Небольшое судно, спроектированное и напечатанное нашими партнерами из Перми, компанией F2 innovations, успешно прошло ходовые испытания. Цельный корпус лодки выполнен из нашего композита Ether GF на крупноформатном 3D-принтере F2 Gigantry.
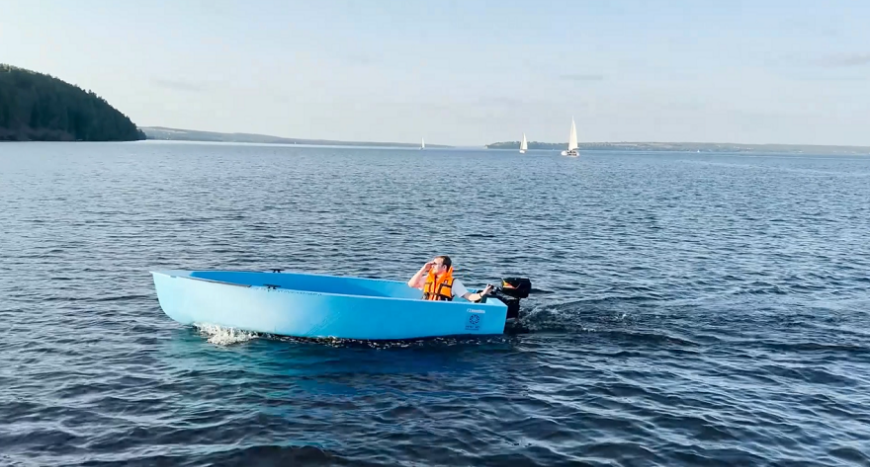
Проект реализован пермской компанией-производителем промышленных 3D-принтеров F2 innovations совместно с нашим научным подразделением — научно-производственным объединением 3D Solutions (НПО «3D Солюшнс»). С F2 innovations мы сотрудничаем уже достаточно давно: они создают средне- и крупноформатные экструзионные аддитивные системы по технологиям FDM (Fused Deposition Modeling) и FGF (Fused Granulate Fabrication), а 3D Solutions разрабатывает и поставляет расходные материалы. Наши совместные экспозиции можно было увидеть, например, на выставках «Композит-Экспо 2023» и «Металлообработка-2024».
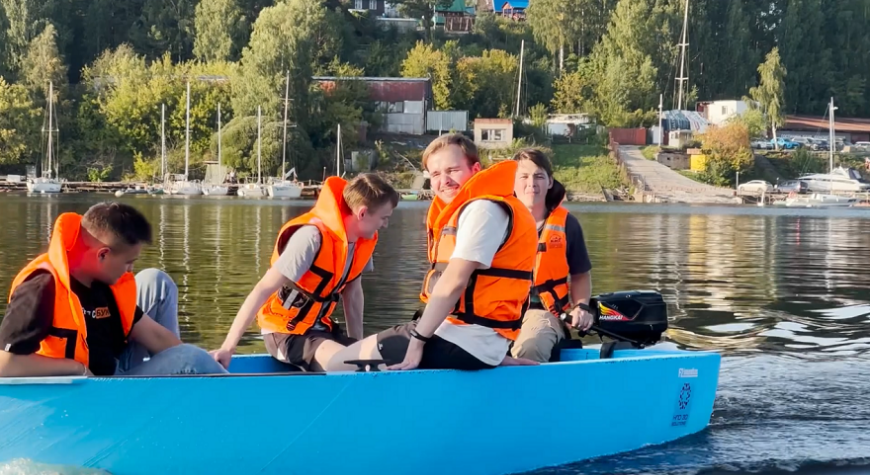
Лодку решили напечатать ради демонстрации возможностей аддитивных технологий в целом, а также оборудования от F2 innovations и расходных материалов от 3D Solutions в частности. Пермская команда самостоятельно спроектировала лодку, а затем вырастила корпус одной деталью на аддитивной системе F2 Gigantry. В стандартной конфигурации такие 3D-принтеры способны печатать изделия размером до 3,5х1,8х1,5 м, но при необходимости могут быть масштабированы вверх или вниз, смотря какие требования предъявляют заказчики. Конкретно в этом случае использовалась более крупная система с областью построения 6х2,5х1,8 м, при этом корпус лодки достигает четырех метров в длину при ширине примерно в полтора метра.
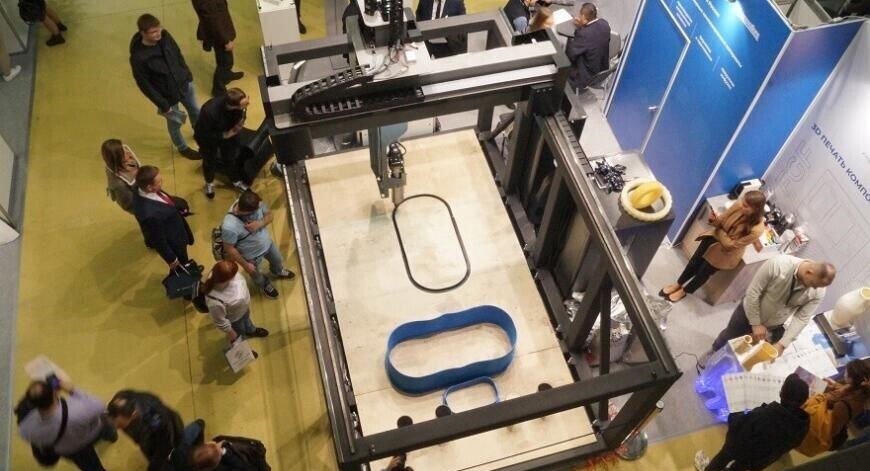
Материал укладывается шнековым экструдером с поэтапным, четырехзонным прогревом хотэнда, позволяющим добиваться высокой производительности без перегрева и деструкции полимера. На практике производительность экструдера F2 Pellet 8 достигает примерно десяти килограмм в час, а прогрев хотэнда до 450°С максимум позволяет работать даже тугоплавкими конструкционными термопластами, некоторые из которых по прочностным характеристикам способны заменять легкие сплавы. Расходными материалами служат гранулированные полимеры или армированные полимерные композиты, предварительно просушиваемые и подаваемые в экструдер пневматической системой.
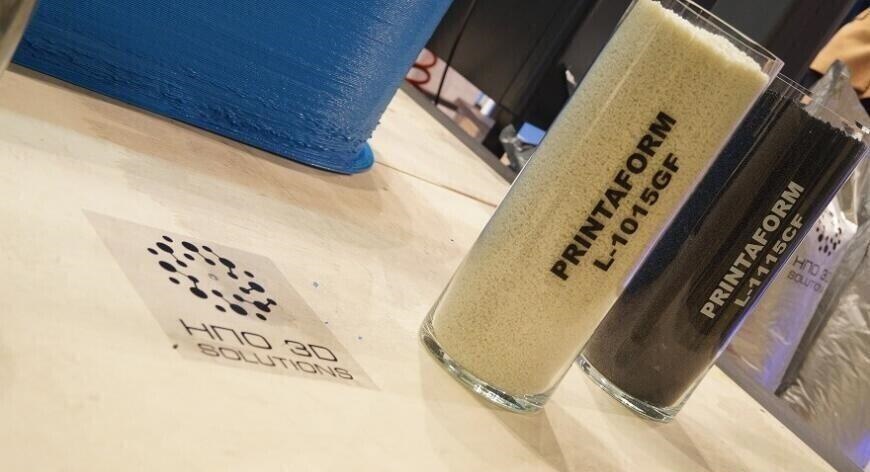
В этом случае использовался один из наших композиционных материалов — полиэтилентерефталатгликоль (PETG) с армирующим наполнителем из рубленого стекловолокна, предлагаемый 3D Solutions под наименованием Ether GF в составе линейки PrintaForm. У этого материала ряд преимуществ, включая высокую когезию слоев, низкую усадку и гигроскопичность, что важно для достижения высокой прочности и сохранения геометрии при построении крупногабаритных объектов, тем более эксплуатируемых на воде.
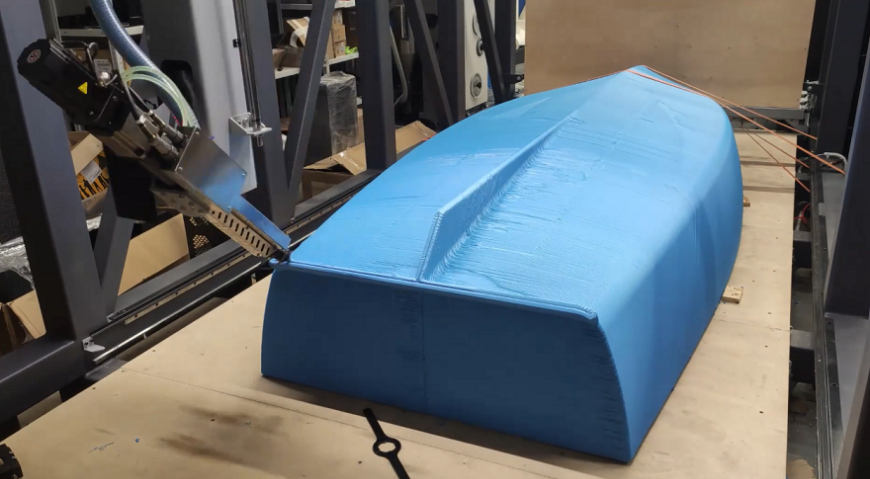
Еще один очевидный плюс Ether GF — относительно низкая стоимость, так как полимерная матрица на пятнадцать процентов состоит из переработанного полимера. На физико-механические свойства это практически не влияет, так как основная доля приходится на первичное сырье, зато повышает экологичность производства и позволяет предлагать материал по более доступной цене, что опять-таки немаловажно. Аналогичный материал доступен и в виде филамента под наименованием REC rPETG GF.
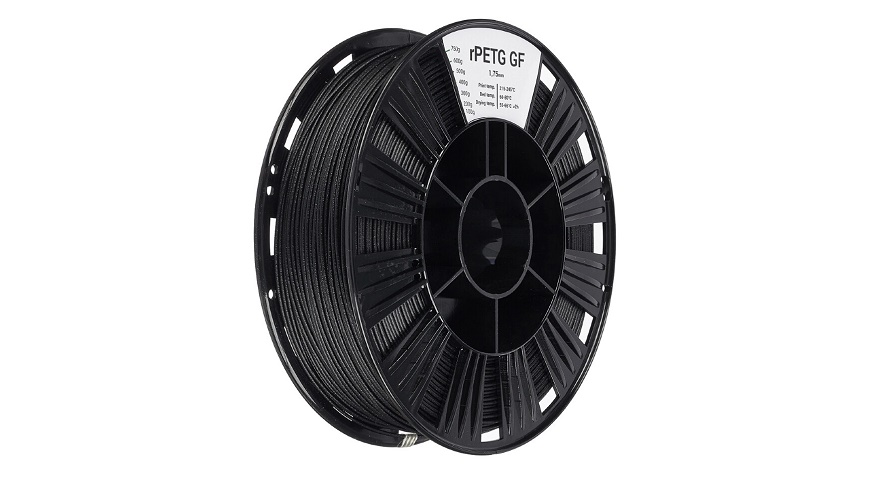
Один интересный момент проекта — способ построения. Как видно на иллюстрациях, укладка расплава производилась под углом в сорок пять градусов. Такая возможность обеспечивается поворотным креплением экструдера. Плюс в том, что при таком методе укладки снижается, а иногда даже полностью устраняется необходимость в поддержках при построении навесных структур. Здесь мы видим как раз такой случай — перевернутый вверх дном корпус, да еще и с внутренними полостями — отсеками непотопляемости, необходимыми для обеспечения безопасности экипажа.
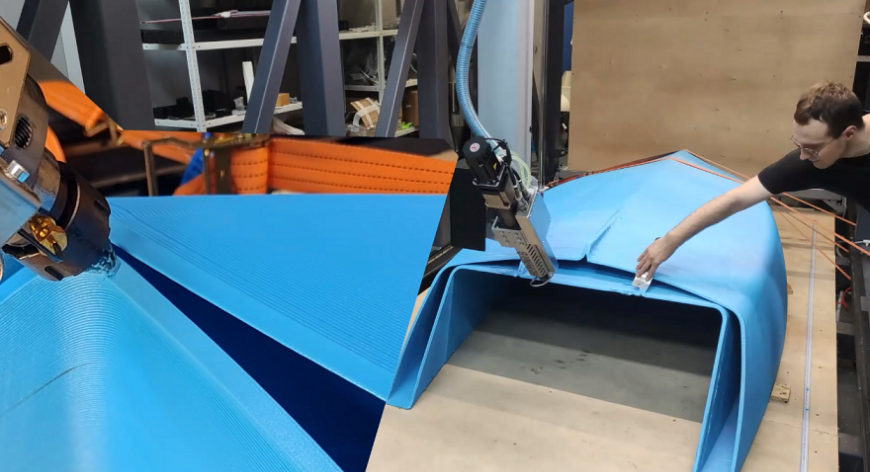
По завершении 3D-печати испытания провели на реке Каме. Лодку оборудовали транцевым электромотором мощностью 1,3 кВт с двумя аккумуляторами, а затем испытали сначала с одним человеком на борту, а затем с растущей нагрузкой, вплоть до полной из семи человек. Судно показало себя хорошо, с неплохой остойчивостью и грузоподъемностью, хотя максимальная скорость невелика — всего около десяти километров в час, но это уже вопрос мощности двигателя.
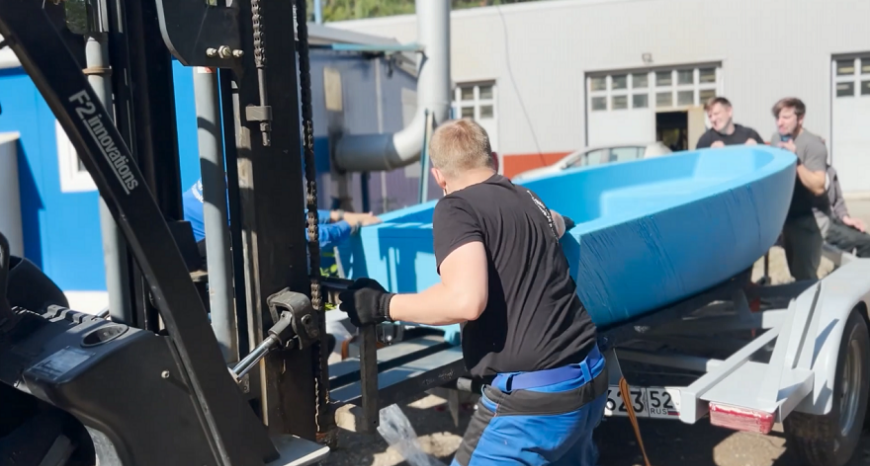
В целом задача выполнена: команде удалось получить крупногабаритное изделие массой около двухсот килограмм, четырехметровой длины и сложной геометрической формы, а затем успешно испытать лодку на воде. О серийном производстве речь не идет, это лишь демонстрация возможностей. На практике подобную крупноформатную 3D-печать было бы выгоднее использовать в производстве формовочной оснастки, а затем уже делать те же корпуса лодок, кузовные детали автомобилей и другие крупногабаритные детали из стекло- или углепластиков. Весь период разработки и создания опытной лодки — от концепции до готового изделия — занял всего пять дней.
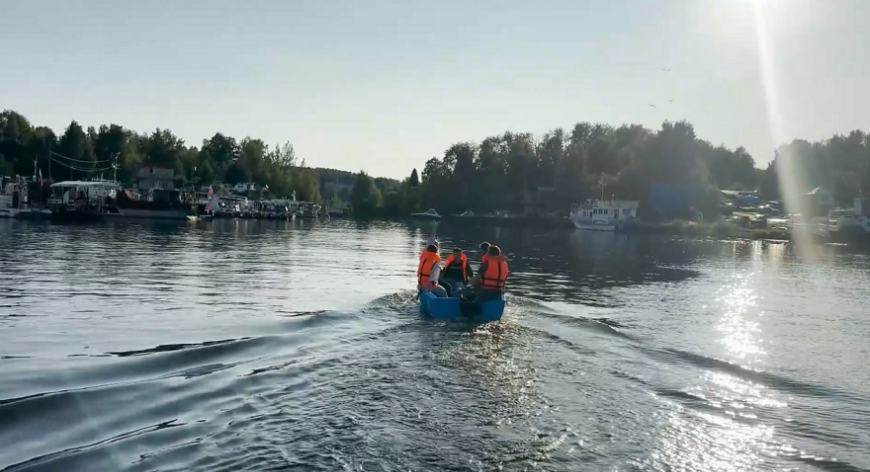
Если вас интересуют возможности крупноформатной экструзионной 3D-печати и расходных материалов, выпускаемых НПО «3D Солюшнс», посетите официальный сайт и свяжитесь со службой поддержки по электронной почте или телефону: наши специалисты будут рады предоставить подробную консультацию.
Чтобы написать отзыв нужно авторизоватся
Вход через социальные сети