, смотря какой полимер использовался ранее.

На чистую поверхность необходимо нанести адгезионное средство. В этом случае использовался клей-карандаш. И команда Volgobot, и мы немало намучились с подбором подходящего средства, перепробовав различные варианты, в том числе импортные стоимостью свыше четырех тысяч рублей за баночку. Как это ни удивительно, в итоге оптимальным вариантом в плане эффективности и стабильности результатов оказался самый обычный клей-карандаш стоимостью порядка пятидесяти рублей, доступный в любом канцелярском магазине.
Настойки 3D-печати
Габариты изделия в нашем примере составляют 75х75х70 мм. Печать осуществлена соплом диаметром 0,6 мм со следующими настройками:
- высота слоя: 0,3 мм;
- высота первого слоя: 0,3 мм;
- ширина линий: 0,6 мм;
- количество линий стенки: 10;
- слои дна/крышки: 4;
- плотность заполнения: 100%;
- температура экструдера: 430°С;
- температура термокамеры: 140°С;
- температура платформы: 165°С;
- скорость печати: 40 мм/c;
- скорость печати стенок: 40 мм/c;
- ретракт: 0,5 мм;
- скорость ретракта: 30 мм/c;
- охлаждение: 0%;
- поток: 100%;
- вспомогательная адгезионная структура: кайма;
- дополнительное поле подложки: 10 мм.
Особого внимания требует термоусадка. При быстром охлаждении высок риск растрескивания по слоям и/или деформаций по краям изделия, потому в G-код необходимо прописать команду «M104 S165 G4 S60», чтобы по завершении 3D-печати камера и платформа синхронно охлаждались со 165°С до 140°С с темпом 1°С в минуту.
Итоговый набор инструкций:
- M141 S164
- G4 S60
- M141 S163
- G4 S60
- M141 S162
- G4 S60
- ...
- M141 S140
Затем вставляется часовая пауза для нормализации модели:
- G4 S3600
На завершающем этапе температура стола и термокамеры опускается с 140°С до 100°:
- M141 S139
- M140 S139
- G4 S60
- M141 S138
- M140 S138
- G4 S60
- M141 S137
- M140 S137
- G4 S60
- ...
- M141 S100
- M140 S100
Результат
Итог стараний — штуцер из PEEK GF-30, на на этом работа не завершена. Для повышения прочности изделию предстоит пройти дополнительную термическую обработку, то есть отжиг.

Отжиг
При наличии программируемой муфельной печи можно использовать следующий температурный цикл:
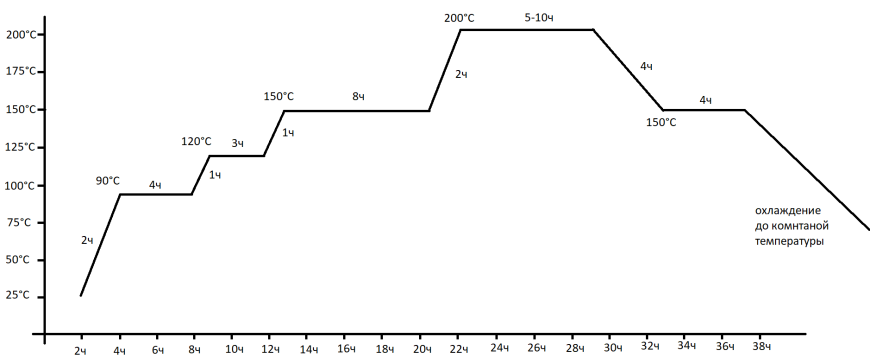
Если же муфельной печи нет, можно добиться приемлемых результатов подручными средствами. Потребуется железная тара, в которую необходимо уложить и утрамбовать слой песка толщиной в пару сантиметров, затем поместить внутрь деталь, засыпать песком доверху и снова утрамбовать.
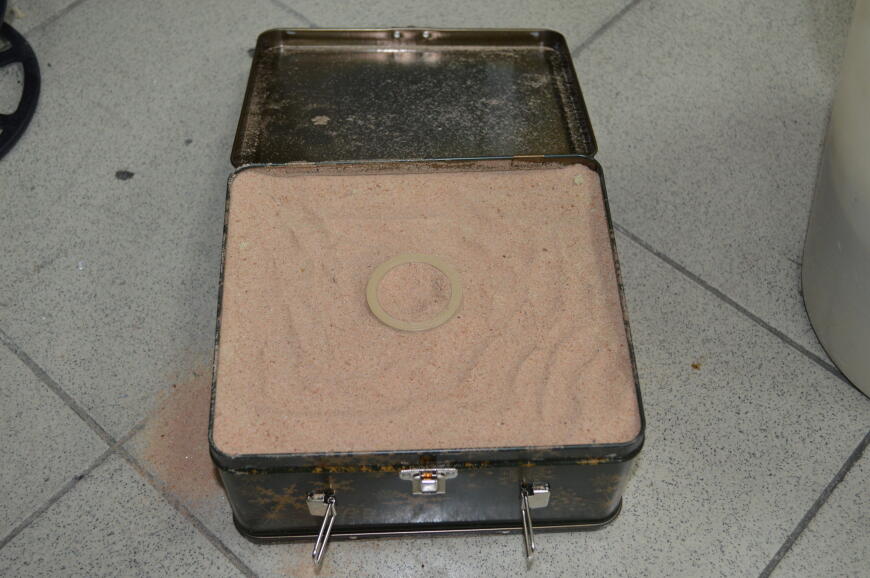
Полученная опока помещается в духовую печь, прогретую до 200°С, и выдерживается в течение трех суток. Затем печь необходимо выключить, дождаться полного остывания и только потом доставать готовую деталь.
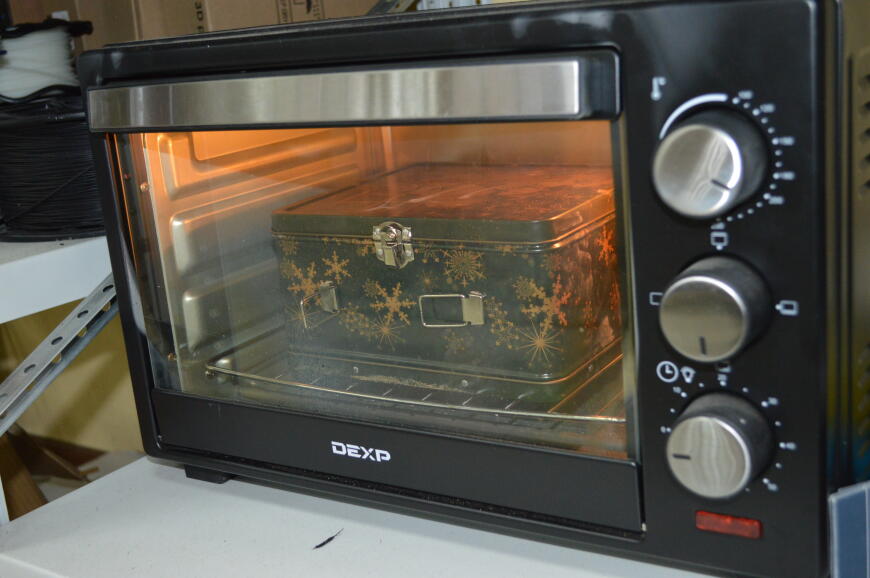
Этот метод тоже позволяет получать прочные детали, но с повышенным риском потери размерной точности.
Экономический эффект
Стоимость такой детали компания Volgobot оценивает в 10 198 рублей за штуку. Сумма немалая, но расчеты показывают выход на окупаемость в течение одного года. За прошедшие к этому времени четыре месяца эксплуатации опытного образца проблем не выявлено. Что не может не радовать, команда Volgobot утверждает, что наш вариант PEEK оказался самым стабильным в работе среди опробованных вариантов.
Чтобы написать отзыв нужно авторизоватся
Вход через социальные сети